Comprehensive Guide to Wafer Processing Techniques
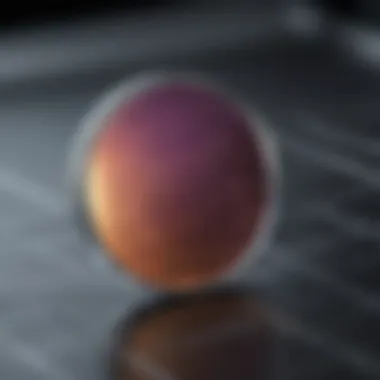
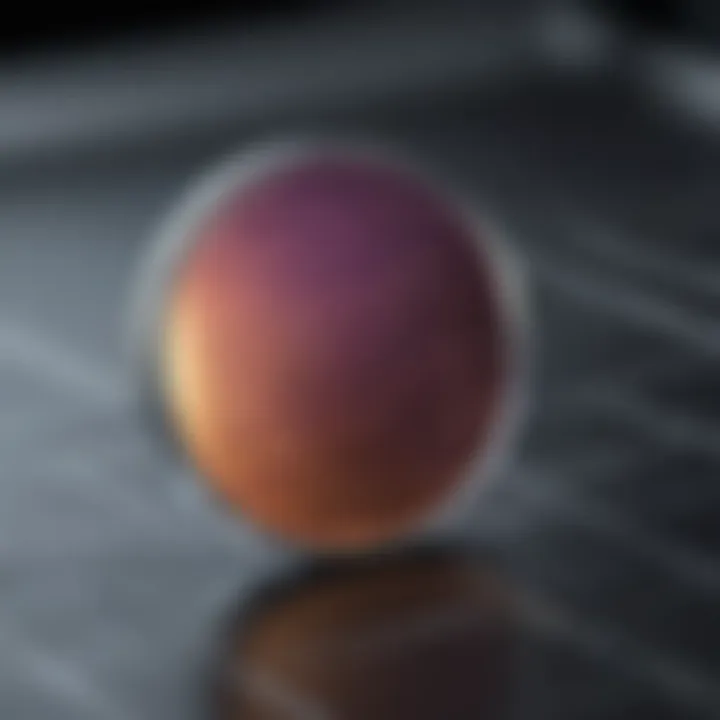
Intro
Wafer processing is an essential cornerstone of semiconductor fabrication, standing at the crossroads of technology and manufacturing. As we leap into a world increasingly driven by electronics, understanding wafer processing becomes vital. It’s the thermally treated, meticulously crafted foundation upon which modern computations hinge.
Grasping the various, sometimes complex, methodologies involved in this process enables professionals, students, and researchers alike to navigate the landscape of semiconductor technology with greater confidence.
Article Overview
Purpose of the Article
This article seeks to unravel the intricacies of wafer processing, illuminating each stage—from wafer preparation to doping. The aim is not merely to list the steps but to examine how these stages fit together like pieces of a jigsaw puzzle, shaping the final product that powers the devices we use daily.
By diving into the core methodologies, advancements, and trends, readers can appreciate the significance of wafer processing in the broader field of microelectronics. Whether you find yourself as a novice eager to learn or an experienced professional looking for a refresher, this piece serves as your compass through the intricate world of semiconductor fabrication.
Relevance to Multiple Disciplines
Wafer processing speaks to an expansive array of disciplines:
- Electrical Engineering: It acts as the backbone for device functionality.
- Material Science: Understanding the materials involved is critical for innovation.
- Physics: The principles of light and electricity govern many processes.
- Manufacturing Engineering: Enhancements in efficiency and automation are also tied to wafer processing.
This interconnectedness illustrates how advancements in wafer processing can resonate across fields, propelling new innovations and technologies forward.
Research Background
Historical Context
The roots of wafer processing can be traced back to the early days of semiconductor discovery in the mid-20th century. Back then, transistors were viewed as a mere novelty, but as demand burgeoned, so did the techniques required to fabricate them efficiently. Over decades, methods have evolved, embracing new materials and technologies—including silicon wafers, which have become the industry standard.
Key Concepts and Definitions
To navigate this intricate manufacturing process, several foundational concepts must be in the grasp of the reader:
- Wafer Preparation: This involves the cleansing and polishing of wafers to ensure their purity and surface integrity.
- Photolithography: A technique where light is used to transfer patterns onto a substrate, ultimately defining device architecture.
- Etching: This defines the selective removal of material, integral for creating the desired geometries.
- Doping: Introducing impurities into a semiconductor layer to modify its electrical properties.
These concepts serve as pillars supporting the entire field of semiconductor processing, influencing everything from performance to yield in modern electronic devices.
"Understanding the nuances of wafer processing is essential for innovation in semiconductor technology."
"Understanding the nuances of wafer processing is essential for innovation in semiconductor technology."
The exploration ahead will delve deeper into each of these stages, revealing not only what they are but also why they matter in the grand scheme of technology.
Foreword to Wafer Processing
Wafer processing stands as a cornerstone in the realm of semiconductor manufacturing. It embodies a series of intricate procedures that transform raw semiconductor materials into functional electronic devices. As we navigate through this article, it becomes clear that understanding wafer processing isn't merely a theoretical exercise; it's fundamentally crucial in grasping how modern technology operates.
Each stage of the processing journey contributes to the final product's efficiency, performance, and reliability. This exploration will expose the layers of complexity involved, making it evident that proper wafer processing is pivotal for creating high-quality microelectronic devices.
Understanding Semiconductor Materials
The very foundation of wafer processing is rooted in semiconductor materials—primarily silicon, gallium arsenide, and indium phosphide among others. Each of these materials has unique properties that make them suitable for different types of electronic applications. For instance, silicon is favored for its abundance and cost-effectiveness, while gallium arsenide excels in high-frequency applications due to its superior electron mobility.
Going beyond mere composition, one must dive into variables such as doping types, crystal structures, and lattice parameters that can heavily influence electrical characteristics. Various dopants introduce controlled imperfections into these materials, allowing for modulation of their conductivity.
Furthermore, the crystal growth methods, such as Czochralski or Bridgman techniques, can significantly affect the final quality and performance of wafers.
Importance of Wafer Processing in Microelectronics
Wafer processing acts as a linchpin in the microelectronics sector, determining not just the functionality of devices but also their scalability and manufacturability.
Key Relevance Aspects:
- Precision and Standardization: In a field where a single micron can make or break a circuit, wafer processing ensures that dimensions are meticulously controlled.
- Yield Maximization: Efficient processing techniques translate to higher yields by minimizing defects and maximizing usable chips per wafer.
- Cost Efficiency: Streamlined processes help in reducing production costs. Minimizing wastage, equipment downtime, and other inefficiencies can lead to a favorable impact on the bottom line.
Wafer Fabrication Techniques
Wafer fabrication is the heart of semiconductor processing, laying the groundwork for device manufacturing. The techniques involved are crucial since they impact the overall functionality and quality of semiconductor devices. As technology progresses and demands evolve, understanding these techniques becomes increasingly vital.
In essence, wafer fabrication techniques translate raw materials into high-performance semiconductors—a transformation that’s rather complex. These methods not only enhance device efficiency but also address different requirements across various applications, ranging from everyday consumer electronics to highly specialized industrial tools. Moreover, the culmination of these techniques hinges on detail-oriented processes, making them indispensable in the microelectronics landscape.
Crystal Growth Methods
Bulk Growth Techniques
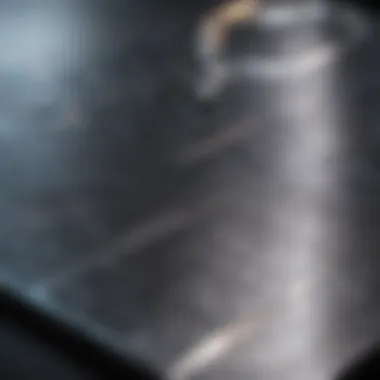
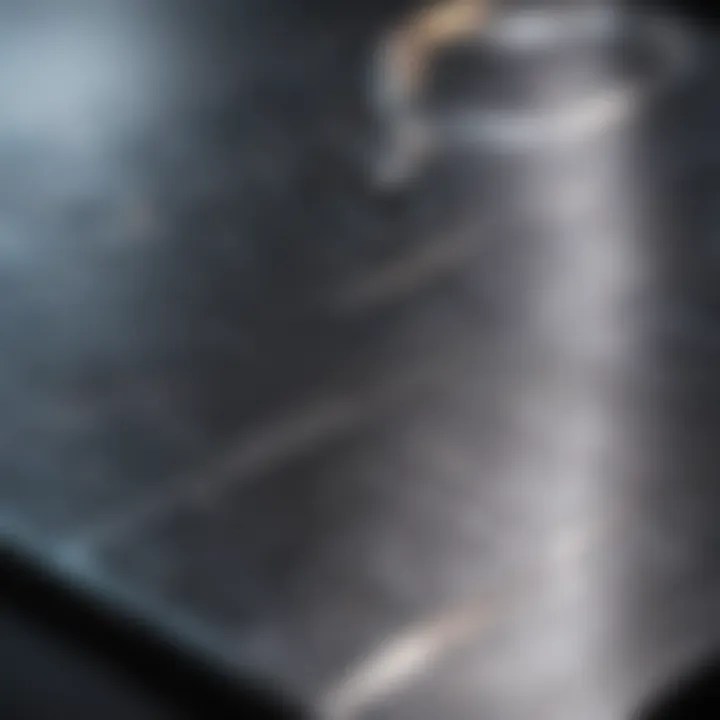
When it comes to creating semiconductors, bulk growth techniques stand out as a fundamental approach. This process primarily focuses on synthesizing single crystals from a molten state, often seen in the production of silicon wafers. The key characteristic of bulk growth lies in its ability to produce large quantities of material with uniform properties, making it a worthy choice in this article.
One of the unique features of bulk growth is its methodical nature—it relies on established methods like the Czochralski (CZ) technique or the float-zone (FZ) method. These techniques have their benefits, notably the capability to create high-purity crystals, which is essential for effective semiconductor performance. However, challenges persist, particularly concerning the scalability and cost-efficiency of the production methods.
In summary, bulk growth techniques bring considerable advantages, yet there are challenges related to production efficiency and overall yield that should not be overlooked.
Epitaxial Growth Methods
Epitaxial growth methods serve as a sophisticated layer on top of the foundational crystal growth processes. These techniques are integral for creating high-quality crystalline layers on substrates, allowing for finer control over material properties. The key characteristic here is the ability to fabricate layers that closely mimic the underlying crystal structure. This quality makes epitaxial growth a popular choice in the semiconductor field.
For instance, molecular beam epitaxy (MBE) and metal-organic chemical vapor deposition (MOCVD) are widely used in this sphere. A significant advantage of epitaxial growth methods is their precision in delivering doped layers—this is crucial for creating components like transistors and diodes which require specific electrical characteristics.
Nevertheless, the process calls for stringent conditions and can be more expensive, making cost management a critical consideration during device design and manufacturing.
Wafer Polishing and Cleaning
Chemical Mechanical Polishing
Chemical mechanical polishing (CMP) stands as a vital technique to achieve the desired surface topology in wafer fabrication. This dual-process combines mechanical abrasion with chemical reactions to smooth the wafer surface, making it suitable for the complex layering in semiconductor applications. A standout feature of CMP is its versatility—able to handle various materials and achieve uniform surface finishes.
The benefits of CMP are glaring: it not only enhances surface flatness but also minimizes defects that can impede device performance. Since microelectronics devices demand extreme precision, CMP has become almost a necessity. However, this process is not without its downsides; managing slurry contamination and maintaining operational consistency can turn into persistent challenges for professionals.
Surface Contamination Removal
Surface contamination removal is another crucial aspect of wafer preparation, ensuring that no residues compromise the integrity of the devices. This process emphasizes the elimination of any particulates or chemical remnants left from previous fabrication stages. A key characteristic of this technique is the deployment of various cleaning agents and methodologies, tailored to specific types of contaminants.
Utilizing methods like acid-based cleans or plasma-based techniques provides significant advantages in producing defect-free surfaces. However, the trade-off often lies in the potential for damaging the wafer if not executed correctly. As such, great care must be taken to balance effectiveness with the preservation of material integrity.
"Wafer fabrication is not just about methods; it's a blend of art and science, requiring a fine touch and keen understanding of materials and processes."
"Wafer fabrication is not just about methods; it's a blend of art and science, requiring a fine touch and keen understanding of materials and processes."
Key Processes in Wafer Processing
Wafer processing involves a series of critical steps that are fundamental to the fabrication of semiconductor devices. Each of these processes plays a vital role in determining the performance and efficiency of the final products. This section highlights the importance of these processes, including photolithography, etching techniques, and doping methods. Understanding these key elements provides insight into the intricate nature of semiconductor manufacturing and its significant impact on the microelectronics industry.
Photolithography
Process Overview
Photolithography serves as a cornerstone in wafer processing. It involves projecting light through a mask onto a photosensitive material, known as photoresist, which sits atop the wafer. The light alters the chemical properties of the photoresist, enabling the selective removal of areas during subsequent developing processes. One of its main benefits is precision; photolithography can pattern features down to sub-micrometer scales, which is quite essential in today’s highly integrated circuit designs.
The unique characteristic of photolithography is its capability to produce highly defined patterns over large areas, making it a leading choice in semiconductor fabrication. However, it does face limitations, such as dependency on the wavelength of light used and the need for expensive equipment and materials. This process remains a beneficial approach despite these drawbacks.
Resist Materials and Applications
Resist materials are crucial in the photolithography process, influencing the quality of the patterned features. Commonly used resist materials include positive and negative resists, with positive resists being noted for their ability to enhance resolution. The selection of the right resist material impacts the clarity and fidelity of the features being created.
These materials determine not only how well the patterns can be reproduced but also their compatibility with various Etching processes. While positive resists allow for greater resolution, they might also require post-exposure baking, which adds complexity and potential pitfalls to the workflow. Hence, it's a balancing act, where the choice must align with the desired application and the overall manufacturing strategy.
Etching Techniques
Dry Etching vs Wet Etching
Etching is a key process that follows photolithography. It involves selectively removing material from the wafer to create the desired features. The two primary types are dry etching and wet etching. Dry etching uses plasma or reactive gases, which allows for more control and accuracy, crucial for creating intricate designs. In contrast, wet etching uses liquid chemicals, generally resulting in faster removal rates but with less precision.
The distinctive advantage of dry etching lies in its ability to achieve anisotropic etching, preserving vertical sidewalls that conform closely to the patterns laid down by the photolithography stage. On the flip side, wet etching can cause undercutting, leading to less defined edges, which could compromise device performance.
Selective Etching Methods
Selective etching methods play a pivotal role in ensuring that only certain materials are removed, depending on their composition or etching rate. This specificity is important in multilayer structures typically found in semiconductors. An essential aspect is how these selective techniques can target specific layers within the semiconductor stack, resulting in improved yield and performance.
Through methods like chemical etching and plasma etching, manufacturers are able to sculpt the substrate with precision. However, while selective etching minimizes waste and enhances efficiency, it often requires more complex setup, which can increase costs and time in the fabrication process.
Doping Processes
Ion Implantation
Doping is essential for modifying the electrical properties of the semiconductor. Ion implantation, a widely used technique, involves bombarding the silicon wafer with ions of dopants. This process allows for precise control over the dopant's dose and depth, leading to better performance characteristics in the final device. It’s seen as a reliable and popular method in wafer processing due to this level of precision.
The unique benefit of ion implantation is the ability to tailor semiconductor properties resulting in improved device functionality. However, it can introduce damage to the crystal lattice of the silicon, which typically requires subsequent annealing steps for repairing the crystalline structure.
Diffusion Techniques
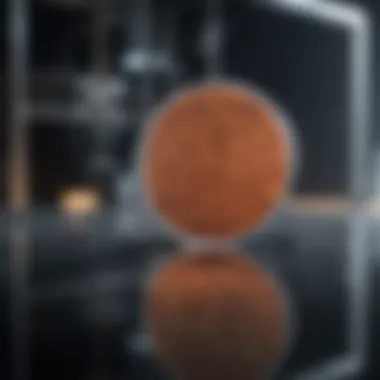
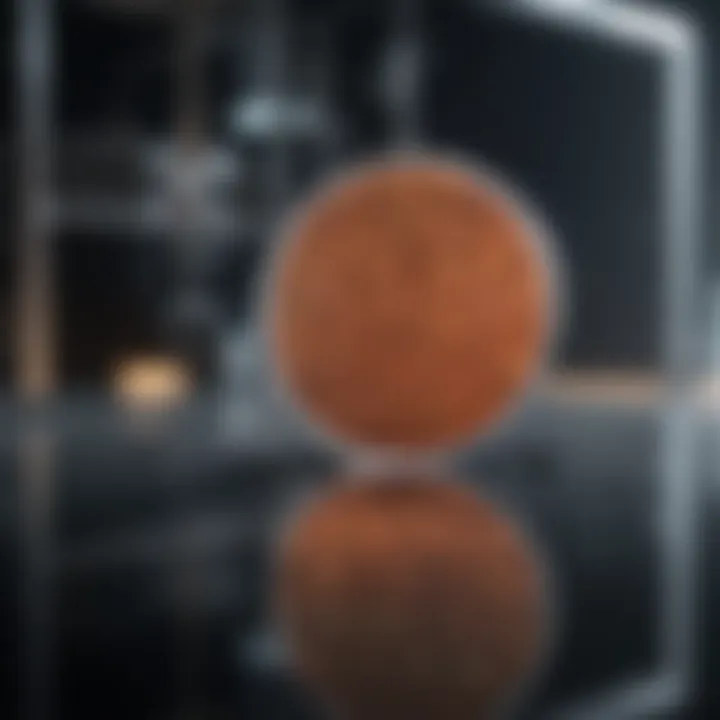
Diffusion techniques stand in contrast to ion implantation. This older method relies on heat and concentration gradients to allow dopants to flow into the silicon wafer. It's often preferred for its relatively simpler process compared to ion implantation. This method ensures a more uniform distribution of dopants, but it can be less precise regarding control over the depth of the doping.
The key characteristic of diffusion processes is the ease of application across large batches, making it cost-effective for higher volume manufacturing. Yet, the trade-off is a broader doping profile, which might not be suitable for advanced applications requiring tight specifications in component performance.
In summary, each of these key processes in wafer processing contributes significantly to the performance and efficiency of semiconductor devices. By understanding these intricate procedures, professionals in semiconductor research and teaching can appreciate the technological marvels produced in modern microelectronics.
Challenges in Wafer Processing
Wafer processing stands as a cornerstone in semiconductor manufacturing, yet it's not without its hurdles. These challenges, if unaddressed, can derail production timelines, inflate costs, and render products less competitive. By analyzing these hurdles systematically, we uncover insights vital for enhancing efficiency and maintaining quality in the industry. This section zeroes in on two primary categories of challenges: defects and surface quality issues, as well as scalability in production.
Defects and Surface Quality Issues
Types of Defects
Defects in wafers come in various forms, each weaving its story of potential failure or Quality Control problems. Common types include crystalline defects, which originate during crystal growth, and surface defects, appearing from inadequate polishing or exposure to contaminants. A notable characteristic of these defects is their ability to directly impact the electrical properties of semiconductor devices. For instance, the presence of dislocations can hinder carrier mobility, leading to decreased performance in final applications. This article highlights the significance of recognizing these defects, underscoring that understanding their root causes is key to devising effective remedies.
The unique feature of defects is their complexity—they may arise not just from fabrication processes, but also from external environmental factors. Recognizing this multifaceted nature helps in crafting more resilient manufacturing strategies. However, the downside is that some defects can be elusive, often requiring advanced diagnostic tools for detection, which amplifies costs and complexity in the production process.
Mitigation Strategies
Addressing defects requires a multi-pronged approach. Among the most effective mitigation strategies are advanced material characterization techniques and robust process control methodologies. The hallmark of these strategies lies in their capacity to minimize defects both proactively and reactively. For example, using in-line metrology equipment helps monitor wafer quality throughout fabrication, thus catching potential defects before they snowball into larger issues.
A unique advantage of these strategies is their adaptability—techniques can be honed based on previous processing cycles and defects encountered. On the flip side, the implementation of advanced strategies often comes with a higher initial investment, which can deter smaller manufacturers. But in the grander scheme of wafer processing, the long-term savings and improved product yields present compelling reasons to invest in these approaches.
Scalability in Production
Process Integration Challenges
In the pursuit of scaling up production, manufacturers frequently encounter process integration challenges. These challenges primarily stem from the need to harmonize various fabrication steps while maintaining efficiency. Each step, from photolithography to etching, has distinct requirements, making it a balancing act to ensure they all work seamlessly together.
The key characteristic of this challenge is the complexity of workflow alignment; a change in one module can ripple through the entire production line. This complexity is most evident when introducing new technologies or materials, where existing infrastructure may not be readily compatible. The advantage of overcoming these integration hurdles is the potential for higher throughput and improved yield rates. However, the disadvantages include the time and cost associated with necessary adjustments and potential disruptions during the transition phase.
Cost-Effectiveness Concerns
Cost-effectiveness plays a crucial role in scaling production without compromising quality. Manufacturers are constantly on the lookout for methods to lower production costs while maximizing output. A significant characteristic of cost effectiveness is its dual nature: while it emphasizes reduced costs, it also insists on the need for high-quality end products.
In practice, achieving this balance requires innovative thinking and sometimes, a willingness to embrace slightly higher operational costs for long-term benefits. A unique aspect of considering cost-effectiveness in wafer processing is that it encourages the adoption of technologies like automation and AI-driven analytics. These tools can lend a hand in optimizing production lines, but they also require an upfront investment. On the downside, failing to address cost-effectiveness can lead to price increases for end products, making them less appealing in a competitive market.
In summary, the challenges in wafer processing—ranging from material defects to the complexities of scaling production—are intricate yet essential areas of focus. Understanding and mitigating these challenges not only improves production capabilities but also enhances overall device performance, paving the way for a more robust semiconductor industry.
Advancements in Wafer Processing Technology
In the world of semiconductor fabrication, advancements in wafer processing technology are nothing short of crucial. These developments not only streamline production but also enhance the quality and functionality of the devices produced. In an industry where precision is paramount, innovative techniques can mean the difference between an average chip and one that sets new benchmarks for performance and reliability.
As technology continually evolves, understanding these advancements can give researchers and professionals the edge they need to adapt and succeed. From new lithography methods to automation in production, these updates contribute not only to improved efficiency but also to reduced costs and enhanced performance of semiconductor devices.
Emerging Techniques
Nanoimprint Lithography
Nanoimprint lithography is a game-changer in the fabrication toolkit. By utilizing mechanical pressure to imprint patterns onto a resist layer, this method stands out due to its ability to create intricate nanostructures at a fraction of the cost compared to traditional lithography. One key characteristic is the low operational costs, which makes it a popular choice, especially for research and development environments where budgets may be tight.
A unique feature of nanoimprint lithography lies in its capacity for high-throughput patterning, which can significantly increase production rate without sacrificing detail. This technology benefits industries that demand exceptional precision, but it has some limitations. For instance, the complexity of template fabrication can introduce new challenges, potentially offsetting some gains in efficiency.
Laser Etching
Laser etching brings an exciting flair to wafer processing. Using highly focused laser beams, this technique achieves remarkable precision in removing material, allowing for detailed micro and nano-pattern creation on semiconductor surfaces. The high speed of laser etching is one of its most remarkable traits, making it an attractive option for those looking to boost throughput while maintaining quality.
One unique aspect of laser etching is its versatility; it can be applied to various materials, from silicon to polymers. However, it's not without drawbacks. The heat generated during the process can sometimes affect the substrate's integrity, which is a consideration that engineers must take into account.
Automation and Process Control
Smart Manufacturing Solutions
In today's fast-paced environment, smart manufacturing solutions offer an exciting avenue for advancement. These solutions leverage data analytics and machine learning to optimize the wafer processing workflow. Their main characteristic is the ability to adapt in real-time based on production conditions, allowing for highly efficient manufacturing processes.
These smart systems provide a way to predict equipment failures before they happen, reducing downtime. The unique feature of such solutions is their integration capabilities with existing systems, allowing seamless transitions into modernized operations. However, there can be initial hurdles, such as the need for employee training to handle these sophisticated systems effectively.
Real-Time Quality Assurance
Real-time quality assurance is a key player in ensuring that semiconductor devices meet the highest standards. Implementing real-time monitoring systems allows for immediate feedback during the manufacturing process. This adaptability is essential in maintaining consistency in device performance.
The ability to detect defects as they occur helps in minimizing waste and rework. A defining characteristic of real-time assurance is its contribution to predictive maintenance, enhancing overall efficiency. That said, the complexity of such monitoring systems can pose challenges regarding data management and analysis, which is critical for achieving the best outcomes.
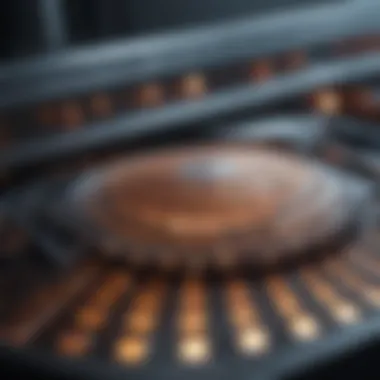
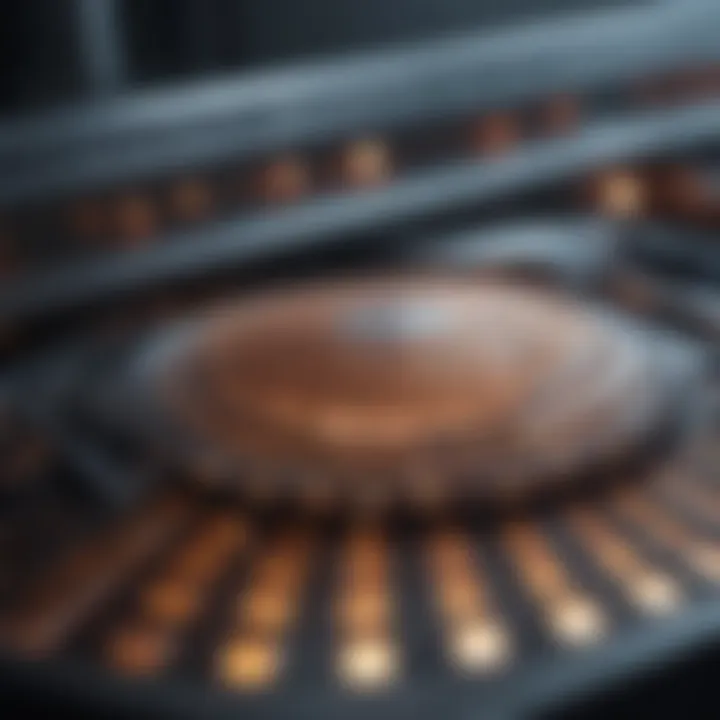
In summary, advancements in wafer processing technology significantly impact the semiconductor industry, presenting both exciting opportunities and challenges that must be navigated carefully.
In summary, advancements in wafer processing technology significantly impact the semiconductor industry, presenting both exciting opportunities and challenges that must be navigated carefully.
Impact of Wafer Processing on Device Performance
Wafer processing plays a vital role in determining the performance of semiconductor devices. The choices made during this intricate process heavily influence not only the efficiency and effectiveness of the devices but also their reliability and longevity. Understanding the connection between wafer processing and device performance is crucial for both manufacturers and researchers in the semiconductor field. This section will explore how material properties affect device functionality, as well as the implications of reliability in semiconductor devices.
Material Properties and Device Functionality
The materials used in semiconductor fabrication are essential for achieving desired functionalities. The intrinsic and extrinsic properties of semiconductor materials can make or break the performance of devices crafted from them.
- Doping Concentration: The precise control over doping processes, which involves introducing impurities to control electrical properties, is crucial. Too much or too little doping can lead to performance issues.
- Structural Integrity: Imperfections during wafer processing, such as dislocations or defects, directly affect how electrons move through materials. This can result in variations in performance, often reflected in increased failure rates.
- Thin Film Characteristics: Thin films, commonly used in devices, depend on the quality of surface processing. Factors such as surface roughness and layer uniformity can affect light absorption, conductivity, and overall efficiency.
Wafer processing affects the grain boundaries and layer interactions within materials, consequently influencing how well a device functions under diverse conditions. The materials should not only demonstrate good performance when first fabricated but also must maintain their functionality throughout the device’s lifespan.
Reliability and Longevity of Semiconductor Devices
In the realm of semiconductor technology, the reliability and longevity of devices is paramount. A key factor in enhancing longevity is the thoroughness of wafer processing methodologies. All aspects, from initial fabrication to final testing, can influence how long a device will last in operation.
- Thermal Stability: During processing, different methods can induce residual stresses or phase changes in the materials, impacting how well they withstand temperature changes. If a wafer isn’t treated correctly, it may suffer from heat-induced degradation.
- Environmental Resistance: Devices must be resilient to environmental factors such as humidity or chemical exposure. Proper wafer cleaning and surface treatments can enhance this resilience, ultimately leading to better longevity.
- Failure Mechanisms: Understanding potential failure mechanisms, like electromigration or thermal cycling, is vital for improving reliability. These issues often stem from the processing steps and material choices made during wafer fabrication.
"Device reliability depends not only on design but significantly on the processing methods used to develop the materials that comprise them."
"Device reliability depends not only on design but significantly on the processing methods used to develop the materials that comprise them."
Future Trends in Wafer Processing
The landscape of wafer processing is constantly shifting, influenced by the need for improved efficiency, sustainability, and the integration of novel materials. Understanding these trends is crucial for stakeholders in the semiconductor industry. The modern drive towards sustainability focuses on reducing the environmental impact of manufacturing processes. This convergence of technology and ecological concern is not merely fashionable; it represents a fundamental shift in how the industry views its responsibility to the planet. Moreover, as devices become increasingly sophisticated, the development of advanced materials—such as 2D materials and wide bandgap semiconductors—offers pathways to enhance performance while addressing these environmental challenges. Together, these elements are reshaping not just wafer processing but also the broader spectrum of microelectronics and device fabrication.
Sustainability and Eco-friendly Practices
Sustainability in wafer processing encompasses a plethora of approaches. As semiconductor manufacturing traditionally has been resource-intensive, there’s a growing emphasis on minimizing waste and energy consumption. Innovations such as water recycling systems, energy-efficient manufacturing equipment, and non-toxic chemicals are becoming paramount.
- Zero-waste initiatives are being prioritized to ensure that every bit of material is utilized effectively, reducing what gets sent to landfills.
- Renewable energy sources, like solar or wind, are increasingly integrated into production facilities, lowering the carbon footprint.
"Embracing sustainability is not just a good practice; it's quickly becoming a necessity for firms vying to remain competitive in this modern economy."
"Embracing sustainability is not just a good practice; it's quickly becoming a necessity for firms vying to remain competitive in this modern economy."
Integration of Advanced Materials
2D Materials
When discussing advanced materials, 2D materials gain significant attention. These materials, exemplified by graphene, consist of a single layer of atoms and exhibit exceptional electrical, thermal, and mechanical properties. Their unique structure allows high flexibility with an incredibly low weight.
- Key characteristic: The exceptional electronic properties make them highly efficient for use in high-speed transistors and flexible electronics.
- Why it's beneficial: The high conductivity and flexibility make 2D materials a prime candidate for next-gen electronic applications, offering unprecedented performance metrics.
However, the integration of 2D materials is not without challenges. Synthesis methods can be both complex and expensive, which can impact scalability in conventional manufacturing settings.
Wide Bandgap Semiconductors
Meanwhile, wide bandgap semiconductors also deserve spotlight. These materials, such as silicon carbide (SiC) and gallium nitride (GaN), are known for their ability to operate at high voltage, high frequency, and high temperatures. This attributes to their increasing use in power electronics, where efficiency is critical.
- Key characteristic: A wide bandgap enables devices to handle higher voltages without compromising performance.
- Beneficial choice: As demand for energy-efficient solutions burgeons, these semiconductors facilitate the development of smaller, more efficient devices in applications ranging from renewable energy to electric vehicles.
Despite their advantages, the cost and technical complexity involved in the manufacturing process of wide bandgap semiconductors cannot be overlooked. Nonetheless, as technology progresses, these issues may be addressed, paving the way for broader adoption.
Culmination and Perspectives
As we reach the final chapter of this exploration, it’s essential to reflect on the magnitude of wafer processing in the realm of semiconductor technology. Wafer processing, while often seen as a series of meticulous steps, embodies a larger narrative of innovation, precision, and the sheer will to enhance electronic capabilities.
Recap of Key Insights
To summarize the essential points discussed, wafer processing comprises myriad stages that combine to form the core of semiconductor device manufacturing. From the selection of high-quality materials during fabrication to the complexities of photolithography and etching, each element holds significant weight in the overall functionality of microelectronics. The following insights stand out:
- Material Quality: The performance of semiconductor devices hinges largely on the quality of the wafers produced. Each inconsistency during the processing stages can lead to defects that adversely affect device reliability.
- Technological Advancements: Emerging techniques such as nanoimprint lithography and automation in process control enhance efficiency and yield, pushing the boundaries of what semiconductors can achieve.
- Sustainability Considerations: The future of wafer processing isn't just about performance; it also involves integrating eco-friendly practices to reduce waste and energy consumption without compromising quality.
"Innovation in wafer processing not only shapes the devices of today but also lays the groundwork for the technologies of tomorrow."
"Innovation in wafer processing not only shapes the devices of today but also lays the groundwork for the technologies of tomorrow."
The Future of Wafer Processing in Technology
Looking ahead, the landscape of wafer processing is poised for transformative change. Several key trends are emerging that could redefine the technology:
- Integration with AI: As artificial intelligence continues to permeate various industries, its incorporation into wafer manufacturing could lead to smarter manufacturing solutions. This integration may enhance quality assurance and optimize production runs.
- Development of 2D Materials: The exploration of new materials such as graphene or transition metal dichalcogenides could allow for devices that are not only faster and more efficient but also significantly smaller in size. This could lead to groundbreaking changes in how electronics are designed and implemented.
- Adoption of Circular Economy Principles: With an increasing focus on sustainability, the semiconductor industry may adopt practices that emphasize recycling and reusability of materials, creating a closed-loop system in wafer processing.
- Collaboration Across Disciplines: As technology evolves, cross-disciplinary partnerships among physicists, materials scientists, and engineers become more critical. Stronger collaborations can lead to innovative solutions for existing challenges in wafer processing.
In closing, wafer processing is not merely a phase in semiconductor production; it is a cornerstone of technological advancement. Keeping an eye on these developments will serve to not only inform researchers and practitioners in microelectronics but also ensure that we remain at the forefront of innovation in a rapidly evolving field.