Advancements and Applications of Titanium Printers
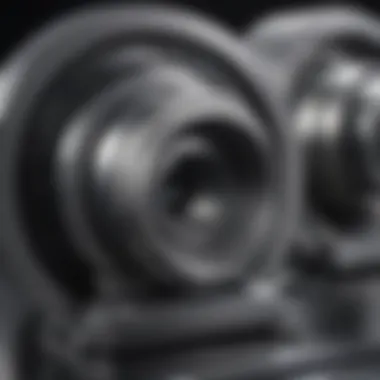
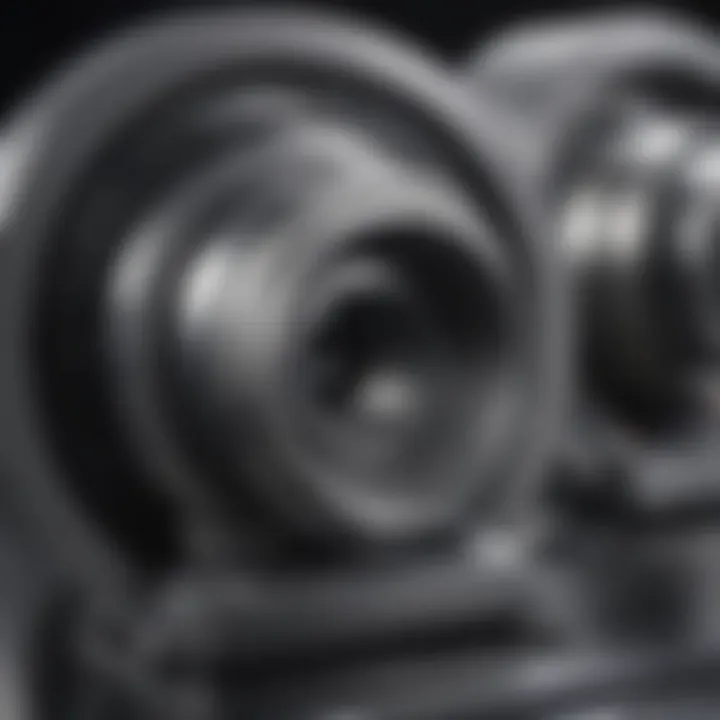
Article Overview
Purpose of the Article
The purpose of this article is to shed light on the fascinating world of titanium printers, exploring their evolution, applications, and practical significance in various industries. As additive manufacturing continues to gain momentum, understanding the role of titanium printers becomes crucial. They are not just tools; they represent a leap in technology that can revolutionize how products are designed and crafted. By delving into the intricacies of titanium printing, we aim to equip readers with insights that bridge technology and practicality, offering a comprehensive understanding of this specialized field.
Relevance to Multiple Disciplines
Titanium printers touch numerous sectors, each with unique needs and applications. This relevance spans from aerospace – where lightweight and strong components are paramount – to healthcare, particularly in creating custom implants. The automotive industry benefits too, realizing the potential of titanium in reducing vehicle weight while enhancing durability. Moreover, academic circles find titanium printers an intriguing subject for research, frequently exploring material properties and innovative printing techniques. The versatility across disciplines underscores the importance of this article, aiming to equip students, researchers, educators, and industry professionals with critical knowledge and understanding.
Research Background
Historical Context
To truly grasp the advancements in titanium printing, one must briefly glance at its history. Titanium itself, once a relatively obscure metal known for its strength-to-weight ratio, gained prominence post-World War II. Initially used in aerospace applications, the material's resistance to corrosion and ability to withstand extreme temperatures set the stage for its future in manufacturing.
The emergence of 3D printing technologies in the late 20th century opened new avenues for titanium's application. This convergence innovated production processes, enabling the creation of complex structures that were previously impossible or inefficient to fabricate using traditional methods. Over the decades, numerous breakthroughs have occurred, leading to the sophisticated titanium printers that are available today.
Key Concepts and Definitions
When discussing titanium printers, it’s essential to clarify some key concepts that often surface in related literature:
- Additive Manufacturing (AM): This refers to the layer-by-layer process of creating objects, contrasting with traditional subtractive methods where material is removed.
- Direct Energy Deposition (DED): A process where focused thermal energy is used to fuse materials by melting them as they are deposited.
- Selective Laser Melting (SLM): A popular technique that utilizes high-power lasers to fuse particles of titanium powder, enabling excellent material properties and fine detail.
Understanding these terms helps contextualize the technology's capabilities and challenges, laying a foundation for a deeper exploration of the applications and innovations within titanium printing.
Intro to Titanium Printing Technology
The domain of titanium printing technology encompasses a myriad of innovations that have transformed the landscape of manufacturing. This technology, a slice of additive manufacturing, revolves around producing intricate parts from titanium, a metal revered for its robustness and lightweight characteristics. The significance of titanium printers extends beyond just their capabilities; they serve as a catalyst for innovation in a range of industries, including aerospace, medicine, and automotive. By delving into the world of titanium printing, one can appreciate the seamless marriage of state-of-the-art technology and engineering prowess.
Historical Context
The journey of titanium printing technology is woven with a rich history that dates back to the mid-20th century when titanium itself was first extracted and utilized in various applications. Initially, titanium was considered too expensive and difficult to work with, making its widespread use in manufacturing limp. However, the dawn of the 21st century brought forth advancements in digital fabrication and printing technologies that changed everything.
In the early 2000s, the advent of selective laser melting (SLM) techniques began shifting perceptions of titanium’s accessibility. This marked a pivotal moment for industries that thrived on innovation. The early adopters of titanium printers, primarily in the aerospace sector, showcased how these machines could create lighter, stronger components compared to traditional manufacturing methods. Fast forward to today, and titanium printing technologies have expanded vastly, finding applications in complex geometries that were once thought impossible.
Definition of Titanium Printers
In simplest terms, titanium printers refer to specialized additive manufacturing machines designed to produce three-dimensional objects from titanium powders. These printers utilize several methods, primarily involving laser or electron beam melting, to layer-by-layer fuse titanium. The incredible versatility of these printers enables them to create components that are both highly intricate and extremely durable.
Key Features of Titanium Printers:
- High Precision: Capable of creating complex geometries with fine detail.
- Material Efficiency: Minimizes waste by using only what’s necessary, suitable for expensive materials like titanium.
- Customization: Easily tailored for specific applications such as medical implants or aerospace components.
Titanium printers not only illustrate the capabilities of modern machinery but also embody the shift toward a more efficient paradigm of production in various industries. As we explore the scientific aspects and feasible applications of these printers, we can better appreciate their role in shaping the future of manufacturing.
The Science Behind Titanium Printing
The realm of titanium printing combines deep-rooted scientific principles with innovative engineering solutions. This intersection not only reveals the intricate workings of additive manufacturing but also showcases the evolution and versatility of titanium as a resource in various industries. Understanding the science behind this technology is crucial for grasping its potential advantages and limitations.
Materials Used in Titanium Printing
Titanium, known for its strength-to-weight ratio and corrosion resistance, serves as the foundational material in titanium printing. However, the quality of printed parts hinges on specific alloy compositions. Popular titanium alloys like Ti-6Al-4V—comprising aluminum and vanadium—are frequently employed due to their balance of mechanical properties and weldability.
Other materials, such as titanium aluminide, have recently gained traction for their lightweight properties and excellent high-temperature performance, particularly in aerospace applications. The choice of these materials is influenced by intended application and performance criteria.
Moreover, how these materials are processed during the printing stage is essential. Various powder bed fusion methods, inclusive of different particles sizes and distributions, affect the adhesion between layers and, ultimately, the strength of the final product.
Printing Techniques and Methods
Selective Laser Melting
Selective Laser Melting (SLM) stands out as a popular method in titanium printing. In SLM, a high-powered laser precisely melts titanium powder layer by layer. This technique allows for dense material formation, which is pivotal for producing critical components in aerospace and medical industries.
One key characteristic of SLM is the ability to create complex geometries that are often impossible with traditional manufacturing methods. This capability opens doors for lightweight designs and optimizes material usage. However, pitfalls include potential thermal stress and defects like porosity generated during the cooling process.
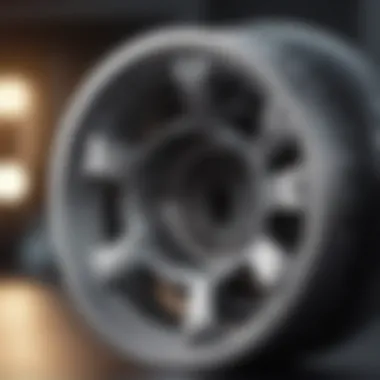
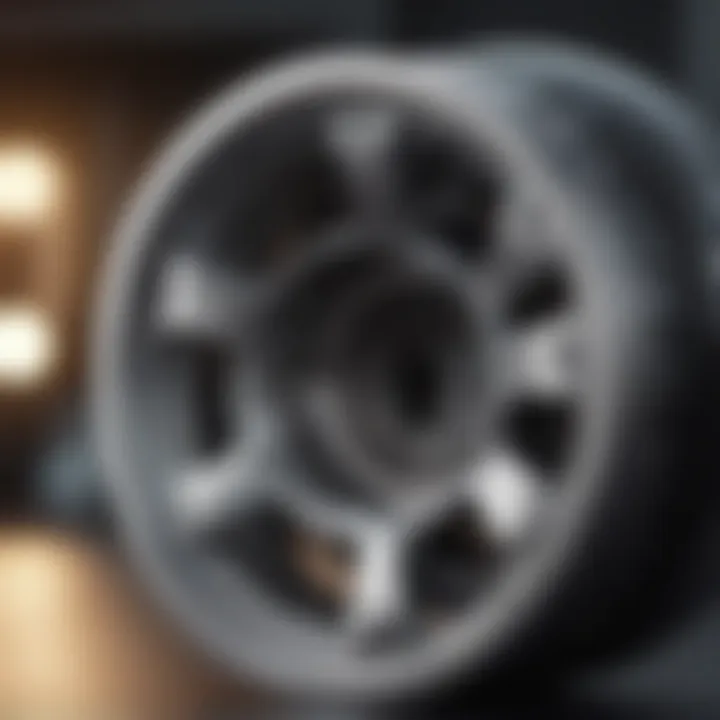
Electron Beam Melting
Electron Beam Melting (EBM) operates similarly to SLM but employs an electron beam in a vacuum instead of a laser. This method excels in producing larger parts and is especially favored in aerospace for its ability to achieve superior mechanical properties.
The key attribute of EBM is its efficiency in processing thick layers of titanium. This capability reduces build times significantly, making it an attractive choice for mass production. However, the equipment's high cost and specific limitations related to material handling can be barriers for some manufacturers.
Direct Energy Deposition
Direct Energy Deposition (DED) is another significant method where metallic powder or wire is melted and deposited through a nozzle as the laser or electron beam moves, layering material onto existing structures. This technique excels in repair applications and adding features to existing components.
The distinctive feature of DED is its ability to combine additive manufacturing with traditional subtractive methods like machining and welding. While it offers considerable flexibility in design modifications, challenges like part distortion due to heat input can complicate the process.
Understanding the science behind titanium printing not only reveals the potential of the technology but also the intricacies of material behavior during processing and application.
Understanding the science behind titanium printing not only reveals the potential of the technology but also the intricacies of material behavior during processing and application.
As industries continue to embrace titanium printing, the importance of mastering these techniques and materials cannot be understated. Navigating the wealth of options enables improved product design and functionality, pushing the boundaries of what's possible in manufacturing.
Comparative Analysis of Titanium and Other Materials
In the world of manufacturing and engineering, choosing the right material can mean the difference between success and failure. The comparative analysis of titanium against other materials is crucial for understanding its unique advantages and possible shortcomings. This analysis helps industries to make informed decisions, influencing everything from design choices to cost implications. As we delve deeper into the advantages and limitations of titanium printing, it becomes clear that this material holds its own in select contexts but isn't without its challenges.
Advantages of Titanium over Other Metals
Titanium offers a plethora of benefits that set it apart from other metals like steel and aluminum. Here are some compelling reasons why titanium shines in various applications:
- Strength-to-Weight Ratio: Titanium is significantly lighter than steel while maintaining exceptional strength. This quality is indispensable in industries like aerospace, where every gram counts, and performance is paramount.
- Corrosion Resistance: Titanium naturally forms a protective oxide layer, making it highly resistant to rust and a variety of environmental factors. This property extends the lifespan of components, particularly in marine and chemical applications.
- Biocompatibility: In the medical field, titanium's compatibility with human tissue is pivotal for implants and prosthetics. This ensures reduced rejection rates and successful surgical outcomes.
- Durability: Items manufactured from titanium tend to withstand fatigue and wear better than those made from other metals. This durability can result in lower maintenance costs and fewer replacements.
- Design Flexibility: Titanium's properties allow for intricate designs that might be impractical with other materials. Additive manufacturing techniques can produce complex geometries, which are increasingly valuable in customized applications.
"Titanium isn't just another metal; it's a game changer in industries where performance and reliability are not optional."
"Titanium isn't just another metal; it's a game changer in industries where performance and reliability are not optional."
Limitations of Titanium Printing
Despite its many advantages, titanium printing is not without limitations.
- Cost: One of the most significant hindrances to titanium’s widespread usage is its cost. The raw material and production processes can be expensive, which might deter businesses from choosing titanium for certain projects.
- Processing Challenges: Printing titanium often requires specialized equipment and considerable expertise. This can lead to longer lead times and the necessity for skilled personnel, which is not always readily available.
- Thermal Properties: Titanium has high thermal conductivity. This can lead to warping during the printing process if not managed correctly. The appropriate settings and post-processing techniques are vital to avoid these issues.
- Limited Production Scale: While 3D printing titanium is revolutionizing production, scaling up can be difficult. Large parts may not always be feasible, and there can be limits to the dimensions achievable through current technologies.
In summary, both the advantages and limitations of titanium must be carefully weighed in the context of specific applications. Understanding these factors can help industries navigate the decision-making process when incorporating titanium into their projects.
Applications of Titanium Printing in Industry
Titanium printing technology offers a range of advantages that can be harnessed across various sectors, making it a focal point for modern manufacturing. Its applications are not just about the innovation of 3D printing but encompass the deeper integration of aerospace, medical, and automotive industries. Each application area reveals specific benefits associated with titanium printing that underline its importance in shaping the future of these sectors.
Aerospace Industry
Components and Structures
In the aerospace industry, titanium printing is particularly significant when it comes to components and structures. Aircraft parts, such as brackets, support beams, and other complex geometries, benefit from the layer-by-layer manufacturing process. This process allows for shapes that are not only lighter but also optimized for aerodynamic performance. The ability to create intricately designed components can markedly increase fuel efficiency.
One key characteristic of titanium in aerospace is its strength-to-weight ratio. For each component manufactured, the use of titanium reduces weight while enhancing durability under stress. This makes it a preferred material for critical applications. The unique feature of titanium printing here is its ability to customize parts for specific aircraft models, leading to reduced maintenance costs in the long run. However, the technical limitations in precision and dimensional accuracy do pose challenges that manufacturers must navigate.
Weight Savings and Performance
The dimension of weight savings and performance cannot be overstated in aerospace applications. Using titanium allows manufacturers to shave off pounds without compromising integrity or durability. This aspect is integral to achieving optimal performance, as every ounce counts during flight, affecting fuel consumption and overall efficiency.
Moreover, titanium's resistance to corrosion makes it ideal for components exposed to harsh environments, such as high-altitude and high-pressure conditions. This characteristic not only contributes to the longevity of parts but also minimizes the frequency of repairs, ultimately leading to cost savings. However, obtaining titanium can be expensive, which sometimes offsets the benefits of lower overall operational costs.
Medical Sector
Implants and Prosthetics
Moving to the medical domain, the application of titanium printing is vital for the development of implants and prosthetics. The unique biocompatibility of titanium allows these printed devices to seamlessly integrate into the human body. Unlike other metals, titanium rarely causes adverse reactions, making it a top choice for implants that are meant to be permanent or semi-permanent.
Customizability is another hallmark of titanium printing in this sector. Surgeons can request tailored implants that fit the unique anatomical features of their patients, providing a level of personalization that enhances outcomes. However, the process of regulatory approval can be an extensive hurdle, causing delays from conception to practice in clinical settings.
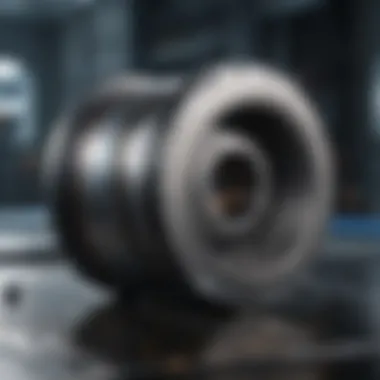
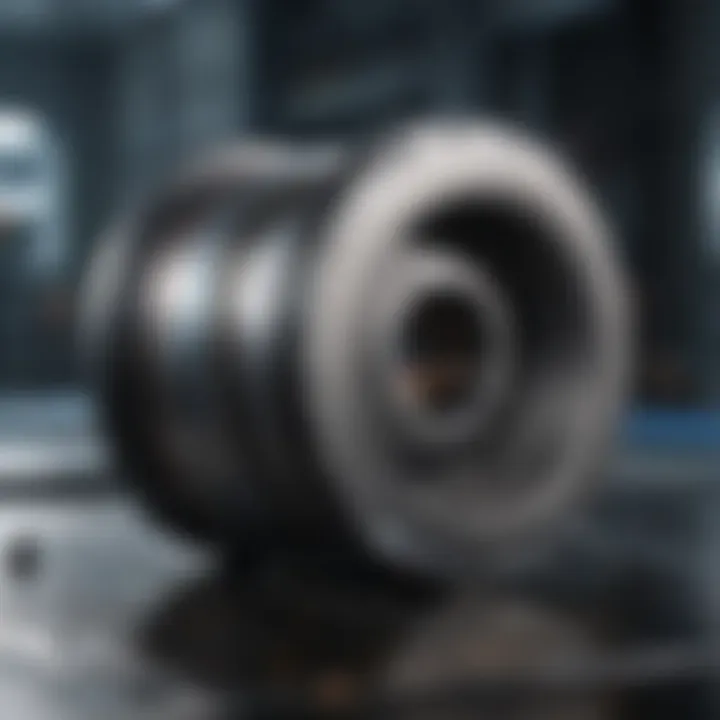
Surgical Instruments
Surgical instruments produced through titanium printing provide a significant advantage in terms of precision and performance. Their lightweight nature reduces fatigue for surgical teams during lengthy operations while maintaining strength for high-stress applications. This is crucial for tools like clamps, scalpels, and forceps, which require both durability and usability.
Additionally, the intricate designs achievable through titanium printing can lead to enhanced functionality. Filters, specialized grips, and ergonomically designed handles can all be manufactured to meet the exact needs of the operating environment. However, the cost associated with titanium printing of surgical instruments may limit widespread adoption, necessitating careful economical assessment by healthcare facilities.
Automotive Applications
In the automotive realm, the advantages of titanium printing start to shine through as well. With an increasing demand for lightweight materials that do not compromise on performance or safety, titanium has begun to carve its niche. From custom components for racing cars—where every gram of weight reduction counts—to parts in everyday vehicles, its role continues to expand.
The adaptation of titanium printing in automotive performance parts, such as exhaust systems and crankshafts, is particularly notable. These components often endure high temperatures and pressure, making titanium’s heat resistance invaluable. However, it's important to note that the adoption of such advanced technologies requires significant investment and upskilling of the workforce.
Overall, the applications of titanium printing across these industries paint a picture of innovation fueled by material science, meeting the demands of modern manufacturing.
Titanium printing stands as a testament to the capabilities of contemporary additive manufacturing, shaping industries by offering unprecedented levels of precision and customization.
Titanium printing stands as a testament to the capabilities of contemporary additive manufacturing, shaping industries by offering unprecedented levels of precision and customization.
Technological Innovations in Titanium Printing
The landscape of titanium printing is rapidly evolving, reshaping how industries approach manufacturing and design. This section delves into two pivotal aspects of these advancements: the integration of advanced technologies and emerging research trends. Each of these factors plays a crucial role in enhancing the efficiency, precision, and capability of titanium printers, making them indispensable in modern manufacturing.
Integration with Advanced Technologies
Artificial Intelligence
Artificial Intelligence (AI) has found its way into titanium printing, offering new horizons for automation and optimization. By leveraging AI, manufacturers can analyze large sets of data to improve the printing process. This utilization of data helps predict failures and optimize machine parameters, which ultimately leads to better quality outputs and reduced waste. One key characteristic of AI in this setting is its ability to learn from previous printing processes. This characteristic makes AI a popular choice as it allows for continuous improvement in manufacturing cycles.
However, the inclusion of AI isn't without its challenges. The unique feature of AI, while powerful, requires considerable initial calibration and training. This can be time-consuming and may involve upfront costs that some manufacturers might find prohibitive. Yet, the long-term advantages—such as increased reliability and reduced material costs—often outweigh these initial hurdles, making AI a strong contender in the future of titanium printing.
Machine Learning Applications
Similarly, Machine Learning (ML) applications have emerged as a transformative force in titanium printing. ML enables systems to learn and adapt through experience, making it particularly effective in refining the complexities of titanium printing processes. The key characteristic of ML is its ability to analyze patterns and adjust parameters dynamically, which enhances the printer's capability to handle various types of titanium alloys and complex geometries.
One intriguing unique feature of ML is its potential for predictive analytics. This allows manufacturers to identify potential failures ahead of time and takes corrective actions before they occur. However, adopting ML technology can be a double-edged sword. The advantages lie in reduced downtime and improved results, while the flip side is that there might be a steep learning curve involved for technicians and engineers, requiring additional training and expertise in handling such advanced systems.
Emerging Trends in Research
Research into titanium printing is witnessing a surge, driven by the need for more efficient and versatile manufacturing solutions. Some promising trends include:
- Development of New Materials: Ongoing research is looking to enhance titanium alloys used in printing, improving durability and performance while lowering costs.
- Enhanced Printing Techniques: New methods are being explored to refine laser and electron beam technologies, focusing on speed and accuracy.
- Sustainability Initiatives: Efforts are underway to make titanium printing more environmentally friendly, with a focus on recycling and minimizing waste.
These trends signal a rapidly expanding frontier in titanium printing, pushing the boundaries of what is possible while addressing the industry's pressing needs. The confluence of technological innovation and dedicated research underscores the momentum this field has gained, making it a key subject of interest for professionals and academics alike.
"Technological advancements in titanium printing promise not just increased capabilities, but a significant shift in manufacturing paradigms, emphasizing efficiency and sustainability."
"Technological advancements in titanium printing promise not just increased capabilities, but a significant shift in manufacturing paradigms, emphasizing efficiency and sustainability."
Economic Implications of Titanium Printing
The economic implications of titanium printing extend beyond the mere act of manufacturing products. Understanding these implications helps to frame how titanium printing fits into the broader spectrum of modern manufacturing and its impact on various sectors. As industries continuously seek lower costs and efficiency improvements, titanium printing presents both significant advantages and considerations that must be analyzed carefully. This section will delve into two key areas: the cost-benefit analysis of titanium printing techniques, along with current market trends and growth prospects.
Cost-Benefit Analysis
When assessing the economic viability of titanium printing, a detailed cost-benefit analysis is paramount. Here are several aspects to consider:
- Initial Investment: Titanium printers often come with a hefty price tag. The equipment, maintenance, and necessary materials contribute to a significant upfront cost. Yet, this should be weighed against long-term savings.
- Material Efficiency: One of the standout benefits of titanium printing is its ability to minimize waste. Traditional manufacturing methods often result in excess material that doesn't make it into the final product. Titanium printers, on the other hand, utilize additive manufacturing techniques, which means material is only used where necessary.
- Complex Design Capability: Titanium printing allows for the production of intricate designs that would be prohibitively expensive or impossible to achieve with traditional methods. This flexibility can open doors for innovation and new products, which can positively affect an organization's bottom line.
- Speed to Market: With the potential for rapid prototyping, companies can bring products to market much faster. This speed can lead to early returns on investment and a competitive edge in their respective fields.
A well-rounded economic analysis requires not just a look at upfront costs and savings but also a focus on these broader strategic benefits that titanium printing offers business leaders today.
Market Trends and Growth Prospects
The market for titanium printing is experiencing notable growth, driven by demand across various industries. Here are some key trends:
- Aerospace Demand: The aerospace sector remains a strong customer for titanium printing. With the need for lightweight yet robust components, the market is expected to grow significantly as companies aim for fuel efficiency and performance enhancements.
- Medical Applications: The ability to print customized implants and surgical instruments is reshaping the medical landscape. Tailored solutions in healthcare are gaining traction, leading to increased investments in titanium printing within this arena.
- Automotive Innovations: As electric vehicle technology advances, manufacturers are beginning to embrace titanium for its strength-to-weight ratio. This can result in higher efficiency and better performance, further pushing demand.
- Research and Development Efforts: As research institutions increase their focus on titanium printing, breakthroughs are likely to lead to innovative applications and improved technologies, further propelling market growth.
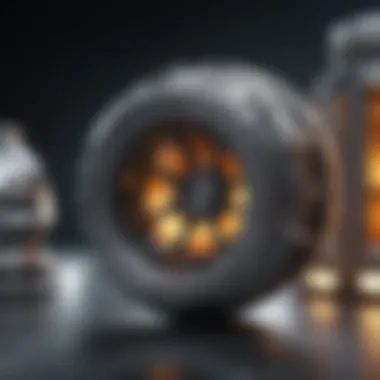
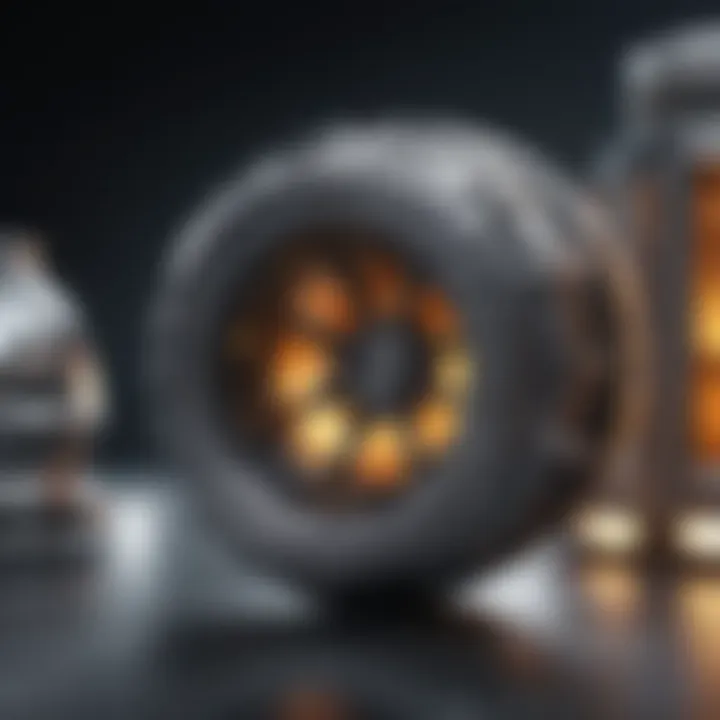
"Titanium printing stands at the intersection of innovation and efficiency, promising substantial contributions to economic growth across multiple sectors."
"Titanium printing stands at the intersection of innovation and efficiency, promising substantial contributions to economic growth across multiple sectors."
In summary, the economic implications of titanium printing are significant, offering both cost benefits and growth potential in various markets. As industries strive for greater efficiency and adaptability, titanium printing will likely play a crucial role in shaping the future of manufacturing.
Challenges Facing Titanium Printers
The topic of challenges facing titanium printers holds significant weight in understanding the dynamics of this cutting-edge manufacturing technology. While titanium printing offers immense potential, it is not without its hurdles. Recognizing these challenges is crucial, as they directly influence the efficiency, practicality, and overall acceptance of this technology in various industries. These obstacles can hinder development and prevent wider adoption, which is why they warrant attention. Here, I will explore specific elements relating to technical limitations and material costs, shedding light on how they can affect the implementation of titanium printing.
Technical Limitations
The realm of titanium printing does boast impressive capabilities, yet it is constrained by certain technical limitations that hinder its progress. For instance, many of the printers available today struggle with achieving consistency in layer quality. This inconsistency can lead to problems such as warping or imperfections in the final product. Furthermore, the parameters for printing titanium, like temperature and speed, need to be meticulously controlled. Otherwise, one may end up with a product that lacks the desired mechanical properties or dimensional accuracy.
Another aspect not commonly considered is the role of post-processing in titanium printing. Often, parts produced through these methods require additional steps—like heat treatment or surface finishing—before they are ready for end use. This necessitates extra time and costs, potentially negating some benefits attributed to additive manufacturing.
"Inconsistencies in layer quality can result in significant compromises in mechanical properties, which is a primary concern for sectors requiring strict adherence to specifications."
"Inconsistencies in layer quality can result in significant compromises in mechanical properties, which is a primary concern for sectors requiring strict adherence to specifications."
Material Costs and Availability
In the context of titanium printing, the costs associated with raw materials can become a significant barrier. Titanium powder, essential for the process, is inherently expensive compared to other metals. The procurement of this powder can be daunting, especially since the quality can vary drastically between suppliers. Not only do businesses need to find a reliable source, but they must also appraise the quality of the material they are using to produce their components.
There’s a concern around the availability of titanium itself. While titanium is abundant in the Earth's crust, the extraction and processing remain costly and capital-intensive processes. As demand for titanium components rises across various industries—from aerospace to medical—the strain on supply chains can lead to increased costs and availability issues. Businesses might find themselves in tight spots with fluctuating prices that can affect their project budgets.
To summarize, while titanium printers offer notable advancements in manufacturing, the challenges of technical limitations and material costs present significant considerations for industries looking to invest in this technology. The quest for a more refined approach to titanium printing continues, driven by the need to overcome these hurdles and enhance the viability of this promising manufacturing avenue.
Future of Titanium Printing
The future of titanium printing is a pressing topic, weaving together the threads of innovation, industry demand, and evolving technology. As we delve into this narrative, understanding how titanium printers can transform manufacturing processes is essential. For industries focused on precision, durability, and lightness—such as aerospace and medical—advancements in titanium printing will pave the way for products that meet stringent specifications while minimizing waste.
Anticipated Advancements
Looking ahead, several key advancements in titanium printing technology are on the horizon. The integration of smart manufacturing technologies is likely to facilitate higher degrees of automation and precision. This could lead to self-optimizing printing processes, where machines learn from previous prints to maximize efficiency and reduce errors.
- Hybrid Manufacturing Techniques: Combining subtractive and additive manufacturing processes may result in more complex structures that utilize titanium’s strengths while minimizing its weaknesses. For instance, a part could be printed and then machined for finer details.
- Enhanced Materials: Future developments may introduce new titanium alloys or composite materials, increasing functionality and performance. The focus will often be on improving mechanical properties without sacrificing lightweight attributes.
- Sustainability Initiatives: With an increasing emphasis on sustainable practices, the exploration of recycled titanium powders might gain traction. This would serve to both reduce costs and bolster eco-friendly operations.
- Rapid Prototyping: Innovations in 3D printing technologies could lead to quicker turnaround times for prototypes, allowing manufacturers to iterate designs swiftly, thus speeding up product development cycles.
"The shifting landscape of manufacturing demands that titanium printing adapts. The market is constantly hungry for not just what works but also what improves upon existing solutions."
"The shifting landscape of manufacturing demands that titanium printing adapts. The market is constantly hungry for not just what works but also what improves upon existing solutions."
These advancements promise to redefine manufacturing capabilities, enhancing titanium’s role in various high-tech applications.
The Role of Research Institutions
Research institutions will play a pivotal role in steering the future of titanium printing. Their influence manifests in multiple ways, from pioneering novel technologies to validating new applications of titanium materials in wider contexts. They are the breeding grounds for experimentation and innovation.
- Collaborative Research: Partnerships between universities and industries can result in groundbreaking discoveries. By pooling resources, they can tackle grand challenges in titanium printing, such as developing heat-resistant alloys for aerospace applications or biocompatible materials for medical implants.
- Funding and Grants: Institutions often receive grants aimed at specific breakthroughs. These funds enable researchers to explore ambitious projects, pushing the boundaries of what titanium printing can achieve.
- Educating the Workforce: As industries evolve, there’s a growing need for skilled personnel. Research institutions are crucial in preparing the next generation of engineers and scientists, offering courses and hands-on experiences in advanced titanium printing technologies.
- Publishing Research: The dissemination of research findings in reputable journals can facilitate knowledge sharing among professionals in the field, guiding practitioners toward successful applications of titanium printing.
In summary, the future of titanium printing is bright, driven by advancements in technology and the foundational support of research institutions. This symbiosis will undoubtedly catalyze new applications, ensuring titanium printing's vital role in modern manufacturing for years to come.
End
As we draw the curtain on this exploration of titanium printers, it's evident that this technology is not only transforming industries but also shaping the future of manufacturing itself. The conclusion encapsulates a nuanced understanding of titanium printing, tying together its advancements, applications, and the potential that lies ahead.
Summary of Insights
Throughout this article, we highlighted the historical context leading up to current titanium printing technologies, comprehensively presenting the materials and methodologies that underpin this innovative practice. By diving into the specific advantages titanium offers over traditional metals, it’s clear how it has carved its niche in critical sectors. Moreover, we examined the economic implications—balancing the high initial cost of titanium printing with its long-term value in terms of performance and efficiency.
A clear takeaway is that while challenges persist, such as material costs and technical limitations, the growth of hybrid approaches and innovative research is paving the way for more efficient processes. The prominent role of titanium in aerospace, medical, and automotive fields exemplifies its versatile nature and the profound impact it can have on advancements in these industries.
“Titanium represents the so-called gold standard for high-performance applications due to its strength-to-weight ratio.”
“Titanium represents the so-called gold standard for high-performance applications due to its strength-to-weight ratio.”
Final Thoughts on the Evolution of Titanium Printing
Reflecting on the evolution of titanium printing, one cannot ignore the significant strides made over the past decades. From initial rudimentary techniques to the integration of advanced technologies like artificial intelligence, the field is witnessing unprecedented growth. Future advancements are likely to include further refinements in the printing process, such as improved laser efficiencies and material formulations, catering to a higher fidelity in product output and sustainability in manufacturing.
As research institutions collaborate with industries, the infusion of knowledge and technology will help in addressing existing limitations, thus enhancing the capabilities of titanium printers. It’s crucial for stakeholders in this domain to remain cognizant of these advancements, adapting and innovating as the landscape changes.