Exploring Various Types of Titanium for Industry
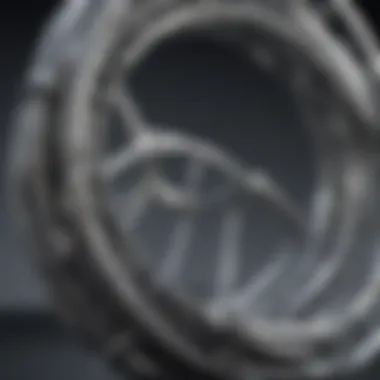
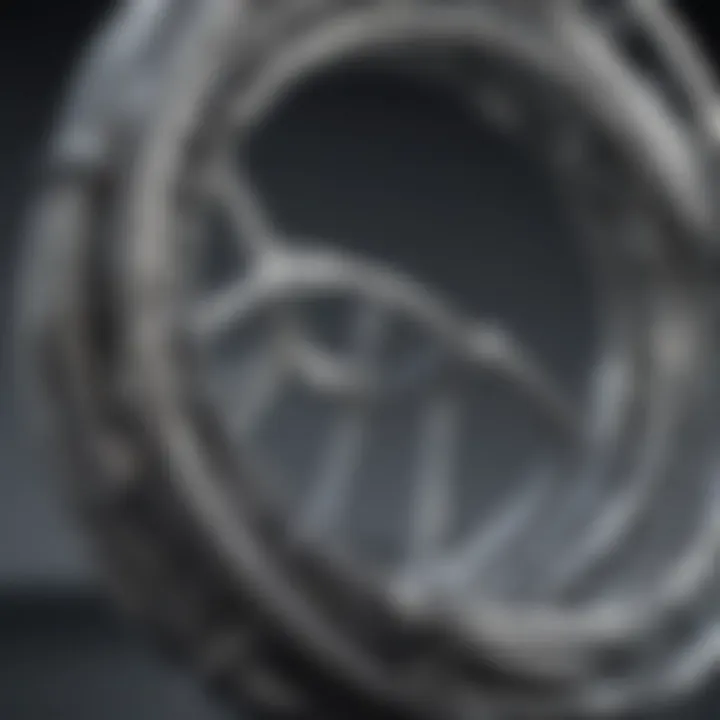
Article Overview
Purpose of the Article
The purpose of this article is to provide a detailed exploration of titanium types. It investigates their unique properties and various classifications, especially focusing on alpha and beta titanium, along with different titanium alloys. Each subsection will highlight the significance of these titanium categories within specific industries. By discussing applications relevant to sectors like aerospace, medical, and automotive, this article aims to offer valuable insights that can inform decision-making processes for engineers, researchers, and industrial professionals.
Relevance to Multiple Disciplines
Titanium’s characteristics make it a versatile material, applicable in numerous disciplines. In aerospace, its lightweight and high-strength properties contribute to fuel efficiency and performance. The medical field benefits from titanium's biocompatibility, making it ideal for implants and surgical instruments. Likewise, in the automotive industry, titanium alloys enhance performance and reduce weight, leading to improved efficiency. By bridging these industries, the insights provided in this article cater to a broad audience, encouraging interdisciplinary collaboration and exploration of titanium's potential.
Research Background
Historical Context
Understanding titanium’s evolution helps comprehend its current applications. Titanium was first discovered in 1791 by William Gregor but remained underutilized for nearly two centuries due to the difficulty of extraction and processing. The advent of the Kroll process in the 1940s revolutionized titanium production, enabling its use in various industries. Today, its exhaustive capability continues to expand through innovative engineering and technologies.
Key Concepts and Definitions
To appreciate the nuances of titanium types, some key concepts must be understood:
- Alpha Titanium: Known for its high strength and ductility, alpha titanium is stable at high temperatures and is less likely to become brittle.
- Beta Titanium: This form has a more complex structure and allows for greater formability, uhich is useful in creating various shaped components.
- Titanium Alloys: Combinations of titanium with other metals like aluminum and vanadium enhance specific properties such as corrosion resistance and fatigue strength.
These concepts lay the groundwork for deeper discussions in the following sections, providing clarity on how each type of titanium serves distinct roles across various applications.
Preface to Titanium
Titanium is a critical element in today's industrial landscape. Its unique properties, such as high strength, low density, and excellent resistance to corrosion, make it an essential material for various applications. The significance of titanium lies not only in its extensive utility but also in its remarkable characteristics that differentiate it from other metals. Understanding titanium is important for students, researchers, and professionals who are exploring advanced materials in engineering, aerospace, medical, and automotive fields.
When discussing titanium, various classifications and types come into play. Each type exhibits specific characteristics that enhance its applicability in different sectors. The introduction of titanium types sets the stage for deeper understanding of materials science and engineering, illuminating how these variations affect performance and usability in real-world applications. Therefore, a detailed examination is pertinent for anyone involved in material selection or engineering design.
Overview of Titanium
Titanium is a transition metal known for its prominent role in several industries. Elemental titanium has an atomic number of 22. It is also characterized by its impressive balance of strength and weight. One of its key advantages is its biocompatibility, which allows it to be used in medical implants and devices. Its prevalence in aerospace, primarily in aircraft manufacturing, is attributed to its favorable strength-to-weight ratio. This means that titanium provides significant structural integrity without adding excessive weight to the overall design.
The extraction of titanium from its ores, primarily ilmenite and rutile, involves complex processes. Even though it is abundant in the Earth's crust, obtaining pure titanium is challenging and requires advanced metallurgical techniques.
Historical Context
The understanding of titanium has evolved significantly. Discovered in 1791 by the British mineralogist William Gregor, titanium was first recognized as a new element. However, its commercial viability was not realized until the 20th century. During World War II, titanium became important for military applications. Its strength and corrosion resistance made it attractive for use in aircraft and missiles.
As technology progressed, the importance of titanium continued to rise. Its applications expanded into diverse sectors, including medical and automotive fields. This historical journey from discovery to industrial prominence illustrates the growing relevance of titanium in modern applications. By exploring the past, we can appreciate the advancements in titanium technology and its impact on various industries today.
Materials Science: Titanium Basics
Understanding the basics of titanium within materials science is crucial for grasping its significance in various applications. Titanium is renowned for its exceptional strength-to-weight ratio, which makes it an ideal material for industries such as aerospace and medical. Moreover, its resistance to corrosion enhances its usability in challenging environments, adding to its value in manufacturing and engineering. This section focuses on the atomic structure and physical properties of titanium, enriching the knowledge necessary for informed decisions in material selection and usage.
Atomic Structure
Titanium has an atomic number of 22, identifying it as a transition metal. The atomic structure is pivotal to the material's behavior. Titanium has a hexagonal close-packed (HCP) crystal structure at lower temperatures, transitioning to a body-centered cubic (BCC) structure when heated above 882°C. This structural change affects several key properties, including strength and ductility.
The arrangement of titanium's atoms influences its reactivity and how it interacts with other substances. Titanium reacts with oxygen, nitrogen, and carbon at high temperatures, forming layers of titanium oxide or carbide, which can complicate processing but also enhance durability. These unique traits emphasize the need for a nuanced understanding of titanium's atomic structure in various applications.
Physical Properties
Titanium exhibits several notable physical properties that significantly contribute to its appeal as a material. Some of these include:
- Density: Titanium has a density of approximately 4.5 g/cm³. This is considerably lower than steel, making titanium an ideal choice in applications where weight is a concern.
- Strength: The tensile strength of commercially pure titanium can reach up to 1000 MPa. In alloys, this can be even higher, making it suitable for high-stress applications.
- Corrosion Resistance: Titanium resists corrosion in seawater and other corrosive environments due to the formation of a protective oxide layer.
- Biocompatibility: Its biocompatibility is well established. This makes it particularly appealing for medical implants and devices.
In addition to these attributes, titanium maintains good thermal stability and has a low thermal expansion coefficient. These properties allow it to retain its integrity under varying temperature conditions, making it a reliable material choice across diverse fields.
Titanium's unique combination of lightweight, strength, and corrosion resistance makes it indispensable in modern engineering and manufacturing settings.
Titanium's unique combination of lightweight, strength, and corrosion resistance makes it indispensable in modern engineering and manufacturing settings.
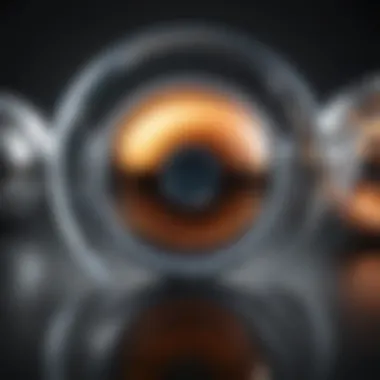
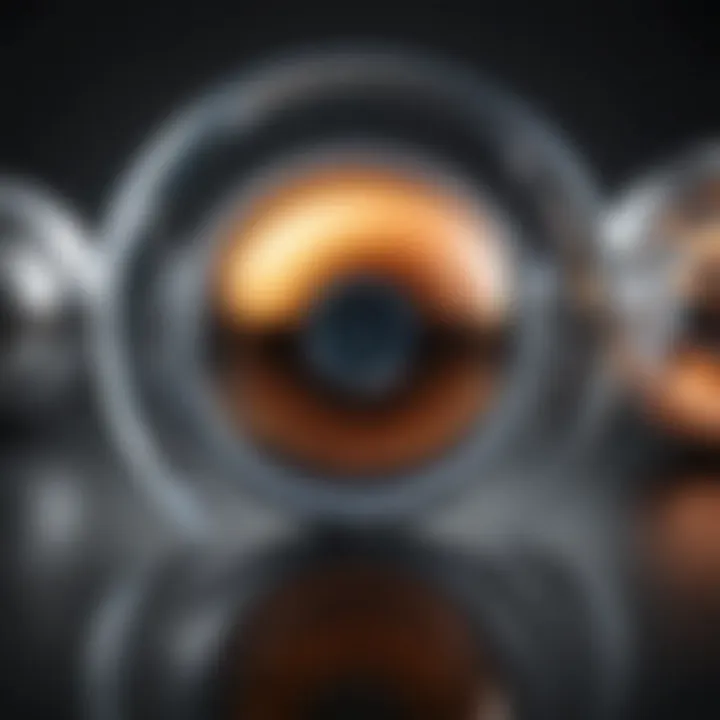
In summary, the atomic structure and physical properties of titanium are foundational to its functionality and application. Understanding these aspects plays a vital role in the effective use of titanium across multiple industries, ensuring that engineers and researchers can select the right form of titanium for their specific needs.
Classification of Titanium Types
Understanding the classification of titanium types is crucial for several reasons. First, it provides clarity on the diverse applications of titanium in various industries. Each type possesses unique characteristics that influence its performance in different environments. By categorizing titanium into alpha, beta, and alpha-beta groups, professionals can more easily select the right type for their specific needs. This organized approach also helps streamline research and development processes. The following subsections explore each classification in detail, emphasizing their properties, applications, and potential benefits.
Alpha Titanium
Characteristics
Alpha titanium is known for its unique crystallographic structure, which is predominantly hexagonal close-packed. This structure contributes to its excellent ductility and weldability. The most notable characteristic of alpha titanium is its high-temperature stability. This property makes it suitable for applications where heat resistance is essential. Unlike beta titanium, which can undergo transformations in stressful environments, alpha titanium maintains its structure and properties under high temperatures, making it a preferred choice in many industries.
Applications
Alpha titanium finds significant use in industries that require lightweight and strong materials. For instance, in the aerospace sector, components made from alpha titanium are used in airframe structures and engine parts due to their ability to withstand high stresses and temperatures. Additionally, the medical field uses alpha titanium in dental implants and prosthetics. Its biocompatibility and resistance to corrosion enhance its attractiveness in these applications. However, its availability in certain forms can sometimes limit its usage.
Advantages
The advantages of alpha titanium include its lightweight nature and excellent mechanical properties. These features contribute to fuel efficiency in aerospace applications and improved patient outcomes in medical uses. Moreover, it is relatively easy to machine compared to other titanium types. However, one downside to alpha titanium is its lower strength compared to beta types, which may limit its application when high strength is essential.
Beta Titanium
Characteristics
Beta titanium stands out due to its body-centered cubic structure. This structure allows for greater strength and toughness compared to alpha titanium. The key characteristic of beta titanium is its ability to be heat-treated. Such treatments can enhance its physical properties considerably. This adaptability makes beta titanium a popular choice in demanding environments, where mechanical performance is paramount.
Applications
Beta titanium has a diverse range of applications. In the aerospace industry, it is often used in high-performance components where strength is crucial. Similarly, the automotive sector benefits from beta titanium in making lightweight yet robust parts. Moreover, this type of titanium has found a niche in the medical field for surgical instruments and implants, especially where increased strength is needed. However, its processing and fabrication can be more complex than for alpha titanium.
Advantages
One significant advantage of beta titanium is its superior strength and toughness, making it ideal for applications requiring durability and resilience. The heat-treatability of this type further opens up possibilities for customization of its mechanical properties. Nevertheless, its processing can entail higher costs and require specific machinery, which could be seen as a drawback in certain applications.
Alpha-Beta Titanium
Characteristics
Alpha-beta titanium combines aspects of both alpha and beta phases. This unique characteristic of dual-phase microstructure leads to an excellent balance between strength and ductility. It is particularly beneficial in situations where both traits are required. The versatility of alpha-beta titanium contributes significantly to its extensive use across several sectors.
Applications
The applications of alpha-beta titanium are widespread. In aerospace, it is used in turbine engines and other critical components where weight reduction without sacrificing strength is necessary. Similarly, in the medical realm, it's employed for various surgical implants and tools. The ability to perform well in challenging conditions adds to its allure. The dual nature means that it can adapt to different configurations, although specific formulations may be optimized for particular applications.
Advantages
Alpha-beta titanium offers a favorable blend of high strength and good ductility. This makes it suitable for applications where failure could have serious consequences. Its adaptability in different environments allows for diverse uses across industries. However, one potential disadvantage is that its processing may require more precise control compared to other titanium types, potentially leading to inconsistency in material properties if not managed properly.
Titanium Alloys Overview
Titanium alloys are crucial in delivering the diverse characteristics required in industrial and scientific applications. Their unique combination of strength, light weight, and resistance to corrosion makes them invaluable in various fields. This section outlines the definition, importance, and commonly used titanium alloys, emphasizing how they enhance performance in specific applications.
Definition and Importance
Titanium alloys are metal mixtures that contain titanium and other elements. They offer enhanced properties compared to pure titanium, including improved mechanical performance and increased resistance to environmental factors. The significance of titanium alloys cannot be overstated; they play vital roles in sectors such as aerospace, medical, and automotive industries. Their ability to withstand stress while remaining lightweight offers engineers and manufacturers the perfect solution for high-performance applications.
Common Titanium Alloys
Ti-6Al-4V
Ti-6Al-4V is one of the most popular titanium alloys, known for its excellent strength-to-weight ratio. It belongs to the alpha-beta alloy category, combining the properties of both phases. This alloy is commonly used in aerospace components due to its high tensile strength and fatigue resistance. The key characteristic of Ti-6Al-4V is its ability to maintain strength at elevated temperatures, making it suitable for applications like aircraft engines and critical structural components. Its unique feature is that it can be welded, providing versatility in manufacturing processes. However, Ti-6Al-4V has a higher cost compared to other titanium alloys, which can be a disadvantage in large-scale applications.
Ti-5Al-2.5Sn
Ti-5Al-2.5Sn is another significant titanium alloy characterized by its excellent workability and low density. It finds its applications primarily in the aerospace sector, where lightweight materials are essential. The key characteristic of Ti-5Al-2.5Sn is its good oxidation resistance and weldability, making it an attractive choice for various structural components. Its unique feature lies in its moderate strength combined with high corrosion resistance, which is beneficial in environments exposed to harsh conditions. On the downside, this alloy may not be suitable for applications requiring exceptionally high strength levels.
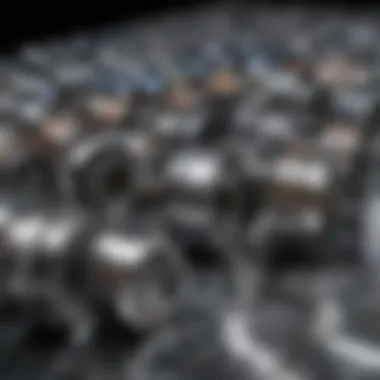
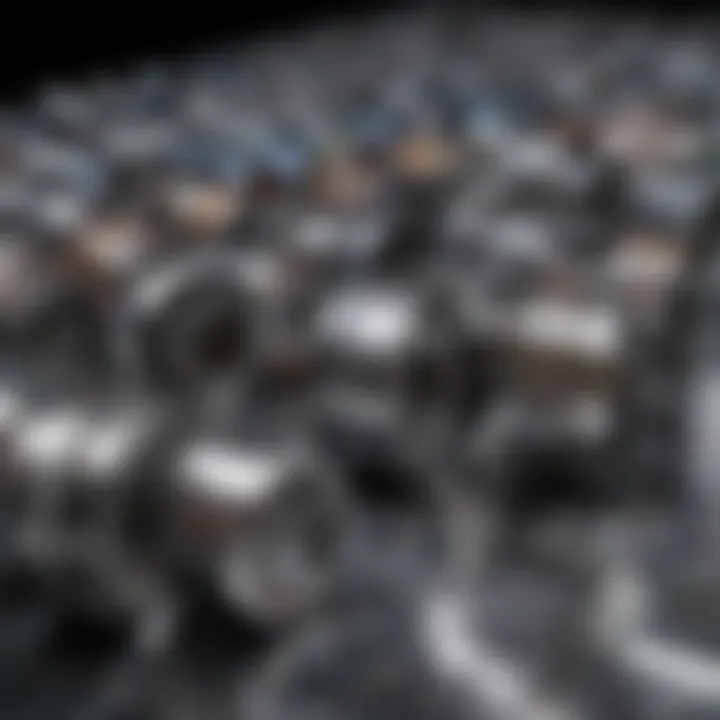
Ti-6Al-7Nb
Ti-6Al-7Nb is known for its application in the medical field, particularly for implants and prosthetics. This alloy offers a balance of strength and biocompatibility, making it ideal for use in the human body. The key characteristic of Ti-6Al-7Nb is its reduced modulus of elasticity compared to other titanium alloys, which helps in mimicking bone properties. This unique feature lead to less stress shielding when used in orthopedic applications. Its limitations include potential challenges during machining due to its tendency to work harden, which can affect production efficiency.
The versatility of titanium alloys significantly influences the progress of engineering and technology in several important sectors.
The versatility of titanium alloys significantly influences the progress of engineering and technology in several important sectors.
Understanding the specific characteristics and applications of titanium alloys is essential for professionals engaged in design and material selection. These alloys unlock a range of possibilities, enabling innovations that drive industry standards.
Applications of Titanium Types
Titanium's unique combination of strength, low density, and resistance to corrosion makes it a material of choice in various industries. Understanding the applications of different types of titanium is essential for professionals and enthusiasts alike. This section covers key industries such as aerospace, medical, and automotive, demonstrating how titanium’s properties align with their specific demands. This knowledge benefits engineers, designers, and researchers by providing clear insights into material selection for optimum performance and reliability.
Aerospace Applications
Titanium plays a crucial role in aerospace due to its high strength-to-weight ratio. Aircraft components such as landing gear, engine parts, and frames frequently utilize titanium alloys like Ti-6Al-4V. This alloy provides strength without the excess weight, enhancing fuel efficiency and performance. The ability to withstand extreme temperatures and manage fatigue makes titanium indispensable in this sector.
- Key Benefits:
- Reduced weight improves fuel efficiency.
- High resistance to corrosion prolongs component life.
- Enhances safety with strong, lightweight structures.
Applications in aerospace demand stringent specifications and standards. Special conditions can arise at high altitudes, and titanium’s mechanical properties help maintain structural integrity. For instance, spacecraft components have to endure harsh environments; titanium’s durability is well-suited for this purpose.
Medical Applications
In the medical field, titanium is highly valued for its biocompatibility. Implants, surgical instruments, and dental appliances often utilize titanium due to its ability to integrate with human tissue. The material promotes healing and minimizes the risk of rejection by the body.
Specific titanium alloys, such as Ti-6Al-4V, are commonly employed in orthopedic and dental implants. Its advantageous properties include:
- Corrosion Resistance: Ensures longevity in bodily fluids.
- Non-Toxicity: Reduces risks of allergic reactions.
- Strength and Light Weight: Provides structural reliability without adding extra mass.
The use of titanium in medical devices illustrates the critical balance between material performance and human health. Hospitals and clinics increasingly embrace innovative titanium solutions, pointing towards an expanding market for these applications.
Automotive Applications
The automotive industry has also recognized the advantages of titanium. While traditionally heavy metals dominated this field, the demand for lighter, stronger materials is shifting the focus to titanium. Components such as valves, connecting rods, and exhaust systems benefit significantly from titanium’s properties.
By incorporating titanium, manufacturers can achieve:
- Improved Fuel Efficiency: Lighter components contribute to lower energy consumption.
- Enhanced Performance: Increased strength allows for higher performance thresholds.
- Durability: Titanium’s resistance to heat ensures long-lasting performance under stress.
Despite being more expensive than conventional metals, the long-term benefits of titanium often outweigh initial costs. Industry leaders are investing in titanium components not only for performance but also for environmental sustainability.
"The increasing adoption of titanium in automotive components highlights a crucial trend of favoring materials with lower environmental impact while enhancing vehicle performance."
"The increasing adoption of titanium in automotive components highlights a crucial trend of favoring materials with lower environmental impact while enhancing vehicle performance."
Standards and Specifications for Titanium
Standards and specifications for titanium are crucial in ensuring that it meets the rigorous demands of various industries. By adhering to these standards, manufacturers can guarantee the quality, safety, and performance of titanium products. This guidance minimizes the potential for failures, enhances reliability, and maximizes the material's functional advantages. The two primary organizations that define specifications for titanium are ASTM International and the International Organization for Standardization (ISO). Each set of standards plays a unique role in shaping the way titanium is processed and utilized in different applications.
ASTM Standards
ASTM International develops voluntary consensus technical standards for materials, products, systems, and services. The ASTM standards related to titanium outline the properties and testing methods for various titanium alloys and grades. These standards ensure that titanium fulfills requirements concerning mechanical properties, chemical composition, and any other critical factors.
For instance, ASTM B265 covers the specification for titanium and titanium alloy plates, sheets, and strips for aerospace and other applications. The testing methods prescribed by ASTM help assess the tensile strength, ductility, and fatigue resistance of titanium materials. Compliance with these standards is not only helpful for manufacturers but also assures end-users of the titanium's performance in demanding environments.
ISO Standards
The ISO standards complement ASTM specifications by providing an international framework for the quality and safety of titanium products. ISO standards related to titanium ensure consistency across countries and industries. This is key, especially for multinational companies that require uniformity in their supply chain.
For example, ISO 5832-2 specifies the requirements for titanium, which is particularly used in medical implants. This standard ensures that titanium used for such sensitive applications is biocompatible and meets all safety criteria. The ISO framework also covers manufacturing practices and testing protocols to ensure high-quality outputs.
Maintaining adherence to recognized standards facilitates international trade and cooperation while improving the reliability of titanium products.
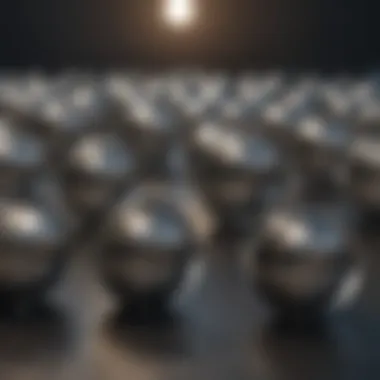
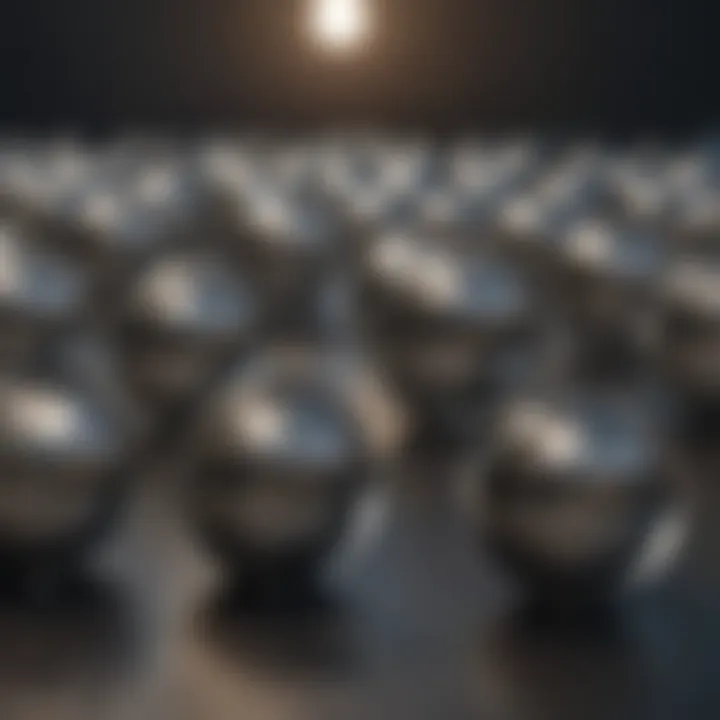
Maintaining adherence to recognized standards facilitates international trade and cooperation while improving the reliability of titanium products.
In summary, ASTM and ISO set invaluable benchmarks for titanium production and use. As industries grow increasingly globalized, these standards not only simplify compliance but also serve as vital indicators of quality assurance. Ensuring adherence to these highly regarded specifications can lead to improved processes, lower costs, and enhanced performance in the increasingly competitive titanium market.
Challenges in Titanium Utilization
Titanium is a unique metal with many advantageous properties, but its utilization also involves several challenges. Understanding these issues is crucial for anyone engaging with titanium in various fields. The challenges impact both the cost-effectiveness and practicality of using titanium in industrial applications. Addressing these challenges effectively can lead to improved methods and practices in the industry.
Cost Factors
Cost is a primary concern when working with titanium. The production and processing of titanium are significantly more expensive than those of metals like aluminum or steel. This is due to the complex extraction process and the need for specialized equipment for machining and fabrication.
- Extraction Costs: Extracting titanium from its ores often involves the Kroll process. This process requires high temperatures and specialized environments, resulting in high energy consumption and, thus, increased costs.
- Market Prices: The market price for commercially pure titanium and titanium alloys can fluctuate. Demand from sectors like aerospace or medical applications can cause prices to rise quickly. This unpredictability can deter investment in titanium projects.
- Supply Chain Issues: The supply chain for titanium, including raw material availability and processing facilities, can be strained. Such issues can lead to delays and inflated costs for manufacturers.
These cost factors suggest that while titanium offers many benefits, its economic feasibility must be carefully analyzed before extensive use in projects.
Processing Difficulties
Processing titanium presents unique challenges, stemming from its physical properties and reactivity. These processing difficulties can limit the applications of titanium, especially in projects requiring high precision or large-scale production.
- Machining Challenges: Titanium has a low thermal conductivity, which can lead to overheating during machining processes. This overheating can cause tool wear and reduce the quality of the finished components. Special cutting tools or techniques may be necessary, which adds to processing costs.
- Welding and Joining Issues: Titanium can be difficult to weld due to its tendency to react with oxygen at elevated temperatures. This requires a controlled environment, typically with inert gas shielding, complicating the welding process.
- Forming Limitations: Forming titanium requires substantial force and may need additional processing steps, which can also increase costs and complexity.
Proper understanding and techniques in dealing with these processing difficulties can make titanium a more viable option for various applications.
Proper understanding and techniques in dealing with these processing difficulties can make titanium a more viable option for various applications.
In summary, while titanium holds immense potential in various industrial fields, it is essential to recognize and mitigate the challenges inherent in its utilization. By tackling cost factors and processing difficulties head-on, industries can better leverage the unique properties of titanium.
Future Trends in Titanium Research
The evolving landscape of titanium research plays a pivotal role in various industries. The exploration of new methodologies, deeper understanding of titanium's properties, and innovative applications significantly enhance its viability in demanding environments. Organizations continually seek improvements in titanium material properties while aiming for sustainability and efficiency.
As industries grapple with globalization and increasing competition, future trends reflect the critical need for titanium to adapt and evolve. By focusing on innovative alloy designs and sustainable production practices, stakeholders can achieve advanced solutions to meet modern challenges. This section discusses the several key future trends in titanium research, emphasizing their importance and implications for both the industry and scientific community.
Innovations in Alloy Design
Innovations in titanium alloy design are paramount to enhancing performance in specialized applications. Researchers are exploring various methods to optimize alloy compositions, leading to the development of new titanium alloys that exhibit improved properties. These advancements may involve modifying existing alloys or creating entirely new combinations of elements to achieve desired characteristics such as increased strength, better corrosion resistance, or reduced weight.
Some notable approaches include:
- Nano-alloying: Incorporating nanoparticles can enhance mechanical properties at a minimal weight increase.
- Additive manufacturing: This technology allows for complex geometries and can significantly reduce waste during production.
- Combinatorial methods: Utilizing advanced computational techniques to predict optimal compositions before extensive physical testing.
These innovations can broaden the application range of titanium, particularly in high-performance environments, such as aerospace and medical fields.
Sustainable Practices in Titanium Production
Sustainability has emerged as a crucial consideration in titanium production. Industries face increasing pressure to adopt environmentally friendly practices. Developing sustainable methods can reduce waste and energy consumption, addressing both environmental concerns and cost factors.
Key sustainable practices include:
- Recycling titanium scrap: Efficient recycling processes can reclaim valuable materials while decreasing the need for new sources.
- Alternative processing methods: Exploring new production techniques, such as hydrogen reduction, may lead to more sustainable options than traditional methods.
- Lifecycle assessments: Conducting comprehensive assessments can help pinpoint opportunities for improvement throughout the production pipeline.
An emphasis on sustainability not only enhances public perception and industry responsibility but also proves advantageous financially.
"Sustainable titanium production is no longer a choice, but a requirement for future viability in the market."
"Sustainable titanium production is no longer a choice, but a requirement for future viability in the market."
The End
The conclusion serves as a critical element in this article as it encapsulates the entire discourse on titanium types. It highlights the various classifications, their unique properties, and the applications relevant across multiple industries. Understanding the nuances of each titanium type is essential for professionals involved in material selection and engineering processes. The implications for industries such as aerospace, medical, and automotive rely significantly on recognizing these differences for optimal outcomes.
Summary of Key Points
- Titanium Varieties: The article delves into alpha, beta, and alpha-beta titanium types, emphasizing their specific characteristics.
- Applications Across Industries: Each titanium type has applications tailored to its properties. For instance, titanium alloys like Ti-6Al-4V are favored in aerospace due to their high strength-to-weight ratio.
- Manufacturing Standards: The presence of ASTM and ISO standards ensures consistency and quality in titanium production.
- Challenges and Considerations: Factors such as cost and processing difficulties often influence the decision-making process in titanium utilization. Knowing these can guide better planning and budgeting.
Implications for Future Research
Future research into titanium types could focus on several pivotal areas:
- Alloy Innovation: Developing new alloy compositions can enhance performance in extreme environments, particularly for aerospace applications.
- Sustainability: Exploring sustainable practices in titanium production is crucial. Strategies like recycling titanium scrap can lessen the environmental impact.
- Advanced Processing Techniques: Investigating new methods in titanium processing could address the current challenges faced by manufacturers, boosting efficiency and product quality.