Exploring HIPIMS Sputtering: Mechanisms and Applications
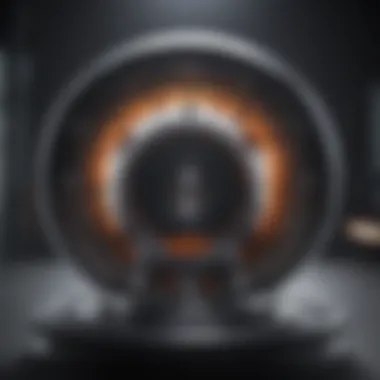
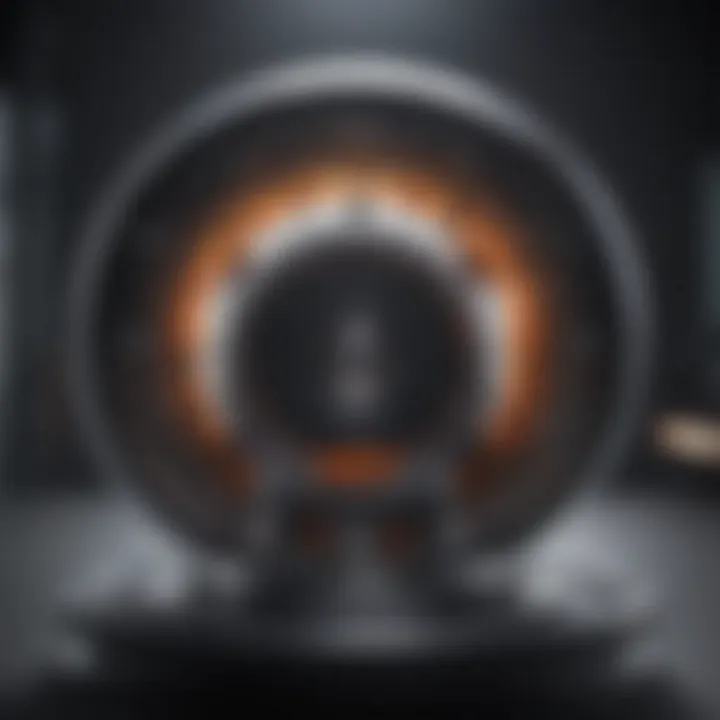
Article Overview
Purpose of the Article
The primary aim of this article is to dissect the multifaceted domain of High-Intensity Pulsed Magnetron Sputtering (HIPIMS). As a notable advancement in material deposition techniques, HIPIMS stands out due to its ability to produce superior coatings with enhanced performance characteristics. We intend to lay out the mechanical underpinnings, such as plasma dynamics and ionization processes, behind HIPIMS sputtering. This understanding serves as a cornerstone for anyone interested in material science, whether for academic pursuits or professional applications.
Relevance to Multiple Disciplines
HIPIMS is not just a buzzword in the material science realm; its implications stretch far and wide. From electronics to defense industries, the technology finds applications where precise coatings are essential. Researchers will find it applicable in studies ranging from semiconductor fabrication to the creation of robust wear-resistant surfaces. Thus, this article serves as a vital resource for students, educators, and professionals across various fields, underscoring its significance not only in academic circles but also within the industry.
Research Background
Historical Context
To truly grasp the innovation that HIPIMS brings, one must first recognize the challenges faced by earlier sputtering techniques. Conventional magnetron sputtering faced limitations regarding the control of plasma parameters and ionization rates, which often hampered the quality of deposited films. The dawn of HIPIMS, born out of the need for higher ionization and energy efficiency, brought a paradigm shift. As researchers began to delve deeper, they found that pulsing the power applied to the target could significantly enhance the ionization of sputtered material. This historical backdrop sets the stage for appreciating the advancements that HIPIMS now embodies.
Key Concepts and Definitions
Diving into HIPIMS requires a basic understanding of some essential concepts:
- Sputtering: A process where atoms are ejected from the target material due to bombardment by energetic ions.
- Magnetron: A device that utilizes magnetic fields to confine plasma, enhancing the efficiency of sputtering.
- Pulsing: In HIPIMS, power is delivered in short bursts, allowing for greater control over the plasma environment and ionization.
Together, these terms carve out the framework for understanding HIPIMS technology. The importance of these foundational pieces cannot be overstated, as they guide not only theoretical exploration but practical application as well.
"In essence, HIPIMS pushes the envelope in material deposition, paving new avenues for research and commercial utility."
"In essence, HIPIMS pushes the envelope in material deposition, paving new avenues for research and commercial utility."
As we delve deeper into the nuances of HIPIMS technology, the upcoming sections will unfold its mechanisms, applications, and promising innovations, creating a tapestry of knowledge that enriches our comprehension of this field.
Prologue to HIPIMS Sputtering
The realm of material science is ever-evolving, and among the various innovative techniques, High-Intensity Pulsed Magnetron Sputtering (HIPIMS) has carved a niche that stands out. This section is centered on introducing HIPIMS sputtering, which is pivotal for both academia and industry. Understanding its intricacies is vital not just for grasping how materials are deposited but for comprehending the implications of such technologies in refining products and processes.
HIPIMS is a specialized form of magnetron sputtering characterized by its unique ability to generate high-density plasma. This capability opens a plethora of opportunities in terms of applications and advancements. Many industries, including microelectronics, optics, and biomedical, are witnessing transformative changes due to HIPIMS. It allows for the deposition of thin films with exceptional qualities like enhanced adhesion, density, and uniformity, thus leading to superior performance in final products.
Moreover, as we delve deeper into this technique, we will uncover the historical context that shaped its development and the mechanisms that underpin its operation. Knowledge of HIPIMS not only enriches oneās understanding of material deposition technologies but also cultivates the ability to innovate further in this field.
The benefits of understanding HIPIMS extend beyond the basic mechanics; they touch on the advances in efficiency and precision that this technique allows. For those in research or industry, a firm grasp of HIPIMS can inspire novel applications and improvements in existing systems. Often, it's the finer details that make the most significant impact in material sciences, and HIPIMS is a testament to that.
Definition of HIPIMS
High-Intensity Pulsed Magnetron Sputtering (HIPIMS) refers to a sputtering technique that utilizes pulsed power to generate high-density plasmas. Unlike traditional sputtering, which may produce lower ionization levels, HIPIMS enables the emission of a vast amount of ions within short bursts of energy. This intermittent release of high power results in a more efficient ionization of the sputtered material, leading to superior film properties.
The driving force behind HIPIMS lies in its operational principleāby oscillating power supply, it allows for pause and surge moments in energy delivery. This provides self-regulation of the plasma environment and optimizes the film growth rate, ultimately producing thin films that have desirable qualities such as high density and enhanced adhesion to the substrate.
Historical Developments
HIPIMS didn't emerge overnight; it is a culmination of years of research and technological advancements in the field of sputtering. The roots of sputtering trace back to the mid-20th century when initially, magnetron sputtering was devised to improve the deposition processes used in electronics.
However, it was not until the late 1990s that the concept of HIPIMS began to gain traction. Early studies showcased the techniqueās potential for creating thin films with unexpected properties, capturing the attention of researchers. A notable landmark in this journey was the development of power supplies capable of delivering the intense pulses required for HIPIMS. With each advancement in equipment and understanding of plasma dynamics, the applicability of HIPIMS has broadened, now touching various fields such as protective coatings and microelectronic applications.
In recent years, as the demand for advanced materials grows, HIPIMS has garnered interest across academia and industry.
The rich history of HIPIMS highlights the journey of exploration that continues to unveil more possibilities for future advancements. As we move further in this article, we will explore the core principles that make HIPIMS a game-changer in material processing, its comparative advantages over conventional sputtering methods, and its diverse applications.
Fundamental Principles of HIPIMS
Understanding the fundamental principles of High-Intensity Pulsed Magnetron Sputtering (HIPIMS) is vital, as it lays the cornerstone for comprehending how this advanced technique operates. These principles not only highlight the intricate mechanics involved in HIPIMS but also spotlight the advantages it offers over traditional sputtering methods.
One specific element is the sputtering mechanism itself. It drives the deposition process, determining how effectively materials are transferred from a target to a substrate. Hence, grasping these mechanisms can help researchers innovate and improve applications across multiple fields.
Mechanisms of Sputtering
The mechanisms of sputtering in HIPIMS are a blend of physics and engineering that make the process distinct. At its core, sputtering refers to the ejection of atoms from a target material when it is bombarded with energetic ions. In HIPIMS, this bombardment happens in a highly controlled environment where the pulse duration and intensity of the power supply are crucial.
During each pulse, a high-density plasma is generated, leading to a significant increase in the number of ions available for collision with the target. This results in a more efficient removal of material from the target, thereby improving the deposition rate. The enhanced ionization also means that the sputtered atoms can gain kinetic energy to travel further before landing on the substrate, leading to denser and more uniform coatings.
Consider the following points about this mechanism:
- Dual Ionization: Both ions and neutrals are responsible for the sputtering process. This dual process can increase the quality of the deposited film.
- Temperature Control: The pulsed nature of the process allows for better thermal management, preventing overheating issues that often arise in continuous sputtering operations.
Role of Pulsed Power
The role of pulsed power in HIPIMS is a key factor in enhancing the efficiency and quality of the deposition. By operating the power supply in pulses, the system can achieve very high peak powers while keeping the average power at manageable levels. This allows for a marked increase in electron density without excessive thermal load.
Such pulsed power contributes significantly to several outcome measures:
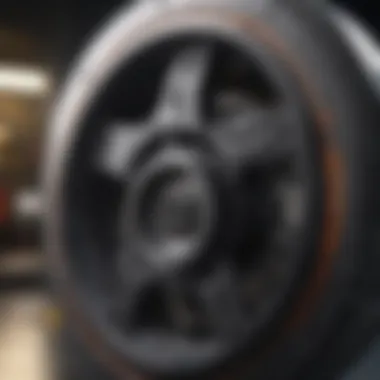
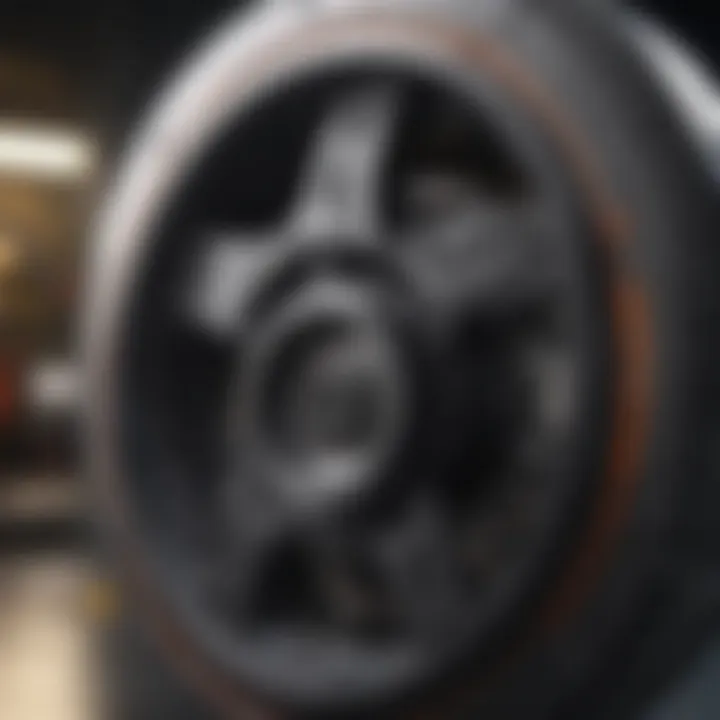
- Increased Ionization: The peaked power enables higher ionization rates, ultimately improving the deposition of materials with improved morphology.
- Enhanced Control: The ability to adjust pulse lengths and frequencies provides precise control over the sputtering parameters, tailoring outcomes for specific applications.
In practice, when the pulse duration is carefully optimized, it can lead to a more stable plasma regime during deposition. This translates to films that not only adhere better but also possess superior performance characteristics.
Magnetron Configuration
The configuration of the magnetron in HIPIMS is another crucial element. The arrangement and design of the magnetron affect how the plasma is maintained and controlled. In a standard magnetron sputtering setup, magnetic fields are used to confine electrons close to the target, amplifying the ionization process.
In HIPIMS, the geometry and magnetic field configurations are designed strategically:
- Enhanced Field: A stronger magnetic field can be employed to elongate the electron travel path, increasing the chance of ionization and maintaining a robust plasma discharge.
- Target Geometry: Specific target shapes and materials can be chosen to optimize the interaction with the plasma, further enhancing film quality.
"A well-designed magnetron can make all the differenceāit's the engine that drives the sputtering race."
"A well-designed magnetron can make all the differenceāit's the engine that drives the sputtering race."
The interplay between the target's material properties and the applied magnetic field can dictate the growth rate and morphology of the deposited films. Therefore, investigating various configurations can unlock potential improvements in film performance, especially in specialized applications like microelectronics and optical coatings.
In summary, understanding the fundamental principles of HIPIMS extends beyond merely knowing the process. It involves a deep appreciation for the complex mechanisms at play, the pivotal role of pulsed power, and the implications of magnetron configurationāall of which contribute to its defined superiority over traditional sputtering methods. This foundational knowledge is essential for researchers and professionals looking to push the boundaries of material science.
Comparative Analysis with Traditional Sputtering Techniques
In the realm of materials science, the ongoing push for more efficient and effective deposition techniques has brought High-Intensity Pulsed Magnetron Sputtering (HIPIMS) to the forefront. Understanding its merits compared to traditional sputtering methods sheds light on its potential impact across several industries. This comparison highlights not just the sophisticated aspects of HIPIMS, but also its practical implications in real-world applications.
Advantages of HIPIMS
HIPIMS shines in several areas that elevate it above conventional sputtering methods. One critical advantage is its ability to achieve higher ionization levels. Traditional sputtering relies largely on lower energy processes, which sometimes leads to inadequate film quality and properties. In contrast, HIPIMS utilizes high-power pulses that not only increase the ionization of sputtered material but also enhance film density and adhesion.
- Improved Film Quality: The energetic conditions during HIPIMS lead to denser films with fewer defects compared to traditional methods. In semiconductor applications, this can mean better performance and reliability.
- Material Versatility: HIPIMS can deposit a broader range of materials, including alloys and compounds, while preserving their unique properties. This advantage is significant in the electronics and optics sectors, where material integrity is paramount.
- Thickness Control: By toggling the pulse duration and frequency, HIPIMS allows precise control over film thickness, catering to specific engineering needs.
Moreover, energy efficiency is also a noteworthy benefit. While traditional sputtering consumes substantial power for prolonged periods, HIPIMS pulses deliver energy in a targeted manner, reducing overall wastage. These aspects underscore the profound advancements found in HIPIMS, making it a game-changer.
Limitations of Conventional Methods
While traditional sputtering methods have their merits, they present challenges that increasingly become stumbling blocks in applications demanding high precision.
- Lower Ionization Rates: Conventional techniques generally produce fewer ions, which can compromise film quality. Specific techniques, such as DC magnetron sputtering, often yield films that do not adhere well, resulting in reduced durability.
- Restricted Materials: Certain materials are difficult to deposit through these traditional means. They may lead to phase changes or alter the desired characteristics when subjected to the uniform energy distribution employed in common sputtering techniques.
- Performance Scaling: The ability to scale traditional methods often comes at the price of decreased film quality, as increasing deposition rates can lead to stress accumulation within the films. This can result in delamination or cracking, contrary to the goals of high-performance applications.
"In the ever-competitive landscape of material sciences, adopting advanced methods like HIPIMS could be the key to keeping pace with evolving industry demands."
"In the ever-competitive landscape of material sciences, adopting advanced methods like HIPIMS could be the key to keeping pace with evolving industry demands."
Applications of HIPIMS Sputtering
Understanding the various applications of High-Intensity Pulsed Magnetron Sputtering (HIPIMS) is crucial for grasping its value in modern material science. HIPIMS serves as a crucial bridge between theoretical principles and practical applications, making it a game changer across different industries. Its unique properties lead to numerous benefits such as enhanced film quality, improved adhesion, and broader materials versatility.
Let's delve deeper into some key fields where HIPIMS is making a profound impact.
Microelectronics and Semiconductors
The microelectronics sector stands to gain immensely from HIPIMS technology. As electronic devices become smaller and more complex, the necessity for high-quality thin films in semiconductor fabrication escalates. HIPIMS enables the deposition of films with superior structural integrity and uniform thickness.
- Exceptional Film Density: The high ionization rate of the sputtered material leads to denser films, essential for performance in microelectronics.
- Reduced Defect Density: The precise control over the deposition process minimizes defects in thin films, which can be crippling in semiconductor devices.
- Tailored Material Properties: With HIPIMS, itās possible to engineer films for specific electrical, thermal, and mechanical properties, allowing for innovative designs and improvements in product performance.
Optical Coatings
In the realm of optical coatings, HIPIMS has emerged as a robust method for creating thin films that enhance the performance of lenses and mirrors. This has significant repercussions not just in consumer electronics but also in scientific instruments.
- High Reflectivity: Coatings produced via HIPIMS can achieve high reflectivity which is crucial in applications requiring minimal light loss.
- Durability: Films deposited using this technique tend to be more resistant to environmental factors, prolonging the lifespan of optical devices.
- Customized Optical Properties: The ability to produce tailored thin films allows for the development of innovative products like anti-reflective coatings, filters, and beamsplitters that can perform under varying conditions.
Biomedical Devices
The biomedical field is remarkably diverse, and HIPIMS plays a pivotal role in advancing the functionality and biocompatibility of medical devices.
- Biocompatible Coatings: The use of HIPIMS enables the creation of coatings that are safer for implantation in human tissues, addressing significant issues of rejection and inflammation.
- Enhanced Properties: Films can be tailored to exhibit specific electrical properties necessary for devices like biosensors, supporting their effective operation.
- Longer Lifespan of Devices: Protective coatings help increase the resistance of implants and devices to wear and corrosion, which is vital for longevity in biomedical applications.
Magnetic Materials
HIPIMS is a breakthrough in the field of magnetic materials by enabling innovations that refine the performance of magnetic films.
- Improved Magnetic Properties: The high ionization degree during deposition contributes to enhanced magnetic characteristics of thin film materials.
- Applications in Data Storage: The technology can be applied in the production of high-density data storage systems, where magnetic films must be durable and efficient.
- New Material Combinations: Researchers can now explore new magnetic alloys and configurations that were not feasible before due to traditional sputtering limitations.
Moreover, the rise of HIPIMS is not just limited to these applications. It embodies a shift towards more advanced, efficient technologies in various industries, paving the way for innovations that we can only begin to imagine.
"With every advancement in sputtering technology, we inch closer to more robust materials that define the future of numerous sectors."
"With every advancement in sputtering technology, we inch closer to more robust materials that define the future of numerous sectors."
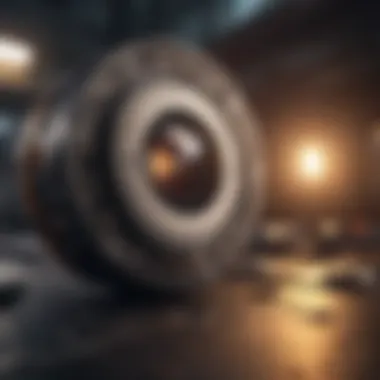
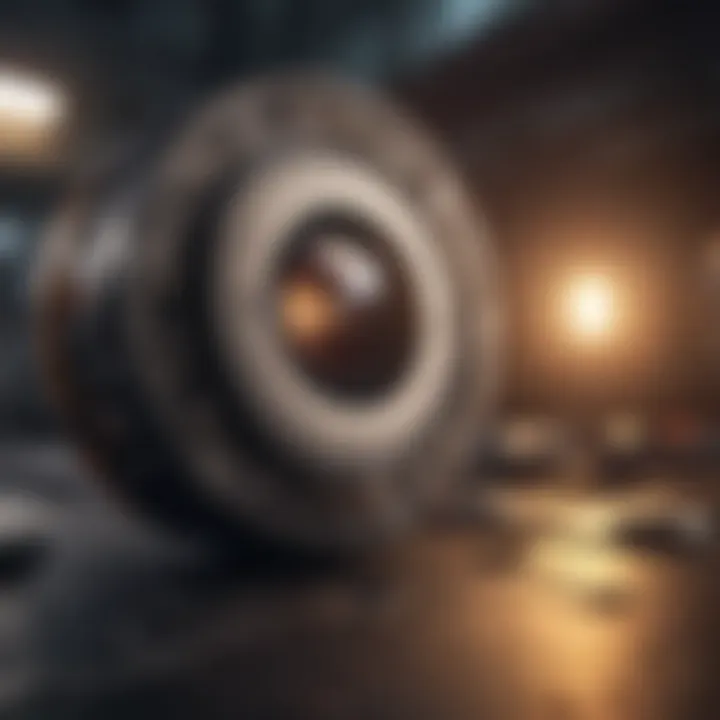
So, as we move forward, it's essential to not only recognize where we stand today with HIPIMS sputtering but also how it pushes boundaries in material science and technology.
Technological Innovations in HIPIMS
The realm of High-Intensity Pulsed Magnetron Sputtering (HIPIMS) is constantly evolving, driven by technological innovations that enhance its capabilities and applications. As we delve into this critical area, it becomes clear that advancements not only refine the sputtering process but also broaden its industrial and scientific horizons. The importance of these innovations stems from their potential to increase efficiency, material quality, and adaptability in various applications.
Advancements in Equipment Design
Recent strides in equipment design for HIPIMS are vital to unlocking its full potential. The shift towards more compact and modular systems reflects a trend in engineering that favors versatility and ease of integration. For instance, the development of hybrid systems that combine conventional sputtering with HIPIMS techniques allows for a more flexible approach to coating substrates.
Notable improvements can be seen in the design of magnetron sources, resulting in increased control over plasma parameters. Adaptive magnetic field configurations not only optimize ionization rates but also allow for precise tuning of deposition rates. This leads to better uniformity in film thickness across various types of substrates, which is crucial for high-performance applications in microelectronics and optical coatings.
Unique features such as integrated real-time diagnostics are also becoming more common. This capability ensures that operators can monitor key performance metrics and make adjustments on-the-go, ultimately improving the overall process efficiency.
Process Optimization Techniques
The optimization of processes in HIPIMS is another cornerstone of its advancements. Enhancing deposition processes can translate into significant improvements in film characteristics and substrate interactions. Implementing variable pulse durations and tailored duty cycles is one technique gaining traction. By fine-tuning these parameters, researchers can alter energy delivery, impacting how atoms interact during the deposition process.
Utilizing feedback systems for real-time adjustments during sputtering has shown promise as well. These systems can analyze film growth and provide instantaneous data, allowing immediate optimizations that reflect specific requirements of the material being deposited.
"Process optimization is not just about speed; itās about achieving the right balance between quality and functionality."
"Process optimization is not just about speed; itās about achieving the right balance between quality and functionality."
The integration of computational modeling is also transforming how researchers approach HIPIMS. Simulations can predict outcomes based on varying conditions, saving time and resources during experimentation. As such, the synergy between theoretical models and practical application is helping to forge a path toward more innovative uses of HIPIMS in developing advanced materials.
Together, these advancements in equipment design and process optimization techniques signify a significant leap forward in HIPIMS technology. They offer not only improved performance but also open doors to new applications that were previously out of reach. As the technology matures, the implications for industries such as aerospace, healthcare, and energy generations will be profound, showcasing the transformative potential of HIPIMS in the scientific world.
Experimental Techniques for Studying HIPIMS
In the realm of High-Intensity Pulsed Magnetron Sputtering (HIPIMS), understanding the fundamental mechanisms and properties at play can significantly enhance both academic research and industrial application. Experimental techniques for studying HIPIMS serve as the backbone for insightful investigations into how plasma dynamics influence material properties. This section will outline the essential techniques employed to characterize the sputtering process and monitor the plasma dynamics, thus providing a cohesive understanding of the operational intricacies of HIPIMS.
Characterization Methods
When it comes to materials science, the term "characterization" refers to the array of methods used to analyze and understand the properties of thin films and coatings developed through HIPIMS. Techniques such as X-Ray Diffraction (XRD), Scanning Electron Microscopy (SEM), and Atomic Force Microscopy (AFM) play crucial roles in evaluating the film morphology, crystal structure, and surface roughness.
Key Characterization Techniques:
- X-Ray Diffraction (XRD): This method allows researchers to identify the crystalline phases within the deposited films, proving significant in understanding the impact of HIPIMS on the filmās physical structure.
- Scanning Electron Microscopy (SEM): SEM provides detailed images of the film surface and helps ascertain uniformity and particle distribution, which is critical in applications like microelectronics.
- Atomic Force Microscopy (AFM): AFM enables assessment of surface features at nanoscale resolutions, allowing researchers to detect changes in surface roughness and texture influenced by the sputtering conditions.
Characterization does not merely provide qualitative data but is essential for establishing predictive correlations between process parameters and the ultimate properties of the films produced. For individuals embarking on research or development projects, these methods clarify the outcome variables, enabling informed adjustments that optimize film quality.
Monitoring Plasma Dynamics
Monitoring plasma dynamics is pivotal in understanding the efficiency and effectiveness of the HIPIMS technique. The gas-phase phenomena, like ionization fraction and plasma density, directly influence the quality of the coating achieved. Optical Emission Spectroscopy (OES) and Langmuir Probes are amongst the vital tools used to monitor these dynamics closely.
Key Monitoring Techniques:
- Optical Emission Spectroscopy (OES): OES allows researchers to analyze the light emitted from the plasma, providing insights into ion composition and temperature. By monitoring specific emission lines, scientists can deduce properties such as electron density and electron temperature, which are essential for optimizing the process conditions.
- Langmuir Probes: These devices measure the current in response to an electric field, offering direct data on plasma characteristics. Langmuir Probes allow one to explore parameters like electron density and energy distribution in the sheath region, critical for understanding the interaction between particles and substrates.
Monitoring the plasma dynamics is not just about gathering data; itās about utilizing that data to refine the HIPIMS process. Understanding how various parameters influence ion bombardment and the subsequent film growth can lead to the development of more efficient and cost-effective systems.
The integration of advanced characterization and monitoring techniques in HIPIMS is redefining our approach towards material deposition, paving the way for innovative applications across multiple sectors.
The integration of advanced characterization and monitoring techniques in HIPIMS is redefining our approach towards material deposition, paving the way for innovative applications across multiple sectors.
Impact of HIPIMS on Material Properties
The relevance of understanding the impact of HIPIMS on material properties in this article cannot be overstated. As a cutting-edge technology, High-Intensity Pulsed Magnetron Sputtering has made significant strides in modifying and enhancing materials at various levels. These changes are not just superficial; they can deeply affect the performance and applicability of materials in diverse fields.
In particular, HIPIMS affects critical elements such as film density and structure, as well as the mechanical and chemical properties of coatings. By studying these factors, researchers can unlock new capabilities in material science, leading to innovations that can translate into practical applications.
Film Density and Structure
Film density and structure are paramount in determining the quality of the coatings produced by HIPIMS processes. Unlike traditional sputtering methods, HIPIMS operates at much higher power densities and uses pulsed technology, which significantly influences how materials are deposited.
- Increased Density: The high-energy conditions promote an increase in the density of thin films. Denser films tend to exhibit superior mechanical strength and durability, making them suitable for demanding applications.
- Columnar Structure: In HIPIMS, due to the high ionization levels, films often show a columnar structure which directly relates to their performance. These columns can also result in enhanced adhesion properties, which are critical in applications like microelectronics and optics.
- Controllable Morphology: Researchers have noted that adjustment in process parameters like pulse frequency can lead to control over microstructural properties. For example, varying the pulse duration can lead to smooth, feature-rich surfaces or even nanostructured materials.
Understandably, having a grip on how film density and structure are influenced by HIPIMS is crucial for future innovations in material applications.
Mechanical and Chemical Properties
The mechanical and chemical properties of materials deposited via HIPIMS further amplify the significance of this technology. As materials are increasingly required to perform under harsher conditions, understanding these properties becomes essential in material design and selection.
- Enhanced Hardness and Wear Resistance: Studies reveal that coatings produced through HIPIMS tend to show increased hardness compared to those created by conventional methods. This hardness translates into higher resistance to wear, making HIPIMS an attractive option for protective coatings used in various industries.
- Improved Adhesion: High adhesion strength is essential, particularly in applications like functional coatings in the semiconductor and optical industries. HIPIMS, by virtue of its unique operating principle, can effectively enhance adhesion at the interface between the substrate and the coating, thereby improving overall performance.
- Corrosion Resistance: Materials coated with HIPIMS processes often exhibit improved resistance to corrosion. This is largely due to the dense structure and minimized porosity found in the films produced. Corrosion resistance is vital in industries such as automotive, aerospace, and biomedical, where long-lasting materials are performed in challenging environments.
"The ability to tailor material properties through HIPIMS not only pushes the envelope in material science but also sets a new standard in practical applications across various industries."
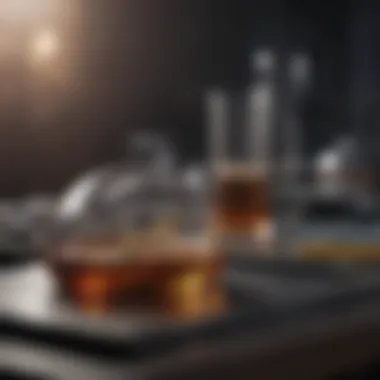
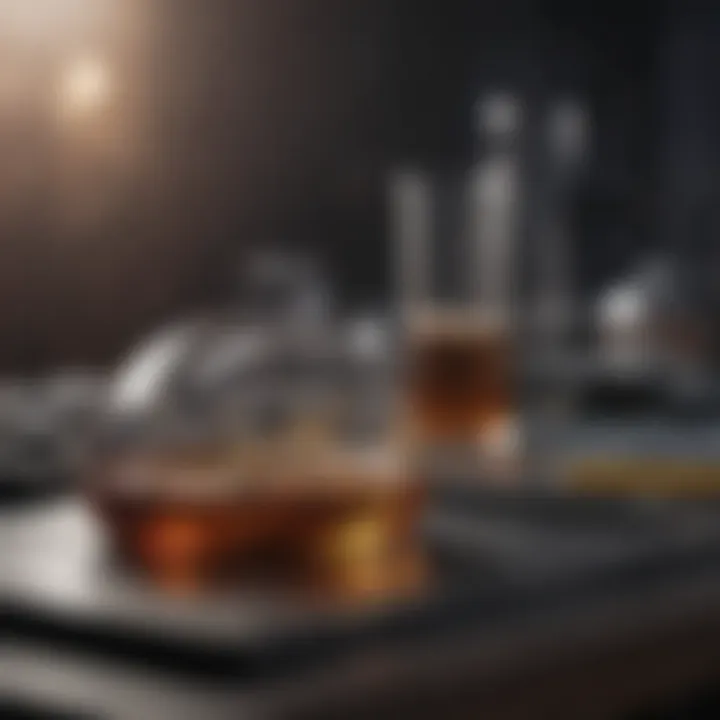
"The ability to tailor material properties through HIPIMS not only pushes the envelope in material science but also sets a new standard in practical applications across various industries."
In summary, the impact of HIPIMS on material properties is multi-faceted and profound. By careful management of the deposition parameters, researchers and professionals can engineer materials that meet the stringent demands of modern technology. As we move forward, this understanding will pave the way for innovative solutions and advancements in numerous domains.
Future Directions in HIPIMS Research
The exploration of High-Intensity Pulsed Magnetron Sputtering (HIPIMS) has opened a plethora of possibilities in material science. As industries push for more advanced materials and tailored properties, the future directions in HIPIMS research are critical. They are not simply twists and turns in research; they represent the forefront of how processing techniques can evolve to meet the demands of advancing technologies.
Understanding the future directions allows researchers and practitioners to foresee potential breakthroughs and reconfigure existing methodologies. The relevance of this discussion benefits professionals involved in both academic research and industrial applications, creating a fertile ground for innovation.
Emerging Trends and Applications
The landscape of HIPIMS is changing rapidly, and several emerging trends are shaping its applications. Here are some key trends to keep an eye on:
- Advanced Coatings: The demand for coatings with specific functionalities, such as anti-corrosive properties or enhanced adhesion, is driving research into customized HIPIMS processes. Tailoring deposition parameters could lead to coatings that outperform existing solutions in durability.
- Nano-Structured Materials: Research is increasingly focused on using HIPIMS to create nano-structured materials. The versatility of HIPIMS allows for precise control over the film's microstructure, which can enhance mechanical properties and performance in applications like wear-resistant coatings and biomedical implants.
- Sustainable Practices: As the world shifts toward more sustainable manufacturing methods, HIPIMS is being examined for its reduced material waste and potential for lower energy consumption compared to traditional sputtering techniques.
"Emerging trends in HIPIMS will not just stay on paper; they are destined to revolutionize how materials are processed across various industries."
"Emerging trends in HIPIMS will not just stay on paper; they are destined to revolutionize how materials are processed across various industries."
These trends create a promising context for the future, where HIPIMS might be integrated into more complex processes, potentially revolutionizing sectors like electronics, aerospace, and even renewable energy technologies.
Integration with Nanotechnology
The convergence of HIPIMS with nanotechnology presents a particularly compelling avenue for innovation. Nanotechnology focuses on manipulating materials at an atomic level, and the fine control offered by HIPIMS aligns perfectly with this philosophy.
- Quantum Dots and Thin Films: The ability to deposit ultra-thin films with precise thickness control through HIPIMS could advance the field of quantum dots, crucial for developing next-generation electronic devices.
- Nanocomposites: HIPIMS can be employed in creating nanocomposite materials, which have applications ranging from lightweight construction materials to high-performance fabrics. The technique's dimensional precision can facilitate the embedding of nanoparticles within a matrix, enhancing material properties.
- Biocompatibility and Drug Delivery Systems: In biomedical applications, HIPIMS can contribute to creating nanostructured coatings for medical implants that promote biocompatibility and can enhance drug release mechanisms in targeted therapies. This fusion of technologies could ultimately lead to better patient outcomes.
By understanding how HIPIMS resonates with nanotechnology, researchers can harness its unique capabilities to solve some of the most pressing challenges in material science. As we look forward, the collaboration of these fields stands to deliver unprecedented advancements, pushing the bounds of what is currently possible in materials engineering.
Challenges in HIPIMS Technology
The remarkable advancements in High-Intensity Pulsed Magnetron Sputtering (HIPIMS) have opened up new avenues in material science. Yet, the technology does not come without its set of challenges. Understanding these hurdles is crucial for researchers and industry professionals alike, as they shape the future viability and application of HIPIMS in various sectors.
Firstly, identifying the barriers in HIPIMS technology provides insights into the limitations and areas for improvement in the extraction process, material properties, and equipment design.
Scalability Issues
One major challenge facing HIPIMS is scalability. While the technology has shown impressive results in laboratory settings and some small-scale applications, it struggles to transition effectively to larger production scales. In many cases, the equipment used in HIPIMS systems may require significant modifications to handle increased capacities without forfeiting quality. This necessity marks a critical point for manufacturers and researchers as they try to strike a balance between throughput and the integrity of deposited films.
Factors contributing to scalability issues include:
- Equipment Limitations: Current tools are often bespoke, neglecting mass production needs and making many installations impractical on a wider scale.
- Process Control: Maintaining consistency in film formation becomes exponentially more complex as scale increases, leading to the risk of defects or subpar material properties.
- Unit Costs: As production scales grow, the initial costs of initial setups and modifications can escalate, turning away potential users who are weighing the financial decision.
Cost-Effectiveness
Another pain point with HIPIMS technology is the question of cost-effectiveness. The advantages of HIPIMS, such as producing high-density films with superior properties, are undeniable; however, these benefits come at a steep price. The initial investment in HIPIMS machinery and ongoing costs associated with operation can deter organizations, especially in small to medium enterprises, from adopting this advanced method.
Key considerations regarding cost-effectiveness include:
- Operating Costs: The high power levels required for HIPIMS can lead to increased energy consumption over traditional methods, necessitating a careful budget analysis.
- Maintenance and Repairs: Specialized equipment and components may also lead to higher maintenance costs and downtime when apparatuses malfunction, further burdening the operating budget.
- Market Competitiveness: As technology evolves, contenders emerging from conventional sputtering techniques may offer lower-cost solutions without sacrificing much in quality, thus challenging HIPIMSās market position.
"The answer to unlocking HIPIMS' potential lies in understanding and overcoming its current challenges."
"The answer to unlocking HIPIMS' potential lies in understanding and overcoming its current challenges."
By addressing the scalability and cost-effectiveness of HIPIMS, researchers can better position this innovative technology for future applications and improvements.
End
High-Intensity Pulsed Magnetron Sputtering (HIPIMS) stands at the intersection of possibility and reality in the material sciences realm. This conclusion synthesizes the vital points discussed throughout the article, reinforcing the instrumental role HIPIMS may play in various sectors. By capturing a unique deposition mechanism that allows for dense films with superior properties, HIPIMS opens new doors for engineering applications. Itās not just a flashy new tool; its potential extends to enhancing material performance across different fields.
The advantages of using HIPIMS, such as improved film quality, enhanced uniformity, and the ability to tailor material properties precisely, set it apart from traditional methods. Therefore, understanding these specific elements emphasizes why researchers and industries invest their time and resources into this technology.
Moreover, the insights drawn from this article bolster an understanding of cost-effectiveness and scalability concerns surrounding HIPIMS implementation. As industries continuously look for ways to innovate, integrating sophisticated techniques like HIPIMS into production cycles is essential.
"The future of material deposition lies in our ability to adapt and innovate with techniques like HIPIMS."
"The future of material deposition lies in our ability to adapt and innovate with techniques like HIPIMS."
Summary of Findings
This article has traversed the complex landscape of HIPIMS, articulating its foundational mechanisms, applications, and the innovations that push its boundaries. Key findings involve:
- Mechanisms: How pulsed power and sputtering dynamics create desirable materials, addressing their density and structural nuances.
- Applications: The burgeoning use of HIPIMS in fields from biomedical device manufacturing to microelectronics, each showcasing distinct advantages over conventional sputtering methods.
- Technological Innovations: Ongoing advancements in equipment and optimization techniques that promise continued evolution of HIPIMS technology.
Together, these findings weave a narrative conveying the significant advancements and applicability of HIPIMS in modern material science.
Implications for Future Research
While the current landscape is promising, multiple avenues await exploration within HIPIMS research. Future studies should address:
- Scalability Solutions: Investigating methods to scale HIPIMS for large-scale industrial applications without sacrificing quality.
- Cost-Effectiveness: Analyzing the economic implications of adopting HIPIMS compared to traditional sputtering methods. Financial sustainability plays a crucial role, especially in competitive markets.
- New Applications: Expanding exploration to areas such as nanotechnology and renewable energy materials, where HIPIMS could fulfill emerging needs.
As researchers dive deeper into these aspects, the necessity to balance innovation with practicality remains paramount. Advances in the understanding and implementation of HIPIMS hold the key to groundbreaking developments in materials science that are yet to be imagined.