Exploring the Versatility of PTFE Foil: Properties & Uses
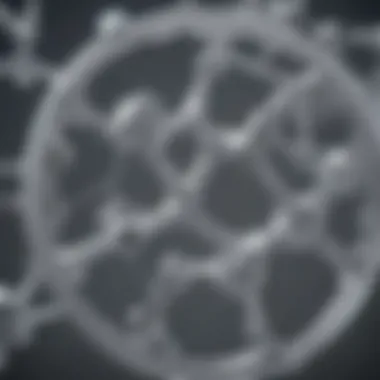
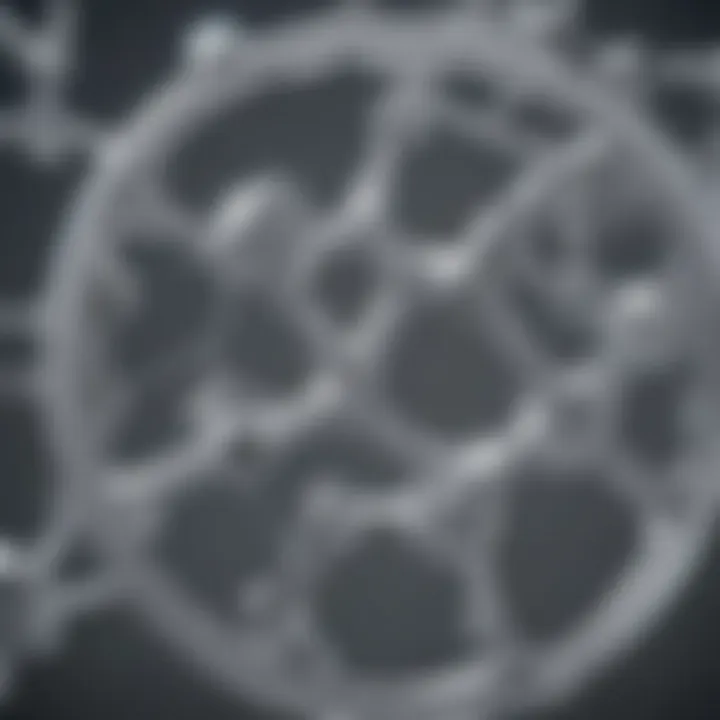
Article Overview
Purpose of the Article
The main aim of this article is to provide a detailed understanding of polytetrafluoroethylene (PTFE) foil, highlighting its distinct properties and wide-ranging applications. Readers will find an in-depth examination of its chemical structure and physical attributes, alongside a discussion on how these features contribute to its effectiveness in various uses. By dissecting the manufacturing processes and innovations surrounding PTFE foil, this article aspires to serve as a comprehensive resource for scholars and industry experts.
Relevance to Multiple Disciplines
PTFE foil holds significance across several sectors, including but not limited to the aerospace, medical, and electronic industries. Its non-stick, heat-resistant, and chemically inert properties make it applicable in fields that demand high-performance materials. The ongoing advancements in PTFE technology further emphasize its relevance in modern manufacturing and product design.
Research Background
Historical Context
Polytetrafluoroethylene was discovered in 1938 by Dr. Roy Plunkett. Initially used for military applications, the exceptional properties of PTFE quickly led it into commercial uses. Over the decades, its role expanded into various areas, evolving with technological advancements and responding to the demands of different fields.
Key Concepts and Definitions
PTFE is a fluoropolymer, which means it is composed of a chain of carbon atoms with attached fluorine atoms. This structure provides PTFE with its notable resistance to heat and chemicals. The process to create PTFE foil involves careful control of temperature and pressure to achieve desired thickness and characteristics. The properties of PTFE foil include:
- Low friction: Reduces wear in mechanical applications.
- High thermal stability: Functions in extreme temperature environments without degrading.
- Chemical resistance: Essential for applications in corrosive environments.
Understanding these foundational aspects sets the stage for exploring PTFE foil's applications and future developments.
Prolusion to PTFE Foil
Polytetrafluoroethylene (PTFE) foil has emerged as a crucial material across many industries. It is renowned for its non-stick properties and exceptional chemical resistance. Understanding PTFE foil begins with recognizing its definition, composition, and historical significance. This article will unfold how these factors contribute to its applications and innovations.
Definition and Composition
PTFE is a high-performance polymer that belongs to the fluoropolymer family. It consists of carbon and fluorine atoms, forming a chain that gives it distinct characteristics. The structural formula is [ -C_2F_4- ] . This unique arrangement results in a material that is stable, resilient, and capable of withstanding harsh environmental conditions.
The composition is essential for its wide range of applications, from industrial to residential uses. Its properties include an extremely low coefficient of friction and high thermal resistance. These qualities allow PTFE foil to serve effectively in demanding environments.
Historical Context
The history of PTFE dates back to the 1930s when it was accidentally discovered by Dr. Roy Plunkett. Originally, it was used in refrigeration systems but soon found a place in various industries due to its unique benefits. Not long after its discovery, applications expanded dramatically, particularly in aerospace and electronics.
Over the years, manufacturers have refined the production processes of PTFE, enhancing its availability and versatility. The significance of PTFE in modern technology is immense, often used in situations where other materials would fail.
Through this narrative, one gains insight into the foundational aspects of PTFE foil, setting the stage for a deeper exploration into its chemical and physical properties, as well as its diverse applications.
Chemical Properties of PTFE
The chemical properties of PTFE (Polytetrafluoroethylene) are central to its functionality and varied applications. Understanding these properties helps professionals and researchers to appreciate why PTFE is favored in many demanding environments. Key attributes like molecular structure, thermal stability, and electrical insulation highlight PTFE's unique advantages in industrial applications. Knowing how these properties influence its behavior under different conditions is essential.
Molecular Structure
PTFE is a polymer composed of carbon and fluorine atoms, which form a unique molecular structure. Each carbon atom is bonded to two fluorine atoms, creating a linear chain. This arrangement leads to a high degree of crystallinity and contributes to PTFE's low friction coefficient. Because of its strong C-F bonds, PTFE exhibits remarkable chemical inertness. This means it does not easily react with other chemicals, making it suitable for various industries, including chemical processing and pharmaceuticals.
- Key Aspects of Molecular Structure:
- High molecular weight contributes to durability.
- The presence of fluorine atoms imparts unique chemical resistance.
- Linear structure allows for flexibility and workability.
Thermal Stability
One of the standout features of PTFE is its exceptional thermal stability. It can withstand a wide range of temperatures, typically from -200°C to 260°C without significant degradation. This property is crucial in applications that involve varying thermal conditions. For instance, in industrial settings, PTFE can handle high heat without losing integrity, which extends the life and efficiency of equipment.
- Important Considerations for Thermal Stability:
- The high melting point allows for use in extreme conditions.
- Resistance to thermal degradation enables its use in applications such as aerospace and automotive engineering.
- It maintains performance under fluctuating temperatures, adding reliability.
"PTFE's ability to withstand extreme conditions without alteration is a primary reason for its widespread acceptance in industry."
"PTFE's ability to withstand extreme conditions without alteration is a primary reason for its widespread acceptance in industry."
Electrical Insulation Characteristics
PTFE is recognized for its excellent electrical insulation properties. Its low dielectric constant and high resistivity make it an ideal material for applications in the electronics industry, particularly in the manufacturing of printed circuit boards and connectors. It effectively prevents the flow of electricity, thereby reducing the risk of short circuits in sensitive electronic devices.
- Significant Features of Electrical Insulation Characteristics:
- High dielectric strength leads to reduced energy loss during transmission.
- Provides reliable insulation in harsh environments.
- Its stability under electrical stress enhances the longevity of electronic components.
In summary, the chemical properties of PTFE, particularly its molecular structure, thermal stability, and electrical insulation, play a pivotal role in its versatility across various fields. Understanding these aspects means better utilization of PTFE in innovative applications, driving advancements in technology and materials science.
Physical Properties of PTFE Foil
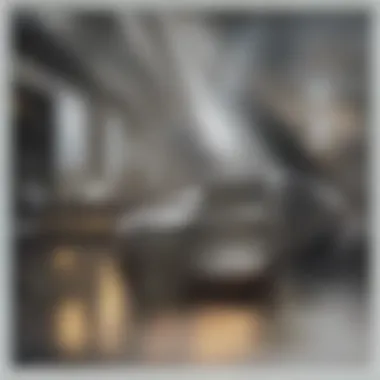
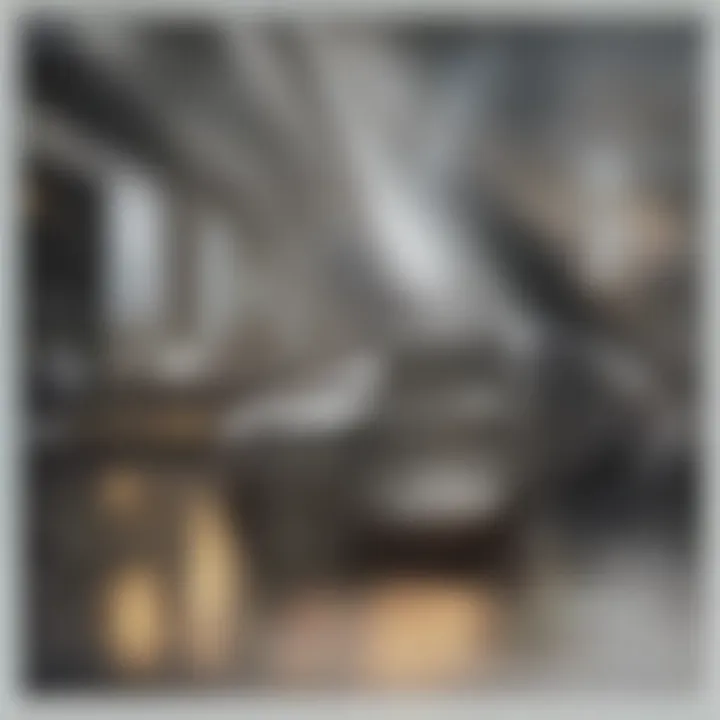
Understanding the physical properties of PTFE foil is crucial to appreciate its extensive applications and benefits across multiple industries. PTFE, or Polytetrafluoroethylene, is renowned for its exceptional characteristics that make it a preferred choice in various fields such as electronics, food processing, and chemical handling.
The physical properties of PTFE foil directly influence its usability and performance, providing insights into how it behaves under different environmental factors. This knowledge is essential for researchers and industry professionals seeking to optimize the use of PTFE in their specific applications.
Mechanical Strength
Mechanical strength refers to the ability of PTFE foil to withstand applied forces without breaking or deforming. PTFE exhibits remarkable tensile strength, which is a critical factor in its durability. This property ensures that PTFE can endure considerable stress, making it suitable for applications where structural integrity is essential.
The strength of PTFE is often complemented by its lightweight nature. Its combination of strength and low weight allows for applications in sectors where reducing total mass is a priority. For instance, in the aerospace industry, the mechanical strength of PTFE is advantageous as it contributes to lightweight construction materials without compromising on reliability.
Thus, the mechanical strength of PTFE foil plays a significant role in both performance and safety across various applications.
Flexibility and Workability
Flexibility is another vital characteristic of PTFE foil. Despite its strength, PTFE foil remains malleable and can be easily manipulated during manufacturing. This capability allows it to be processed into various forms such as sheets, rolls, and custom shapes according to specific requirements.
Workability is crucial for industries that demand precision in the fabrication of components. For instance, in the electronics sector, PTFE can be cut and formed into intricate designs required for printed circuit boards. Its flexibility also translates into adaptability, allowing for efficient integration into complex systems. Therefore, the flexibility and workability of PTFE foil significantly enhance its utility in numerous applications.
Chemical Resistance
One of the standout features of PTFE foil is its unparalleled chemical resistance. PTFE is highly resistant to a wide variety of chemicals, including acids, bases, and organic solvents. This characteristic ensures that PTFE foil can maintain its integrity and performance in harsh chemical environments, making it an ideal choice for the chemical processing and pharmaceutical industries.
Chemically aggressive substances can lead to significant material degradation in many other materials. In contrast, PTFE's stability under such conditions means that equipment linings, seals, and gaskets made from PTFE can prolong the lifespan of essential components. This level of resistance not only aids in reducing maintenance costs but also enhances safety by minimizing the risk of leaks and contamination.
"The remarkable chemical resistance of PTFE foil positions it as a critical material in environments where safety and durability are paramount."
"The remarkable chemical resistance of PTFE foil positions it as a critical material in environments where safety and durability are paramount."
Manufacturing Processes of PTFE Foil
The manufacturing processes of PTFE foil play a crucial role in determining its final properties and functional applications. These methods contribute significantly to the quality and performance of the material. Understanding these processes helps in enhancing product reliability and efficiency across various industries. Each manufacturing technique has its own set of benefits, considerations, and specific applications that can be utilized depending on the requirements of the end-use scenarios.
Extrusion Techniques
Extrusion is one of the primary methods used to manufacture PTFE foil. In this process, PTFE resin is heated until it reaches a semi-liquid state. Then, it is forced through a die to create a continuous sheet or foil. This technique allows for the production of uniform thickness and surface finish, which is critical for many applications.
Some advantages of extrusion techniques include:
- High Output: It can produce large volumes of PTFE foil efficiently.
- Customization: Different die designs can result in foils tailored to specific needs, such as varying thickness or width.
- Cost-Effectiveness: When scaled, extrusion can reduce the cost of production significantly compared to other methods.
However, there are challenges as well. Controlling the temperature and pressure is vital, as improper settings can affect the material properties. Slight variations can lead to defects in the foil, impacting its usability.
Calendering Methods
Calendering is another significant manufacturing process for PTFE foil. This involves passing PTFE through a series of rollers, which compress and shape the material into sheets of desired thickness. This method is known for producing foils with excellent surface smoothness and consistency.
Key benefits of calendering include:
- Control Over Thickness: The process provides precise control over the thickness of the finished product, which is essential for specific applications.
- Smooth Finish: Calendering results in a finely finished surface, ideal for applications in the electronics and medical fields.
- Enhanced Mechanical Properties: This process can enhance the mechanical strength of the PTFE foil due to the high pressure applied during shaping.
While calendering yields quality results, it typically produces smaller quantities compared to extrusion. Hence, the choice of method often depends on production volume requirements.
Gasketing and Die-Cutting Processes
In the production of PTFE foil, gasketing and die-cutting processes are critical for creating specific shapes and sizes that match the needs of various applications. These methods involve cutting PTFE foils to form gaskets, seals, or unique components that require precise dimensions.
Gasketing offers numerous advantages:
- Precision Shapes: The ability to produce intricate shapes with tight tolerances is essential in industries where sealing is important.
- Material Efficiency: Die-cutting minimizes waste by utilizing raw material more effectively.
Some challenges include:
- Complexity of Design: High complexity in designs may require advanced tooling and setup, leading to initial cost increases.
- Need for Testing: Finished products must be tested for fit and performance to ensure they meet the rigorous standards often demanded in industrial applications.
The appropriate manufacturing process for PTFE foil depends largely on the specifications and performance criteria required by the end product.
The appropriate manufacturing process for PTFE foil depends largely on the specifications and performance criteria required by the end product.
In summary, understanding the manufacturing processes of PTFE foil is fundamental for researchers, engineers, and industry professionals. Each method brings unique properties to the material, offering solutions tailored to diverse applications and challenges.
Applications of PTFE Foil
PTFE foil is widely recognized for its exceptional versatility and functionality across various industries. Each sector leverages the distinct properties of PTFE for specific applications, resulting in enhanced performance and durability. Understanding these applications is critical, as it highlights the material's relevance and its contributions to technological advancements.
Electronics Industry
Use in Printed Circuit Boards
PTFE foil plays a significant role in printed circuit boards (PCBs). Its low dielectric constant and low dissipation factor are key characteristics. These properties enhance signal integrity, making PTFE a preferred choice for high-frequency applications within electronics. The foil can withstand high temperatures and aggressive chemicals, extending the lifespan of the PCBs. However, the manufacturing process can be costlier compared to traditional materials, which might limit its adoption in less demanding applications.
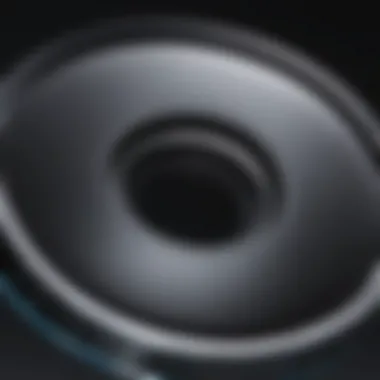
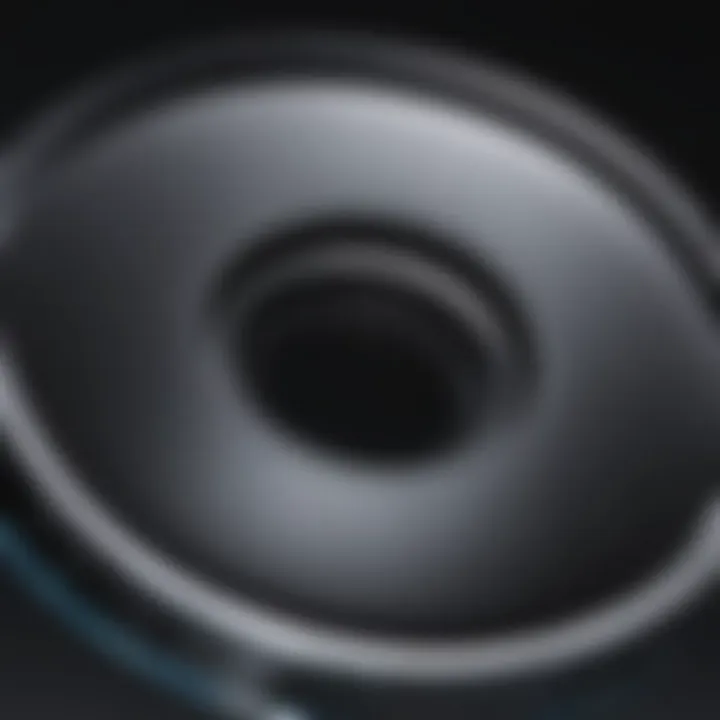
High-Frequency Applications
In high-frequency applications, PTFE foil is invaluable. Its ability to maintain low losses at high frequencies makes it suitable for microwave and RF circuits. This advantage boosts overall efficiency in communication systems. The material's thermal stability is another essential feature, ensuring reliable performance over time. On the downside, PTFE's mechanical properties might not be as strong as some alternatives, requiring careful consideration during product design.
Chemical Processing
Linings in Storage Tanks
PTFE foil is used for linings in storage tanks, particularly for corrosive substances. The non-reactive nature of PTFE ensures that it will not degrade even in the presence of harsh chemicals. This characteristic is crucial for maintaining tank integrity and preventing leaks. Utilizing PTFE foil in this capacity can drastically reduce maintenance costs over time. However, installation can be more complicated, requiring specialized skills.
Seals and Gaskets
Seals and gaskets made from PTFE foil offer excellent sealing capabilities in various environments. This material is resistant to extreme temperatures and a wide range of chemicals. Many industries favor PTFE seals due to their longevity and reliability, which can minimize downtime in operations. The only consideration is that, depending on the application, PTFE gaskets may require additional support to handle high pressures.
Food Industry
Non-Stick Surfaces
In the food industry, PTFE foil is commonly used for non-stick surface applications. The material’s inherent non-stick properties simplify food preparation and cleaning processes. Restaurants and food manufacturers benefit from efficiency and reduced waste. However, concerns about the safety of certain non-stick coatings in extreme heat conditions must be addressed, leading some manufacturers to select alternative non-stick solutions.
Food Processing Equipment
PTFE foil is increasingly employed in food processing equipment. It makes for easy cleaning and compliance with food safety regulations due to its non-porous surface. Additionally, the durability of PTFE reduces equipment wear and tear, ensuring longer service life. Nevertheless, the initial costs may be higher than conventional materials, prompting some businesses to evaluate their return on investment carefully.
Medical Applications
Biocompatibility
Biocompatibility is a defining aspect of PTFE foil in medical applications. Its chemical inertness ensures that it does not react with body fluids or tissues. This property is vital for devices that require implantation or prolonged contact with biological environments. PTFE's reliability can be critical in advancing medical technology. The challenge remains in balancing costs and performance, especially in small-scale production.
Medical Device Manufacturing
Medical device manufacturing often utilizes PTFE foil for its unique characteristics. Its flexibility and durability allow for the production of intricate designs required in advanced medical devices. PTFE's compatibility with sterilization methods is another advantage, ensuring devices remain safe for use. However, adherence to strict regulatory standards can complicate the manufacturing process.
PTFE foil continues to be a choice material across diverse sectors due to its unique properties, significantly impacting various applications.
PTFE foil continues to be a choice material across diverse sectors due to its unique properties, significantly impacting various applications.
Advantages of Using PTFE Foil
PTFE foil offers numerous benefits that make it a preferred material in various industries. Its unique properties result in practical advantages that enhance the performance of products where it is applied. Understanding these benefits is crucial for engineers, researchers, and industry professionals, as it allows for informed decisions related to material selection. Here, we explore the key advantages of using PTFE foil: durability, cost-effectiveness, and its compatibility with a wide range of temperatures.
Durability and Longevity
Durability is one of the primary advantages of PTFE foil. This material exhibits high resistance to wear and tear, which contributes to its long lifespan in applications. PTFE foil is not easily damaged by chemicals, moisture, or extreme temperatures. These characteristics ensure that equipment and products made from PTFE foil will last longer and require less frequent replacements or repairs.
Even in harsh environments, PTFE foil maintains its structural integrity. For instance, it can withstand exposure to corrosive substances found in chemical processing facilities without deteriorating. This feature is particularly valuable in industries such as pharmaceuticals and food processing where hygiene and material longevity are crucial.
Moreover, the durability of PTFE foil leads to less waste, which aligns with sustainable practices. Fewer replacements mean reduced resource consumption, making PTFE an environmentally friendly choice over time.
Cost-Effectiveness
Cost-effectiveness is another significant advantage of PTFE foil. Though the initial investment might seem higher than alternative materials, the lifecycle costs often favor PTFE. First, its durability implies longer use, which translates to fewer replacement costs.
Additionally, PTFE foil's resistance to chemical damage reduces maintenance efforts and associated expenses. In the long run, industries can save substantially on repairs and replacements.
The versatility of PTFE also adds to its cost-effectiveness. It can be used across various sectors, from electronic manufacturing to food processing. This multi-functional nature reduces the need to source multiple materials for different applications, streamlining purchasing and inventory processes. Furthermore, lower energy costs associated with manufacturing and processing PTFE can contribute to overall savings.
Wide Temperature Range Compatibility
PTFE foil is known for its impressive compatibility with a wide range of temperatures. It can perform effectively in temperatures ranging from -200°C to +260°C without losing its properties. This feature makes it especially valuable in applications where temperature fluctuations occur frequently.
Many other materials fail in extreme temperatures, leading to malfunctions or failures. In contrast, PTFE foil maintains stability, which is essential for ensuring the reliability of equipment in diverse conditions. For instance, in aerospace applications, where materials encounter extreme environments, PTFE foil guarantees performance consistency.
In summary, the ability of PTFE foil to function across such a broad temperature range opens doors to applications in various critical fields, including automotive, energy, and construction.
"The unique properties of PTFE foil empower industries to enhance performance while minimizing operational costs."
"The unique properties of PTFE foil empower industries to enhance performance while minimizing operational costs."
These advantages position PTFE foil as a strategic choice for many modern applications, making it a critical material for innovation and efficiency in multiple sectors.
Challenges in the PTFE Foil Market
The market for PTFE foil is growing, but it faces varios challenges that affect its reach and sustainability. Understanding these challenges is critical for industry professionals and researchers to move forward effectively. Addressing these issues not only helps in the advancement of PTFE technology but is also essential for maintaining consumer trust and regulatory compliance. The sections below expand on the major challenges, namely, environmental concerns, competition from alternative materials, and regulatory compliance.
Environmental Concerns
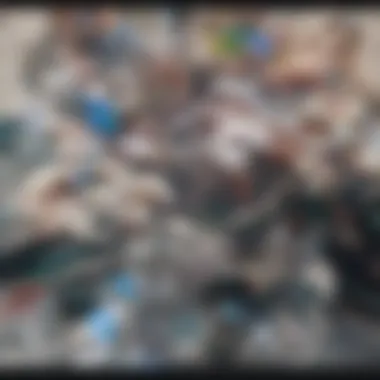
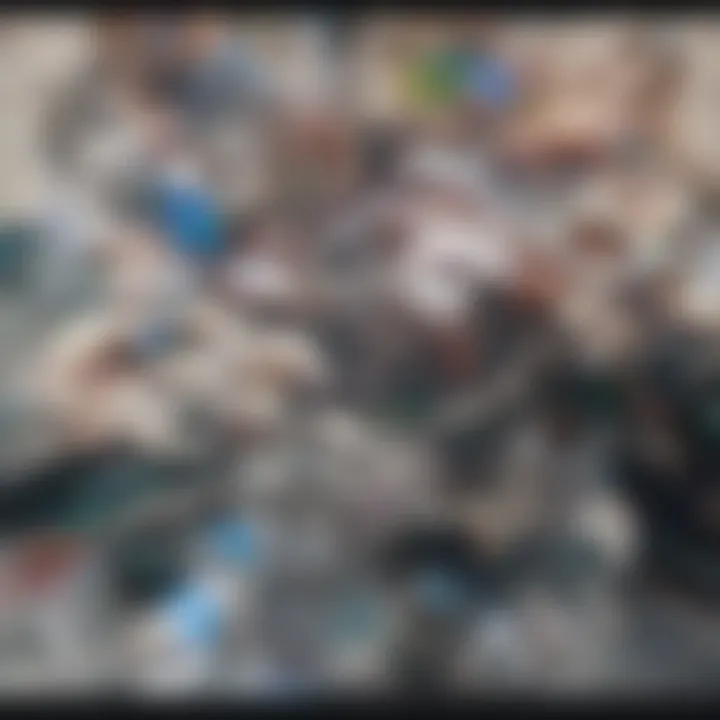
Environmental issues are at the forefront of challenges affecting the PTFE foil market. The production and disposal of PTFE materials can result in pollution and waste. The polymer itself is known to be chemically resistant, making it durable but also challenging to recycle. Consequently, the accumulation of PTFE in landfills poses long-term environmental risks. Notably, the manufacturing process often involves the use of toxic substances, which raises additional ecological concerns.
To combat these challenges, the industry is exploring greener manufacturing techniques and sustainable methods for end-of-life management. Innovations include developing alternative materials that can have a lower environmental footprint while still providing similar properties to PTFE. Additionally, consumers are becoming more aware of sustainability, which puts pressure on manufacturers to adopt eco-friendlier practices.
Competition from Alternative Materials
Another significant challenge is the competition from alternative materials. Other types of polymers and composites may offer comparable properties, such as high temperature resistance and chemical safety, but often at a lower cost. Materials like silicone, polypropylene, and engineering plastics are increasingly common in various applications. Their benefits include ease of availability and lower production costs, making them attractive options for manufacturers.
The rise of these alternatives leads to increased market pressure for PTFE foil producers. The industry must focus on innovation and differentiation, highlighting unique advantages of PTFE foil. Developing hybrid materials or composite solutions can be a way to thrive in a competitive landscape.
Regulatory Compliance
Navigating the labyrinth of regulatory requirements is another challenge. The use of PTFE is subject to multiple regulations, especially in industries like food processing, healthcare, and electronics. Compliance with local and international standards is essential for maintaining market access and consumer safety. These regulations dictate not only production practices but also testing and certification processes.
Manufacturers must stay informed about changes in legislation and adapt their practices accordingly. Failure to comply can result in significant penalties and loss of credibility. Therefore, investing in quality assurance and regulatory planning becomes vital. This also entails fostering open communication with regulatory bodies to ensure that the evolving standards are met.
Addressing the challenges in the PTFE foil market requires a proactive approach. By investing in sustainable practices and staying compliant with regulations, companies can safeguard their position and contribute positively to the environment.
Addressing the challenges in the PTFE foil market requires a proactive approach. By investing in sustainable practices and staying compliant with regulations, companies can safeguard their position and contribute positively to the environment.
Technological Innovations in PTFE Foil Production
Technological advancements play a vital role in improving the production of PTFE foil. These innovations not only enhance the quality of the product but also increase its efficiency and application range. As industries evolve, the need for better, more sustainable materials grows. Notably, PTFE foil benefits from state-of-the-art techniques that respond to this demand, allowing for its continued prevalence across diverse sectors.
Advanced Fabrication Techniques
The landscape of PTFE foil production is notably altered by advanced fabrication techniques. Methods such as 3D printing and laser cutting have emerged, enabling more complex shapes and sizes that were previously difficult to achieve. 3D printing specifically introduces a level of customization and flexibility in design, allowing manufacturers to create components tailored to specific industrial needs. This technology can also reduce waste, as it optimizes material usage during production.
Moreover, extrusion methods have improved, facilitating the production of films with even thickness and uniformity. This consistency is crucial in ensuring that the performance characteristics of PTFE remain reliable during their application.
Sustainability Innovations
Sustainability in manufacturing is another area where technological innovations are making a significant impact. The industry is gradually moving towards eco-friendlier methods of producing PTFE foil. This includes the use of bio-based feedstocks that are more renewable, reducing reliance on fossil fuels. Furthermore, efforts to minimize waste and energy consumption are seen through improved recycling methods and energy recovery systems.
Additionally, companies are increasingly exploring closed-loop production systems. This method minimizes waste by reusing production scrap and employing more efficient processes to recycle used PTFE products. The integration of these sustainable practices is essential for meeting regulatory standards and addressing environmental concerns, making them an integral part of the future of PTFE foil production.
Smart Materials Integration
The integration of smart materials into PTFE foil production is pushing the boundaries of functionality. Smart materials can respond to environmental changes, like temperature and pressure variations, which expands the application potential of PTFE foil. For instance, incorporating sensors into PTFE films can create applications in health monitoring systems and industrial processes where constant monitoring is critical.
Another promising area is the development of self-healing PTFE films. These materials can repair damages autonomously, effectively extending their lifespan and maintaining performance. This innovation presents a significant advantage in sectors such as aerospace and automotive, where material reliability is paramount.
Future Prospects of PTFE Foil
The future of PTFE foil holds significant promise and complexity within various industries. This versatile material, known for its unique features, is poised to adapt and evolve in response to changing market demands and technological advancements. Understanding these elements is crucial for both researchers and industry professionals, as it informs future developments and innovations.
One of the foremost considerations in the future of PTFE foil is its role within sustainable practices. As industries increasingly focus on eco-friendliness, manufacturers are exploring ways to reduce the environmental impact of PTFE. This may include the development of recyclable PTFE options or the implementation of greener manufacturing methods. Engaging in sustainable practices not only enhances brand reputation but also complies with stricter regulations on environmental safety.
Market Trends
Market analyses indicate a growing demand for PTFE foil across various sectors, including electronics, medical, and food industries. The electronics sector, in particular, is anticipated to drive significant growth due to the increasing complexity of devices requiring high-performance insulation. Innovations in microelectronics demand materials like PTFE foil that can maintain integrity under extreme conditions, giving them a competitive edge in product utilization.
Similarly, the medical field is evolving, with PTFE foil essential for creating biocompatible materials. The increasing volume of medical equipment and devices needing high-quality seals and insulations enhances the market's potential.
Key market trends include:
- Sustainable product development
- Growing sophistication of technology
- Adoption in developing economies
Research Directions
The academic and industrial research surrounding PTFE foil continues to flourish, focusing on several fronts. Increasing emphasis on advancements in material science is driving the exploration of new formulations and applications. Researchers are investigating the integration of nanotechnology to improve the physical and chemical properties of PTFE foil further. This includes enhancing thermal stability and mechanical strength, which can open doors to new applications.
Moreover, studies examining the compatibility of PTFE with other materials also hold promise. Such interdisciplinary research can lead to the creation of composite materials that harness the beneficial properties of PTFE while overcoming its limitations.
Future research directions may encompass:
- Development of composite materials
- Innovations in recycling processes
- Integration of smart sensors
The interplay between innovation and sustainability will undeniably position PTFE foil as a material of choice in the coming decades, shaping its applications and market presence.
The interplay between innovation and sustainability will undeniably position PTFE foil as a material of choice in the coming decades, shaping its applications and market presence.
Closure
The importance of concluding our discussion on PTFE foil cannot be overstated. This article highlights the necessity of understanding both the properties and the applications of this remarkable material. PTFE foil, with its unique chemical composition and outstanding physical properties, finds extensive uses across various industries. Its contributions range from enhancing electronic devices to ensuring safety in food processing. As we look toward future innovations, it is crucial to consider both the advancements and the challenges that lie ahead for PTFE foil. This discussion synthesizes not only theoretical insights but also practical implications that can guide researchers and industry professionals.
Summary of Key Points
In this article, we examined several critical aspects of PTFE foil.
- Definition and Composition: PTFE is a fluoropolymer known for its high resistance to chemicals and thermal stability.
- Chemical and Physical Properties: Its unique molecular structure grants it mechanical strength and flexibility, essential for various applications.
- Manufacturing Processes: PTFE foil can be produced through methods such as extrusion, calendering, and die-cutting, each influencing its properties.
- Applications: From electronics to medical devices, the versatility of PTFE foil makes it integral in numerous sectors.
- Advantages: Durability, longevity, and cost-effectiveness are notable benefits that support its continued use.
- Challenges: Environmental concerns and industry competition pose significant challenges in the market.
- Technological Innovations: Advances in fabrication techniques and sustainability practices are crucial for future production.
- Future Prospects: Market trends and ongoing research point towards a promising future for PTFE foil.
The Future of PTFE Foil in Science and Industry
Looking ahead, PTFE foil is poised for further innovations that will change its functionalities and applications. Emerging technologies may improve manufacturing processes, reducing costs and environmental impacts. Moreover, as industries evolve, the demand for materials with better heat resistance and chemical durability will increase. Researchers are likely to explore integrating smart materials into PTFE foil, enhancing its applications further.