Exploring the Advantages of Polyimide Composites
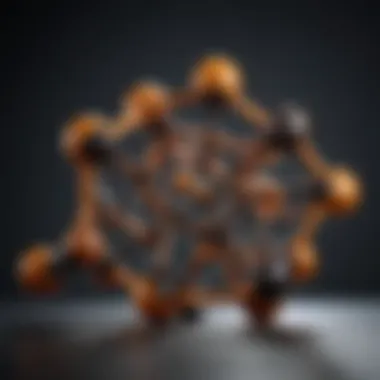
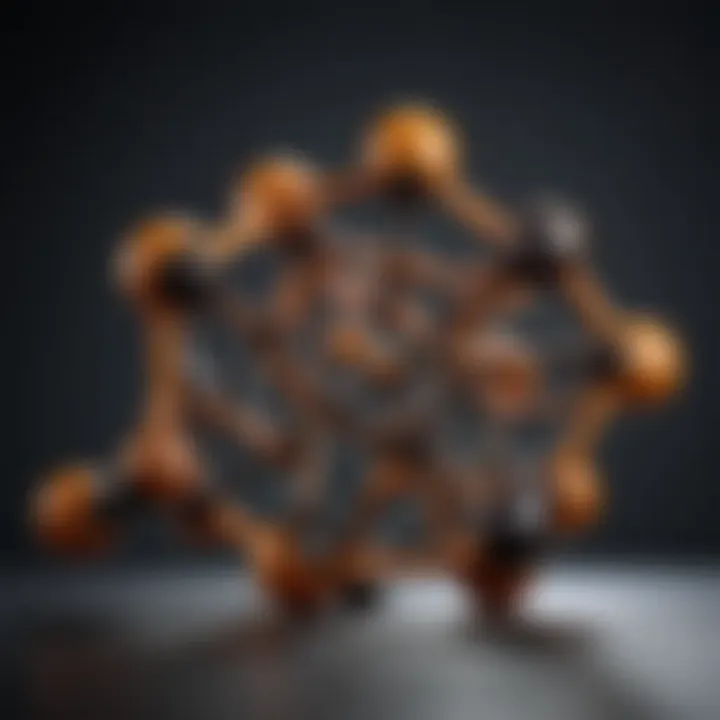
Article Overview
Polyimide composites represent a significant innovation in materials science, offering unique advantages across various industries. This article aims to illuminate the remarkable properties, applications, and recent advancements related to these composites. By dissecting the features and benefits of polyimide materials, the article will equip researchers, engineers, and industry professionals with thorough insights and knowledge relevant to polymer science and composite materials.
Purpose of the Article
The primary purpose of this document is to provide a deep understanding of polyimide composites. It goes beyond surface-level information, delving into the composition, properties, and manufacturing techniques that make these materials so valuable. Each aspect will be explored systematically to highlight why polyimides are increasingly relevant in high-performance applications.
Relevance to Multiple Disciplines
Polyimide composites cross various disciplines, including aerospace, automotive, electronics, and medical fields. Their unique properties, such as high-temperature stability and excellent chemical resistance, make them a preferred choice in demanding environments. This versatility underscores the importance of understanding these materials for professionals working in engineering, research and development, and manufacturing.
Research Background
Historical Context
The development of polyimide materials dates back to the mid-20th century. Initially synthesized for their excellent thermal and chemical properties, polyimides have evolved over decades. Their application in electronics and aeronautics received significant focus due to their ability to perform under extreme conditions. The rich historical context provides a framework to understand current trends and future directions in research.
Key Concepts and Definitions
A few key terms must be defined to navigate the discussion on polyimide composites effectively:
- Polyimide: A high-performance polymer known for its excellent thermal stability and mechanical properties.
- Composite: A material made from two or more constituent materials that have significantly different physical or chemical properties.
- Thermal Stability: The ability of a material to maintain its structural integrity under high temperatures.
Understanding these definitions sets the groundwork for a more detailed exploration of the properties and applications of polyimide composites.
Prelude to Polyimide Composites
In an era where material science is continually evolving, polyimide composites have emerged as crucial assets across various industries. Their unique properties—ranging from high thermal stability to excellent mechanical strength—render them indispensable in applications that demand resilience and performance. Understanding polyimide composites is vital for professionals in fields such as aerospace, electronics, and automotive industries, where reliability is paramount.
Polyimide composites are formulated by combining polyimide resins with reinforcing materials, ultimately enhancing their structural integrity. This unique composition manifests remarkable benefits over traditional polymers. Their versatility allows them to withstand extreme temperatures and harsh chemical environments, making them a favorable choice for innovative product designs.
Furthermore, as industries push for advancements, polyimide composites are increasingly seen as a solution to performance limitations encountered with other materials. Researchers and engineers are continuously exploring their properties and applications to unlock new possibilities and improve existing technologies.
Key Insight: Polyimide composites are not just materials; they represent an intersection of chemistry and engineering, driving forward advancements in various high-tech applications.
Key Insight: Polyimide composites are not just materials; they represent an intersection of chemistry and engineering, driving forward advancements in various high-tech applications.
Definition and Composition
Polyimide composites are defined as high-performance materials made by combining polyimide polymers with various reinforcements. The basic characteristic of polyimides lies in their repeating imide groups within their chemical structure, which contribute to favorable mechanical and thermal properties.
The composition of these composites typically involves the following components:
- Polyimide Resin: The backbone of the composite, offering durability and thermal stability.
- Reinforcing Agents: Commonly used materials include carbon fibers, aramid fibers, and glass fibers. These agents enhance the overall properties, such as strength and resistance to thermal degradation.
- Fillers and Additives: These substances may be included to further improve specific attributes such as electrical conductivity or fire resistance.
Through the strategic combination of these materials, polyimide composites achieve exceptional performance metrics, which is pivotal for their application in demanding environments.
History of Polyimide Development
The development of polyimides dates back to the mid-20th century, marking a significant milestone in material science. Initially, these materials gained attention due to their heat-resistant properties and resilience under various conditions.
In the 1960s, researchers like Dr. Hermann Staudinger contributed to the synthesis of polyimide chemistry, paving the way for their commercial use. The launch of DuPont’s Kapton in 1965 revolutionized the market, establishing polyimide as a material of choice for insulation in electrical applications.
Over the decades, further innovations have driven the research around polyimides. The focus has shifted towards enhancing their composite forms, integrating novel reinforcements and improving processing techniques. Today, the multidisciplinary approach involving chemistry, engineering, and application technology continues to push boundaries. This rich historical context underpins the relevance of polyimide composites in modern industry, ensuring continued exploration and advancements.
Chemical Structure of Polyimides
The chemical structure of polyimides plays a critical role in defining the material's properties and its applications across various industries. Understanding this structure aids in comprehending how polyimides can resist high temperatures and chemicals, which is essential for aerospace, electronics, and automotive sectors. The polymer's backbone, functional groups, and the type of monomers used in its composition significantly influence performance characteristics such as thermal stability, mechanical strength, and chemical resistance.
Types of Monomers
The monomers used to produce polyimides are key to determining their final properties. Common monomers include aromatic diamines and aromatic dianhydrides, which combine to form the polyimide structure. These components create a rigid backbone that contributes to their high thermal stability.
- Aromatic Diamines: Molecules such as 4,4'-diaminodiphenyl ether and p-phenylenediamine are frequently used. Their structure generally involves two amino groups attached to aromatic rings, leading to excellent thermal properties and rigidity.
- Aromatic Dianhydrides: Compounds like pyromellitic dianhydride and maleic anhydride provide the necessary chemistry for forming polyimides. They interact with the diamines to facilitate polymerization, forming imide linkages in the process.
The combination of these monomers allows for varied structures and, consequently, distinct physical properties in the resulting polyimide composites. Not only does this influence mechanical performance, but it also determines thermal and chemical behavior, which is vital for specific applications.
Polymerization Processes
The polymerization processes employed in creating polyimides significantly impact their molecular structure and properties. Two primary methods are noted: high-temperature imidization and low-temperature routes.
- High-Temperature Imidization: This method involves heating polyamic acids (precursors to polyimides) at elevated temperatures to achieve complete cyclization. Though it results in high-performance polymers, the thermal management during processing can be challenging due to the temperatures involved.
- Low-Temperature Routes: Newer approaches attempt to polymerize at lower temperatures, which can reduce energy costs and improve material handling. This provides a way to create polyimide composites with less shrinkage and stress during processing.
Key considerations include:
- Control Over Molecular Weight: The choice of polymerization influences the molecular weight of the polyimide, impacting its final mechanical attributes.
- Reaction Time: The duration of the reaction will also affect the chain length and cross-linking density, which directly correlates to the mechanical properties.
The selection of processes, therefore, governs the end-use of the material, showcasing the intricate relationship between polymer chemistry and practical performance in real-world applications.
Understanding the chemical structure of polyimides thus not only elucidates the characteristics of the materials but also enhances the approach towards innovation in their applications.
Understanding the chemical structure of polyimides thus not only elucidates the characteristics of the materials but also enhances the approach towards innovation in their applications.
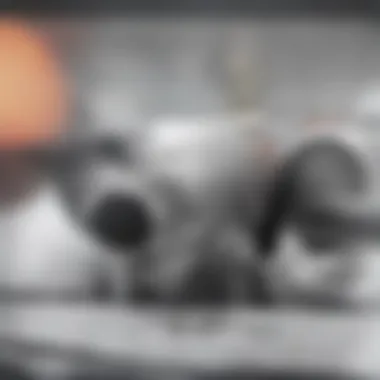
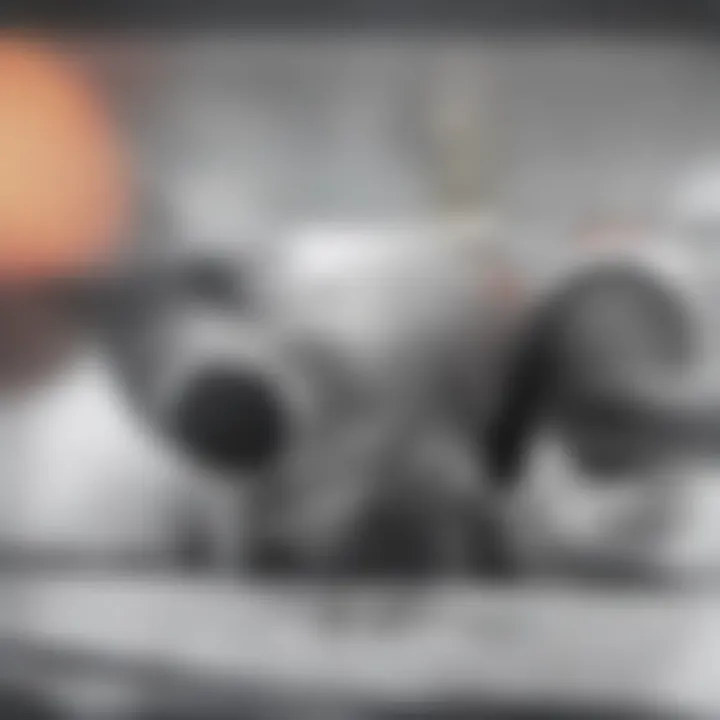
Properties of Polyimide Composites
Understanding the properties of polyimide composites is essential to appreciating their role in various applications. These materials exhibit unique attributes that distinguish them from other polymers, making them suitable for critical industries. Thermal stability, mechanical properties, and chemical resistance stand as the primary characteristics that define polyimide composites. Each of these properties contributes significantly to the functionality and usability of the materials in demanding environments.
Thermal Stability
Comparison to other polymers
Thermal stability is a standout feature of polyimide composites when compared to other polymer types, such as epoxies or polyesters. The increased thermal resistance of polyimides can be attributed to their unique chemical structure, allowing them to maintain their integrity at high temperatures. This high level of stability means that polyimides can be used in applications where heat is a significant factor.
In comparison, many conventional polymers begin to degrade at elevated temperatures, leading to potential failure. Polyimides do not exhibit the same rapid degradation, which marks them as a favorable choice for industries that require materials capable of withstanding extreme thermal environments. However, it is important to note that the high processing temperatures necessary for polyimide production may impact manufacturing costs and scalability.
Applications in high-temperature environments
Applications in high-temperature environments are a critical component of employing polyimide composites. Industries such as aerospace and electronics frequently experience conditions where materials are subjected to significant heat. Polyimide composites provide necessary solutions in these cases, enabling structural and functional components to operate effectively under such conditions.
This ability enhances their value in producing parts for jet engines and heat shields, where failure due to thermal effects can lead to catastrophic results. However, engineers must understand the limitations regarding specific temperature thresholds, as prolonged exposure beyond recommended limits could still risk material performance.
Mechanical Properties
Strength and durability metrics
The strength and durability metrics of polyimide composites represent a blend of resilience and reliability. These composites exhibit impressive tensile strength and resistance to mechanical stress. The high-performance characteristics of polyimides allow them to perform in applications where materials must endure significant forces without exhibiting permanent deformation.
This strength makes polyimide composites suitable for aerospace and automotive applications, where lightweight structures with high strength are essential. The downside is that while polyimides are strong, they may not exhibit the same levels of impact resistance found in some other materials, necessitating careful consideration of design applications.
Factors affecting mechanical performance
Several factors affect the mechanical performance of polyimide composites. These include temperature fluctuations, load types, and humidity levels. Polymer molecular weight, as well as the specific fillers and reinforcements used, can also play a pivotal role in dictating the mechanical behavior of the finished composite.
Understanding these factors is necessary for engineers to optimize the composite for specific applications. For instance, the inclusion of nanoscale fillers enhances strength but may also lead to variations in processing behavior. Balancing the mechanical performance with manufacturability is crucial in achieving desired outcomes with polyimide materials.
Chemical Resistance
Impact of environmental factors
The impact of environmental factors on polyimide composites’ chemical resistance is significant. Polyimides exhibit excellent resistance to a variety of chemicals, including solvents and oils, making them suitable for use in many industrial settings. Even under exposure to corrosive environments, polyimides maintain their structural integrity and functionality.
This property is particularly important in applications involving chemical processing, as deterioration from exposure to harsh substances can lead to failure. However, certain reactive chemicals may still pose risks to their longevity, and careful assessment is needed based on the specific chemical environment.
Applications against chemical exposure
Applications against chemical exposure capitalize on polyimide composites’ inherent resistance qualities. Industries such as chemical manufacturing and oil and gas frequently rely on these materials to create components like seals and casings that withstand aggressive substances without compromising performance.
By utilizing polyimide composites, firms can enhance safety and reliability while also reducing maintenance needs. Nonetheless, organizations must remain vigilant in monitoring material compatibility with specific chemicals to prevent unforeseen degradation during their lifecycle.
In summary, the properties of polyimide composites play a vital role in defining their numerous applications, highlighting their robustness in thermal stability, mechanical strength, and chemical resistance. Understanding these characteristics can guide researchers and professionals toward better designs and implementations in demanding conditions.
In summary, the properties of polyimide composites play a vital role in defining their numerous applications, highlighting their robustness in thermal stability, mechanical strength, and chemical resistance. Understanding these characteristics can guide researchers and professionals toward better designs and implementations in demanding conditions.
Manufacturing Techniques
The manufacturing of polyimide composites entails various techniques that shape their properties and performance. Understanding these techniques is crucial as they determine the final application of the composites in diverse fields. Each method offers specific benefits and considerations that impact production efficiency, cost, and the physical characteristics of the final product. Thus, it is important to explore different methods and their relevance to the overall manufacturing process.
Melt Processing Techniques
Melt processing techniques play a significant role in the production of polyimide composites. These methods allow for efficient shaping and molding of materials at elevated temperatures.
Injection molding
Injection molding is a popular method used in creating complex shapes with precision. It involves injecting molten polyimide into a mold where it cools and solidifies. This technique is highly valued for its ability to produce large quantities of identical parts quickly. One of its key characteristics is the adaptability it offers regarding design flexibility. Additionally, it allows for effective scaling of production operations. However, the initial cost for designing and fabricating the molds can be significant, which may limit its use in smaller production runs.
Extrusion methods
Extrusion methods involve forcing a heated polyimide mixture through a die to create continuous shapes, such as sheets or films. This technique is known for its efficiency and ability to produce long, uniform pieces of material. Extrusion is beneficial for manufacturing requirements where large volumes are essential. The main advantage is its consistent quality in output and lower production costs when compared to other methods. However, it may not be suitable for creating complex shapes or intricate details, which can be a limitation for some applications.
Solvent Casting Methods
Solvent casting methods are another avenue for producing polyimide composites. This method involves dissolving polyimides in a suitable solvent to form a liquid solution that can be poured into molds or spread onto surfaces.
Process overview
The process of solvent casting is relatively straightforward. After mixing the polyimide with the solvent, the solution is allowed to evaporate, leaving behind a solid composite. This approach is advantageous for making thin films or coating surfaces uniformly. The simplicity and low energy requirements of this method make it popular among manufacturers. However, controlling the thickness and uniformity can be challenging due to variations in solvent evaporation rates.
Advantages and disadvantages
While solvent casting offers distinctive advantages, it also presents challenges. The ability to create high-quality films and sheets is one advantage, thus allowing for high-performance applications. However, the presence of solvents poses environmental concerns and regulatory challenges. Additionally, the reliance on volatile solvents can lead to safety issues during the process, making it essential to ensure appropriate measures are in place.
Advanced Composite Fabrication
Advanced composite fabrication techniques are at the forefront of innovation within the polyimide composite industry, enabling the development of new applications.
Filament winding
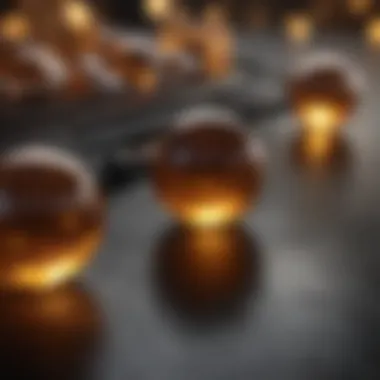
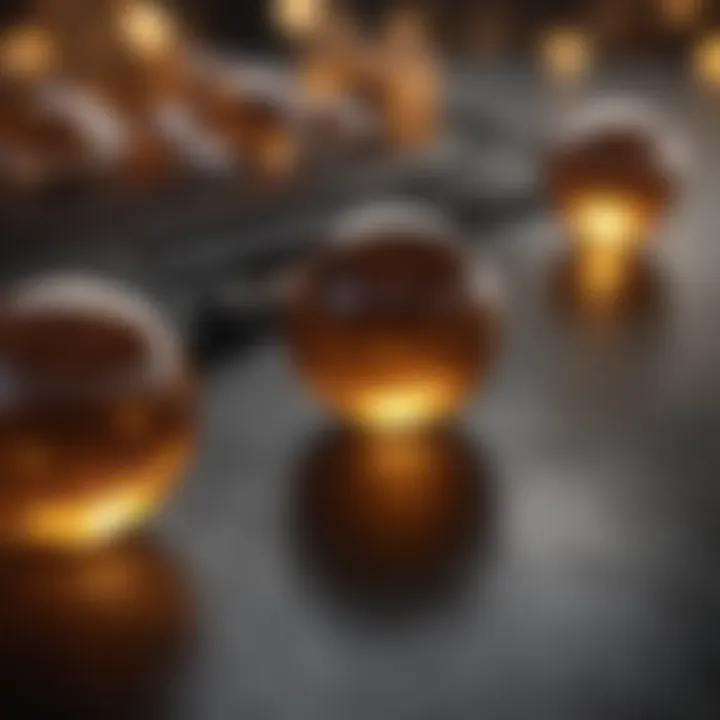
Filament winding entails wrapping continuous strands of polyimides around a rotating mandrel to form composite structures. This technique is mainly used in the production of high-strength tubes and pressure vessels. Its key characteristic is the ability to create parts with precise fiber alignment, improving the mechanical properties of the final product. The benefits of filament winding include producing composite components with excellent strength-to-weight ratios. Nonetheless, the equipment needed for this method can be costly, which may hinder adoption for some manufacturers.
3D printing developments
3D printing developments represent a significant evolution in composite fabrication. This method allows for additive manufacturing of polyimide parts layer by layer, providing a high level of design freedom. Its main advantage is the reduction in material waste compared to traditional subtractive processes. Furthermore, 3D printing can facilitate rapid prototyping, allowing for quicker iterations of designs. However, maintaining consistent quality and ensuring robust mechanical properties can be a challenge, as the technology is still maturing.
Polyimide composites hold promise for advancing manufacturing processes, underpinned by various techniques that drive innovation and efficiency.
Polyimide composites hold promise for advancing manufacturing processes, underpinned by various techniques that drive innovation and efficiency.
Applications of Polyimide Composites
Polyimide composites are fundamental in modern engineering and technology due to their exceptional properties which make them suitable for a myriad of applications. This section emphasizes the diversity and importance of applications across various industries. Understanding these applications not only sheds light on the material's innovative uses but also highlights its potential for future developments. Key features such as thermal stability, mechanical strength, and chemical resistance enhance their benefits, making them preferred choices in sectors like aerospace, electronics, and automotive.
Aerospace Industry
Use in aircraft components
The use of polyimide composites in aircraft components is vital for enhancing performance and safety. These materials contribute significantly to weight reduction while maintaining structural integrity. A key characteristic of polyimide composites is their low weight coupled with high strength, which is crucial in aerospace applications where every gram counts. This attribute makes them a beneficial choice for manufacturers looking to improve fuel efficiency. Additionally, the unique feature of polyimide composites is their exceptional heat resistance, allowing aircraft to operate in high-temperature environments without compromising safety.
Performance under extreme conditions
Polyimide composites demonstrate remarkable performance under extreme conditions, specifically in environmental and thermal extremes. This characteristic is essential for aerospace applications, where components need to endure fluctuations in temperature and pressure. Their thermomechanical stability sets them apart in this sector, making them a popular choice for manufacturers aiming to enhance the reliability of components like engine parts and structural elements. However, one must consider that while polyimide composites excel in these conditions, specific grades may incur higher costs in comparison to other materials.
Electronics and Insulation
Thermal management solutions
In electronics, thermal management solutions using polyimide composites play a crucial role in enhancing device reliability. The ability of these materials to conduct heat effectively while remaining electrically insulating allows for improved thermal conductivity. This feature is significant for reducing heat accumulation in electronic devices. Their effective insulation properties also make them quite valuable in various applications, including circuit boards and flexible printed circuits. However, balancing thermal conductivity with insulation can sometimes be a challenge, and requires careful selection of composite materials for optimal performance.
Insulation properties in electrical applications
Polyimide composites are renowned for their outstanding insulation properties, which are particularly important in electrical applications. Their high dielectric strength ensures minimal electric current leakage, which can be detrimental in sensitive electronic devices. This property is fundamental for ensuring long-term reliability and performance in applications such as transformers and capacitors. While these materials provide several benefits, the cost of production can be higher than alternative insulating materials, thereby necessitating a careful cost-benefit analysis by manufacturers.
Automotive Applications
Lightweight construction benefits
Lightweight construction benefits are pivotal in the automotive industry, driving the adoption of polyimide composites. By using these materials, automotive manufacturers can reduce the overall weight of vehicles, which subsequently leads to enhanced fuel efficiency and performance. A key characterstic of this application is the composites' high strength-to-weight ratio, making them an ideal choice for critical components like body panels and structural elements. Despite these advantages, the integration of such materials can involve significant investment in new manufacturing processes.
Durability in automotive components
The durability of polyimide composites in automotive components contributes to the longevity and reliability of vehicles. Their resistance to temperature extremes and chemical exposure allows them to withstand harsh driving conditions. This unique feature translates to reduced maintenance costs and longer service life, providing significant advantages for both manufacturers and consumers. However, challenges such as material costs and potential lifecycle impacts may influence their adoption across all automotive applications.
"The versatility of polyimide composites across multiple sectors showcases their potential for further innovations and research, which could reshape material applications in the future."
"The versatility of polyimide composites across multiple sectors showcases their potential for further innovations and research, which could reshape material applications in the future."
Research and Developments
Research and developments in polyimide composites represent a pivotal area in material science. Advancements in this field can lead to significant improvements in efficiency, sustainability, and performance. This section will explore the emergence of innovative technologies that continue to enhance polyimide materials, as well as the push towards sustainable production practices. Both of these components are vital for ensuring polyimide composites meet the demands across various industries today.
Emerging Technologies
Nano-reinforced composites
Nano-reinforced composites involve incorporating nanomaterials into polyimide matrices to enhance mechanical and thermal properties. This specific aspect has drawn considerable interest for its potential to bolster the performance of polyimide composites beyond traditional capabilities. The key characteristic of nano-reinforced composites is the significant improvement in strength and stiffness achieved at relatively low loadings of nanoscale fillers.
A popular choice in this field is the integration of carbon nanotubes or graphene oxide. These nanomaterials provide unique features, such as exceptional electrical conductivity and remarkable thermal properties, making the composites suitable for advanced applications. However, they also present challenges related to processing and dispersion within the polymer matrix, which can affect the uniformity and consistency of the final product.
Smart material integration
Smart material integration signifies the incorporation of materials that can respond dynamically to environmental changes. In the context of polyimide composites, this technology allows for the development of self-sensing and self-healing capabilities. The key characteristic of smart materials in this context lies in their ability to monitor structural integrity and adapt to conditions, which is beneficial for maintaining performance in critical applications.
The unique feature of smart material integration is its potential to enhance the durability and reliability of polyimide composites. For example, these materials can provide real-time feedback on stress or temperature changes, informing maintenance needs. However, the complexity of these systems can introduce new challenges in terms of cost and manufacturing processes, possibly limiting widespread adoption.
Sustainability in Polyimide Production
Environmentally friendly processes
The push for environmentally friendly processes in polyimide production reflects the growing recognition of the importance of sustainable practices in manufacturing. This specific aspect emphasizes reducing harmful emissions and waste throughout the production cycle. The key characteristic of environmentally friendly processes is their focus on using renewable resources and avoiding toxic solvents, making them a preferable choice for eco-conscious manufacturers.
Unique features of these methods include the application of alternative polymerization methods, such as solvent-free synthesis techniques. These processes can lead to a lower environmental impact. However, challenges may arise in scaling up such methods for commercial applications, necessitating further research and development to optimize efficiency.
Recycling and end-of-life considerations
Recycling and end-of-life considerations play an essential role in the sustainable lifecycle of polyimide composites. This aspect focuses on the feasibility of recycling polyimide materials and minimizing waste post-consumption. The key characteristic of effective recycling methods involves the ability to reclaim and reuse materials, which can significantly reduce overall resource use and environmental impact.
Unique features in this area include the development of depolymerization techniques, which allow for breaking down polyimides into their monomer units. This offers a potential pathway for reusing materials in new applications. However, the practical application of these methods remains a challenge, potentially limiting their effectiveness unless further explored in real-world scenarios.
"The future of polyimide composites hinges on integrating advanced technologies with sustainable practices."
"The future of polyimide composites hinges on integrating advanced technologies with sustainable practices."
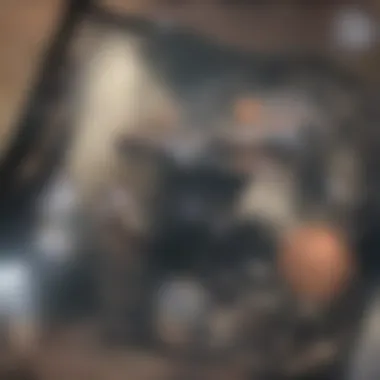
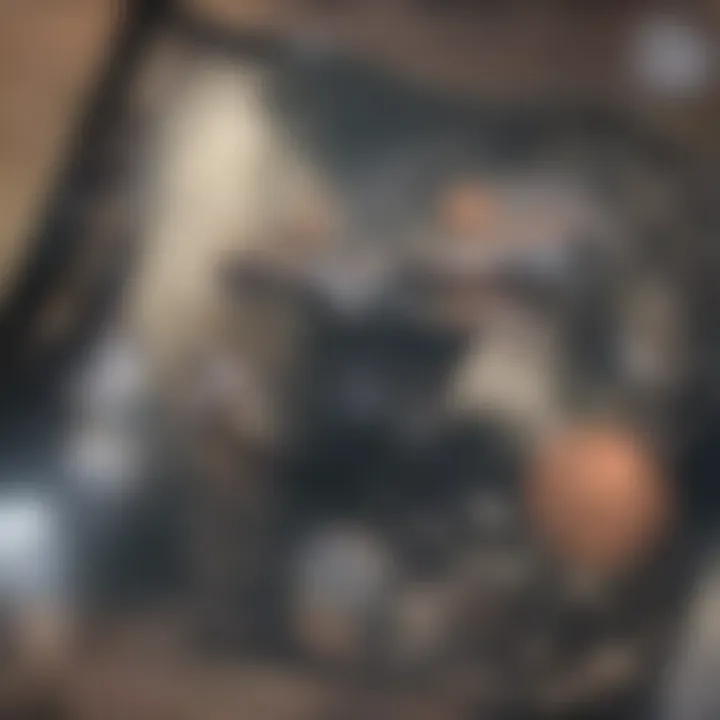
The integration of these advancements are vital for creating a more sustainable and efficient future for polyimide composites, ensuring they continue to meet the evolving demands of various industries.
Challenges in Polyimide Composite Applications
The incorporation of polyimide composites into various industries presents several challenges that must be taken into consideration. Understanding these challenges is crucial for optimizing production and application technologies. Two primary areas of concern include manufacturing limitations and performance constraints. Addressing these issues requires both technical knowledge and innovative solutions to ensure polyimide composites meet the high expectations of modern applications.
Manufacturing Limitations
Cost implications
Cost implications represent a significant hurdle in the wide-scale adoption of polyimide composites. The synthesis of polyimides typically involves intricate processes and specialized raw materials. These factors contribute to higher production costs compared to other polymers. For manufacturers, this aspect becomes a crucial consideration, as it directly impacts pricing strategies and market competitiveness. The complex manufacturing processes also necessitate skilled labor and sophisticated equipment, further driving costs. Despite these challenges, companies that invest in optimizing production can benefit from the unique properties of polyimide composites in high-performance applications.
Material availability
Material availability is another critical element affecting the production of polyimide composites. The sourcing of specific monomers and precursors is often limited by geographic and market constraints. Suppliers may have fluctuating capacities, leading to potential delays and increased costs. This scarcity can hinder large-scale production and affect project timelines. However, ongoing advancements in material science and changes in supply chain dynamics may offer solutions, making polyimide composites more accessible in the future.
Performance Constraints
Heat aging effects
Heat aging effects are vital to understanding the longevity and reliability of polyimide composites in applications subjected to high temperatures. Prolonged exposure to elevated temperatures can result in alterations to the physical and mechanical properties of polyimides. These changes can manifest as reduced strength or flexibility, which are critical factors for performance. Awareness of these limitations ensures that engineers can select appropriate materials for specific applications, ultimately fostering a deeper understanding of polyimide behavior under stress.
Mechanical degradation challenges
Mechanical degradation challenges involve the wear and tear that polyimide composites experience under operational conditions. Factors such as environmental exposure, load stress, and frequency of use significantly influence the degradation processes. Understanding these challenges is beneficial for developers, as it allows for the optimization of material configurations and design. In this context, extensive testing and research can guide improvements in mechanical stability, ensuring reliable performance in demanding environments.
"Polyimide composites offer immense potential, but addressing their challenges is essential to unlock their full capabilities in practical applications."
"Polyimide composites offer immense potential, but addressing their challenges is essential to unlock their full capabilities in practical applications."
By tackling the manufacturing limitations and performance constraints surrounding polyimide composites, industries can harness their inherent advantages while ensuring that issues do not hinder their practical applications.
Future Directions in Polyimide Composite Research
The research landscape for polyimide composites is evolving rapidly. As industries demand materials that meet high-performance standards, the focus on future directions in polyimide composite research has gained immense importance. Novel developments in this field address both material properties and manufacturing processes. Researchers are tasked with enhancing the overall utility of polyimide composites while considering sustainability and efficiency.
Innovations in Material Science
Exploring new polymer chemistries
The exploration of new polymer chemistries is critical in the advancement of polyimide composites. This involves investigating the properties and behaviors of different chemical structures. New polymer building blocks can lead to polyimides with tailored characteristics, such as improved thermal stability and mechanical strength. The key characteristic of these new materials is their ability to be designed from the molecular level up. This focused approach makes them particularly appealing for engineering applications where precision is crucial.
A unique feature of exploring new polymer chemistries is the versatility it provides. It opens avenues for creating materials that maintain performance under challenging conditions. However, the complexities involved in synthesizing these new polymers may present some disadvantages, including increased production costs and longer lead times for development.
Fabrication method innovations
Innovations in fabrication methods play a significant role in the evolution of polyimide composites. Current trends focus on enhancing traditional methods and integrating novel techniques that can improve production efficiency and quality. Key characteristics of these innovations include the adoption of additive manufacturing processes, such as 3D printing. This allows for the creation of complex geometries that were poorly accessible with conventional methods.
Such advancements create opportunities for lightweight structures without sacrificing strength. However, these processes may require specialized equipment and materials, which can impact the overall cost structure of production.
Interdisciplinary Research Opportunities
Collaborative studies with other materials
Engaging in collaborative studies with other materials enhances the knowledge framework surrounding polyimide composites. Researchers are increasingly working across disciplines to fuse polyimides with other composite materials, creating hybrids that can exhibit enhanced properties. This approach allows for a more robust analysis of the performance potentials of polyimide composites.
The unique feature of such collaborations lies in their ability to tackle complex engineering challenges, paving the way for innovative solutions. However, there is a risk that the integration process may lead to unforeseen complications in the material's behavior or overall manufacturability.
Integration with emerging technologies
Integration with emerging technologies has the potential to transform the applications of polyimide composites. Technologies such as machine learning and artificial intelligence are informing predictive models about material behaviors under various conditions. The ability to simulate performance can significantly reduce the time frames associated with material development and testing.
This integration not only speeds up research but can also lead to more sustainable practices through refining processes and material usage. There is a caveat, though; reliance on these technologies might require substantial investments in infrastructure and training.
In summary: Future directions in polyimide composites research will require a combination of innovative chemistry, advanced fabrication methods, and interdisciplinary collaborations to unlock their full potential. The pathway is complex but filled with opportunities to enhance performance and sustainability.
In summary: Future directions in polyimide composites research will require a combination of innovative chemistry, advanced fabrication methods, and interdisciplinary collaborations to unlock their full potential. The pathway is complex but filled with opportunities to enhance performance and sustainability.
End
The conclusion of this article delves into the essential points surrounding polyimide composites. This section serves to consolidate the variety of information shared throughout the previous sections. A clear synthesis of insights provides the reader with a firm understanding of polyimide composites' role and significance across industries.
In summary, polyimide composites are notable for their unique properties such as high thermal stability, mechanical strength, and chemical resistance. These characteristics make them invaluable in applications ranging from aerospace to electronics. The exploration of their chemical structure, manufacturing techniques, and advancements in research underscores the importance of ongoing innovation in this field. The improved understanding of these attributes opens doors for new applications, thus benefiting various sectors.
Moreover, the advancements and challenges identified in these materials suggest a promising yet cautious journey ahead. The need for continuing research is evident, particularly in finding sustainable production methods and enhancing performance capabilities.
Polyimides are expected to remain a leading material in the high-tech landscape due to their versatile use and unmatched qualities.
Polyimides are expected to remain a leading material in the high-tech landscape due to their versatile use and unmatched qualities.
Summary of Key Insights
This article highlights several key insights regarding polyimide composites:
- Thermal Stability: Polyimide composites can withstand high temperatures with minimal degradation, which is critical in applications where materials are subjected to extreme conditions.
- Mechanical Properties: They exhibit significant strength and durability, making them suitable for demanding environments.
- Chemical Resistance: These composites withstand a range of chemical exposures, providing reliability in harsh conditions.
- Manufacturing Techniques: Various processes such as melt processing and solvent casting enable tailored production of polyimide composites.
- Applications Across Industries: From aerospace components to automotive durability, the range of applications confirms their vital role.
- Future Research Needs: Innovation is crucial, especially concerning sustainable practices and interdisciplinary approaches to material science.
Call for Further Research
The field of polyimide composites requires ongoing study and exploration. Future research should focus on:
- Sustainability: Developing more environmentally-friendly production processes and investigating recycling possibilities of polyimide composites.
- Performance Enhancement: Finding ways to optimize mechanical and thermal properties to extend service life in practical applications.
- Nano-reinforced Materials: Investigating how nano-reinforcements can improve existing polyimide composites.
- Integration with Other Materials: Exploring synergistic applications with new technologies and materials to enhance functionality.