The Fascinating Science of Uni-Directional Carbon Fiber
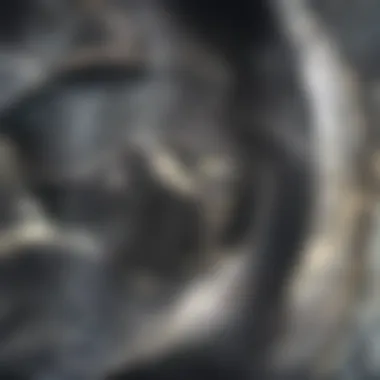
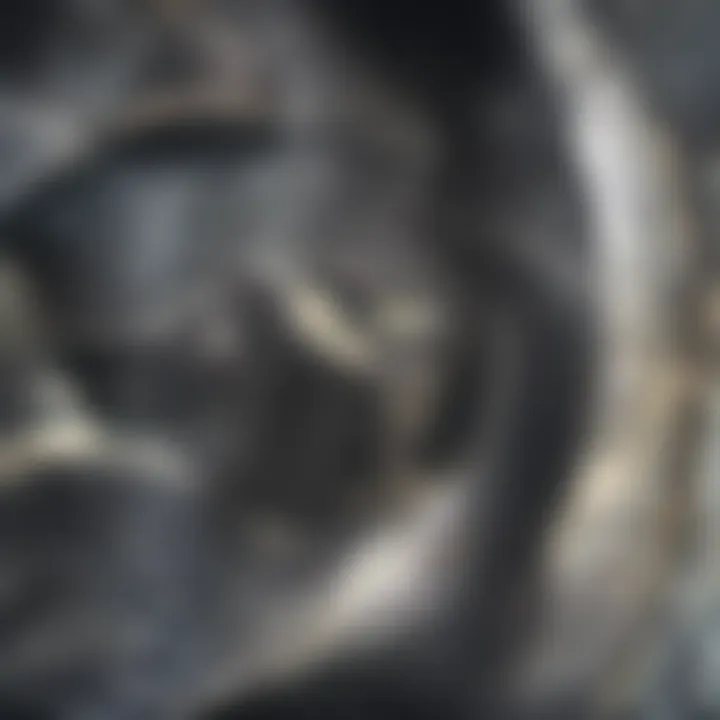
Article Overview
Purpose of the Article
The purpose of this article is to provide a comprehensive analysis of uni-directional carbon fiber, a material that has gained prominence in various fields due to its distinctive properties. It aims to detail the material's advantages and disadvantages, its production techniques, and its diverse applications in industries ranging from aerospace to biomedical devices. By articulating the critical characteristics and implications of this material, the article serves as a resource for scientists, engineers, and other professionals who seek a deeper understanding of carbon fiber technology.
Relevance to Multiple Disciplines
Uni-directional carbon fiber is not confined to a single domain; its implications touch on multiple disciplines including materials science, engineering, and even sports technology. Its lightweight nature and superior strength make it essential in high-performance applications. In research, the exploration of its properties assists in material innovation, leading to advancements in product design and engineering solutions. This cross-disciplinary relevance underscores the necessity of understanding the nuances of uni-directional carbon fiber in driving future technological progress.
Research Background
Historical Context
The journey of carbon fiber began in the late 1950s. Initial developments laid groundwork for the production of high-performance fiber. Unlike conventional textiles, carbon fiber emerged as a material that combines high tensile strength with reduced weight. Its evolution over the decades has led to various forms, with uni-directional carbon fiber taking center stage in modern applications. The ability to tailor mechanical properties has transformed industries such as aerospace and automotive, enabling the creation of lighter and stronger structures.
Key Concepts and Definitions
Understanding uni-directional carbon fiber requires familiarity with several key concepts:
- Uni-Directional Structure: This refers to fibers that are oriented in a single direction, which enhances tensile strength along that axis. The material’s performance is largely determined by this alignment.
- Tensile Strength: This is the resistance of a material to breaking under tension. Uni-directional carbon fiber boasts high tensile strength, critical for load-bearing applications.
- Resin Matrix: Often used in conjunction with carbon fibers, the resin helps to bind the fibers together, providing additional structural integrity.
"The unique orientation of fibers in uni-directional carbon fiber enables specific performance characteristics that cater to high-stress applications, making it a valuable material in engineering and design."
"The unique orientation of fibers in uni-directional carbon fiber enables specific performance characteristics that cater to high-stress applications, making it a valuable material in engineering and design."
These definitions and concepts provide foundational knowledge essential for a deeper dive into the subject, enabling readers to engage with the material properties of uni-directional carbon fiber in various contexts.
Preface to Uni-Directional Carbon Fiber
Uni-directional carbon fiber represents a significant advancement in material science. This material is notable for its impressive strength-to-weight ratio, making it a preferred choice in industries where performance and efficiency are critical. Understanding uni-directional carbon fiber is essential for students, researchers, and professionals who seek to innovate or enhance products utilizing this technology. The unique characteristics of this material not only offer a competitive edge in production but also inspire ongoing research and development.
Definition and Characteristics
Uni-directional carbon fiber consists of fibers aligned in a single direction, enhancing strength and performance along that axis. Each fiber is thin, often less than 15 microns in diameter, which contributes to its lightweight properties. When combined with a polymer matrix, such as epoxy, it forms a composite material with excellent rigidity and reduced weight. This structure leads to significant advantages in various applications, especially those requiring precise load-bearing capabilities. It is also highly resistant to temperature fluctuations and corrosion, underscoring its functional durability.
Key characteristics of uni-directional carbon fiber include:
- High tensile strength which makes it effective under stress.
- Low density, leading to lighter components without sacrificing performance.
- Excellent stiffness-to-weight ratio which allows for thinner designs without compromise.
Historical Context and Development
The development of uni-directional carbon fiber is rooted in advancements made during the mid-twentieth century when carbon fibers began to emerge as an alternative to traditional materials. Initially, these fibers were used primarily in aerospace and military applications due to their high cost and specialized nature. However, as production methods improved over the years, the use of uni-directional carbon fiber expanded significantly.
By the late 1970s, researchers recognized the potential of uni-directional structures in enhancing performance metrics of various products. Today, these fibers are utilized in a myriad of fields, from sports equipment to automotive components. The historical transition from niche applications to mainstream adoption reflects ongoing innovations in manufacturing processes, enabling wider accessibility and adaptability in product designs.
Chemical Composition of Uni-Directional Carbon Fiber
The chemical composition of uni-directional carbon fiber plays a crucial role in determining its unique properties and applications. Understanding the key components and materials involved provides valuable insights into why this material is favored in various high-performance industries.
Polymer Matrix Materials
Uni-directional carbon fiber is typically combined with a polymer matrix to enhance its mechanical properties and overall performance. The polymer matrix serves multiple roles, including bonding the fibers together, transferring loads, and protecting the fibers from environmental factors. Common types of polymer matrices used include epoxy, polyamide, and polyester.
Epoxy resins, in particular, are popular due to their superior adhesion and mechanical strength. They exhibit low shrinkage upon curing, which helps maintain the structural integrity of the composite. The choice of polymer matrix directly affects the thermal stability, chemical resistance, and ductility of the final product. In the aerospace sector, where performance standards are high, the right polymer matrix is essential for ensuring safety and longevity.
Carbon Fibers Properties
The properties of carbon fibers themselves are fundamentally important to the performance of uni-directional carbon fiber composites. Carbon fibers are characterized by their high tensile strength, low weight, and excellent stiffness. Typically measured by their tensile modulus and strength, carbon fibers can withstand significant amounts of stress without permanent deformation.
Some notable properties include:
- High Strength-to-Weight Ratio: This makes carbon fibers ideal for applications where minimizing weight is critical, like in aerospace.
- Thermal Conductivity: Compared to many other materials, carbon fibers conduct heat well, which can be advantageous in applications requiring heat dissipation.
- Corrosion Resistance: Carbon fibers resist chemical degradation, making them suitable for harsh environments.
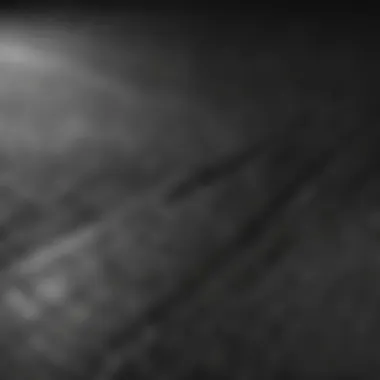
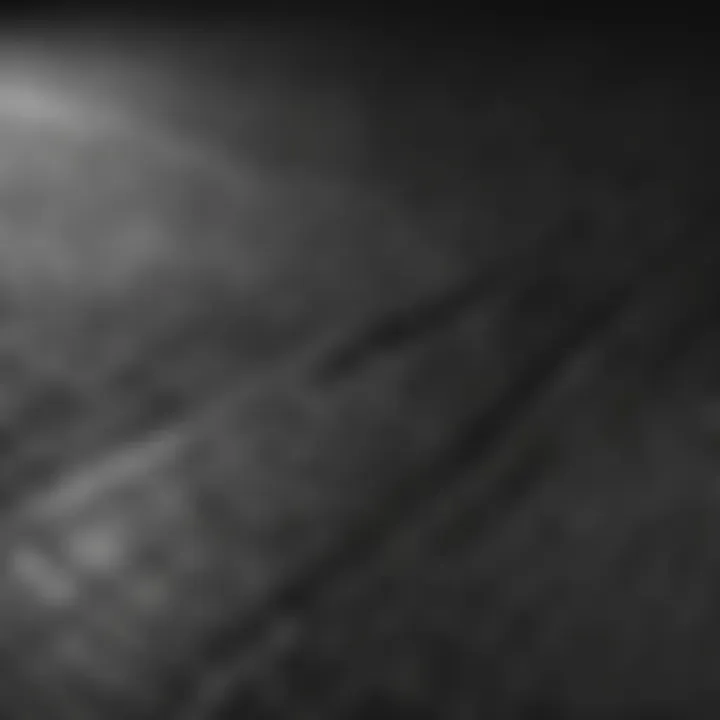
These attributes make uni-directional carbon fiber appealing for use in various industries, including automotive and sports equipment manufacturing. Each application capitalizes on the fundamental nature of the fibers, emphasizing the importance of their composition and how they are processed together with polymer matrices.
"The synergy between the polymer matrix and carbon fibers ultimately determines the performance and reliability of the composite material."
"The synergy between the polymer matrix and carbon fibers ultimately determines the performance and reliability of the composite material."
This understanding of the chemical composition lays a foundation for deeper exploration into production methods, applications, and challenges associated with uni-directional carbon fiber. Each element within the composition contributes significantly to the material’s function and suitability across industries.
Production Methods for Uni-Directional Carbon Fiber
The production methods for uni-directional carbon fiber are vital for understanding its application and effectiveness in various fields. These methods influence the quality, performance, and adaptability of the final product. The choice of manufacturing technique determines not only the characteristics of the fibers but also their suitability for diverse applications, from aerospace to sports equipment. Therefore, a deep dive into manufacturing techniques and innovations is essential for researchers and professionals working with this material.
Overview of Manufacturing Techniques
The manufacturing of uni-directional carbon fiber typically involves several key techniques, each with its own unique advantages and challenges. The primary methods include:
- Filament Winding: This technique involves winding continuous strands of carbon fibers around a mold. It provides excellent strength and allows for complex geometries. This method is widely used in pressure vessels and aerospace components.
- Pultrusion: This method pulls fibers through a resin bath and then through a heated die to create a solid shape. Pultrusion is efficient for producing long, continuous sections and offers good quality control. It is commonly used for structural components in construction and automotive sectors.
- Lay-Up Process: In this manual technique, layers of carbon fiber sheets are laid in a mold and soaked with resin. Though labor-intensive, it allows for customization and intricate designs. This method is often used in the fabrication of sporting goods and specialized parts in aerospace.
- RTM (Resin Transfer Molding): This involves injecting resin into a closed mold containing the carbon fiber. It provides a high level of precision and reduces waste, making it favorable for large parts used in automotive production.
Each manufacturing technique has distinct process parameters that affect the final properties of the uni-directional carbon fiber, such as tensile strength and stiffness. The choice between these methods often depends on the desired specifications of the end product and cost considerations.
Key Innovations in Production
Recent innovations in the production of uni-directional carbon fiber focus on enhancing efficiency and minimizing environmental impact. Some of these advancements include:
- Automated Manufacturing Processes: Automation reduces labor costs and increases consistency in production. Automated systems can optimize fiber placement and resin application, leading to improved mechanical properties.
- Recyclable Fiber Technologies: As sustainability becomes a priority, the development of recyclable carbon fibers is emerging. Innovations in this area are aimed at reducing waste associated with production and end-of-life disposal, promoting a circular economy.
- Enhanced Resin Systems: Researchers are developing new resin formulations that improve bonding with carbon fibers while being more resistant to environmental factors. This can result in superior performance in various applications.
- 3D Printing with Carbon Filament: 3D printing technology is evolving to incorporate carbon fibers, enabling rapid prototyping and custom parts production. This method allows for complex designs that were previously difficult or impossible to achieve.
"The advancements in manufacturing not only improve the performance of carbon fibers but also address the urgency of sustainability in material production."
"The advancements in manufacturing not only improve the performance of carbon fibers but also address the urgency of sustainability in material production."
These innovations collectively indicate a promising future for uni-directional carbon fiber, emphasizing performance improvements and environmental consciousness. Understanding these methods can help professionals make informed decisions regarding material selection and application.
Material Properties of Uni-Directional Carbon Fiber
Understanding the material properties of uni-directional carbon fiber is crucial. These properties determine how this composite material performs in various applications. The focus on strength, stiffness, durability, and resistance to fatigue provides insights into its overall effectiveness in real-world scenarios.
Strength and Stiffness Analysis
The strength and stiffness of uni-directional carbon fiber are among its most notable characteristics. Strength refers to the ability of a material to withstand an applied load without failure. Stiffness, on the other hand, indicates how much a material deforms under stress.
Uni-directional carbon fiber showcases a remarkable strength-to-weight ratio. This attribute makes it highly desirable in applications where weight reduction is critical. For instance, in aerospace engineering, every gram saved can result in fuel efficiency gains.
The stiffness of this material is predominantly influenced by the alignment of the fibers. In uni-directional carbon fiber, the fibers are aligned in one direction, which enhances stiffness along that specific axis. This property makes it effective in applications requiring bending resistance. Strong, stiff composites can lead to more efficient designs and better performance in engineering structures.
"The advanced properties of uni-directional carbon fiber enable innovations across industries, pushing the boundaries of design and application."
"The advanced properties of uni-directional carbon fiber enable innovations across industries, pushing the boundaries of design and application."
Durability and Fatigue Resistance
Durability plays a significant role in the performance of uni-directional carbon fiber. This material is known for its resistance to environmental factors, including moisture and UV exposure. Such durability ensures longevity in practical applications, making it a cost-effective choice over time, despite a higher initial investment.
Fatigue resistance is equally important. It relates to how well a material can endure cyclic loads without failing. Uni-directional carbon fiber exhibits impressive fatigue resistance, meaning it can sustain repeated stress over an extended period. This is particularly relevant in industries such as automotive and aerospace, where components experience constant loading and unloading cycles throughout their service life.
As a summary, strength, stiffness, durability, and fatigue resistance make uni-directional carbon fiber a leading contender in advanced engineering materials. Understanding these properties is essential for scientists and engineers designing components that can withstand demanding environments.
Applications of Uni-Directional Carbon Fiber
Uni-directional carbon fiber has become a crucial material in various industries due to its unique properties. Its applications span across different sectors such as aerospace, automotive, and sports equipment manufacturing. Each application leverages the material’s high strength-to-weight ratio and other beneficial characteristics. Understanding these applications not only emphasizes the material's versatility but also highlights its impact on technology and innovation.
Using uni-directional carbon fiber can lead to significant improvements in performance and durability. As we explore its applications, it is clear that this material is poised to redefine standards in engineering and design.
Aerospace Industry Implementation
The aerospace industry is one of the largest consumers of uni-directional carbon fiber. Its primary role is to enhance the performance and efficiency of aircraft. By incorporating this material into aircraft structures, manufacturers achieve significant weight reductions without compromising strength. For example, the Boeing 787 Dreamliner utilizes uni-directional carbon fiber in its wings and fuselage. This contributes to increased fuel efficiency and reduced operational costs.
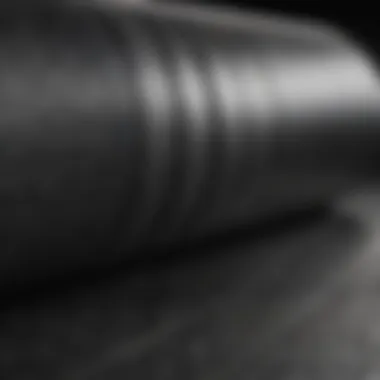
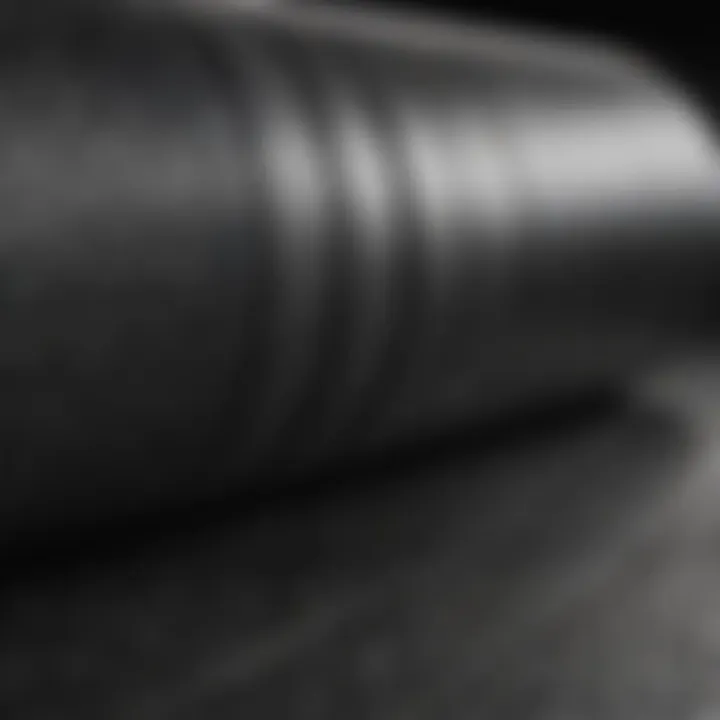
The ability to mold uni-directional carbon fiber into complex shapes allows for aerodynamic designs. This is essential for maintaining performance at high altitudes and speeds. Additionally, the material's resistance to corrosion and fatigue ensures long-term reliability, crucial for safety in aviation.
Automotive Applications
In the automotive sector, uni-directional carbon fiber finds numerous applications, enhancing both performance and safety. Car manufacturers use it extensively in high-performance vehicles, particularly in racing and luxury cars. The lightweight nature of uni-directional carbon fiber leads to better speed and fuel economy.
Moreover, its application in components such as chassis and body panels results in vehicles that are not only lighter but also more rigid. Enhanced rigidity through uni-directional carbon fiber helps improve handling and stability at high speeds. Brands like Lamborghini and McLaren use this material in their cars to optimize performance.
Sports Equipment Manufacturing
Sports equipment is another significant area benefiting from uni-directional carbon fiber. The material is favored in high-end products such as bicycles, tennis rackets, and golf clubs due to its lightweight and robust characteristics.
For instance, top-tier racing bicycles often incorporate uni-directional carbon fiber frames, allowing cyclists to achieve higher speeds with less effort. In tennis, rackets made from this material provide players with more power without sacrificing control. This is due to the ability to tune the stiffness and properties of the fiber during manufacturing.
Furthermore, sports equipment made with uni-directional carbon fiber typically lasts longer and withstands greater impacts, ensuring athletes can depend on their gear under extreme conditions.
In summary, the applications of uni-directional carbon fiber illustrate its remarkable versatility and importance across various industries. From aerospace to automotive and sports, the material not only improves functionality and performance but also paves the way for future advancements in design and engineering.
Advantages of Uni-Directional Carbon Fiber
Uni-directional carbon fiber is noted for several advantages that set it apart from other materials. These advantages are crucial in assessing its application across various industries. Understanding these benefits helps in determining the future relevance and capability of uni-directional carbon fiber.
Weight to Strength Ratio
One of the most significant advantages of uni-directional carbon fiber is its exceptional weight to strength ratio. The structure of this material allows it to maintain high strength while being remarkably lightweight. When compared to traditional materials, this ratio becomes particularly evident. For instance, in the aerospace and automotive industries where reducing weight is essential, uni-directional carbon fiber provides a competitive edge. It enables engineers to design components that do not compromise on safety while achieving performance goals.
The low density of carbon fiber means that large structures can be constructed without excessive mass. Furthermore, the directional alignment of fibers plays a role in enhancing tensile strength along the fiber orientation. This means that even lightweight structures can endure significant forces without structural failure.
"The weight to strength ratio is a critical factor in industries where performance is paramount."
"The weight to strength ratio is a critical factor in industries where performance is paramount."
A few key points regarding weight to strength ratio include:
- Enhanced Performance: Reduced weight contributes to faster speeds and improved fuel efficiency in vehicles.
- Design Flexibility: Engineers have more freedom to create complex shapes without additional weight concerns.
- Increased Payload: In aerospace applications, light components can lead to higher payload capacity without affecting overall weight limits.
Corrosion and Wear Resistance
Another notable advantage is the corrosion and wear resistance exhibited by uni-directional carbon fiber. Unlike metals, which can degrade over time due to rust and environmental exposure, carbon fiber withstands harsh conditions effectively. This characteristic makes it particularly valuable in industries like marine applications, where components face moisture and salt exposure.
The inherent properties of the polymer matrix also enhance the durability of the material. This means components made from uni-directional carbon fiber require less frequent replacement, thereby reducing long-term maintenance costs.
Moreover, wear resistance is essential in high-friction applications such as bearings and automotive components. The stability of carbon fiber under mechanical stress contributes to longer lifecycle and reliability.
In summary, the corrosion and wear resistance leads to significant operational advantages:
- Reduced Maintenance Costs: Less frequent replacements save money and resources.
- Longevity: Components can perform for extended periods, even in adverse environments.
- Consistent Performance: Reliable outcomes due to uniform resistance against degradation.
These advantages underline the potential of uni-directional carbon fiber as a go-to material for advanced applications across different industries.
Challenges and Limitations of Uni-Directional Carbon Fiber
The adoption of uni-directional carbon fiber in various industries underscores its many benefits, yet challenges exist that present significant hindrances. Understanding these challenges is crucial for engineers, researchers, and those in related fields. This section will shed light on two primary challenges: the cost of production and the issues related to parameter consistency and variability.
Cost of Production
One of the primary barriers to broader utilization of uni-directional carbon fiber is its production cost. The materials and complex processes involved necessitate a substantial investment, making it less accessible for certain applications.
- Raw Materials: The precursor materials, such as polyacrylonitrile, are not only expensive but also susceptible to market fluctuations. High-quality fibers require specificity in sourcing, increasing costs.
- Manufacturing Processes: Techniques like prepregging and autoclave curing involve precise conditions that can be energy-intensive. This complexity often results in increased labor and operational costs.
- Economies of Scale: While industrial production can affect costs positively, achieving the necessary scale remains a challenge for many manufacturers, particularly small to medium enterprises.
The cost factor impacts decision-making in both existing and prospective markets. It often leads to the choice of alternative materials, affecting the overall adoption rate of carbon fiber technologies.
Parameter Consistency and Variability
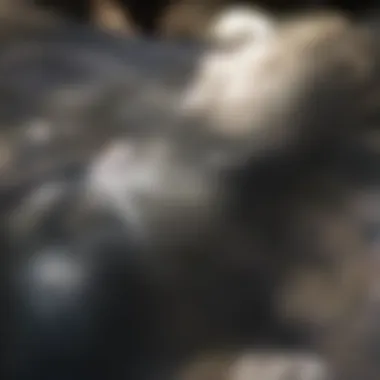
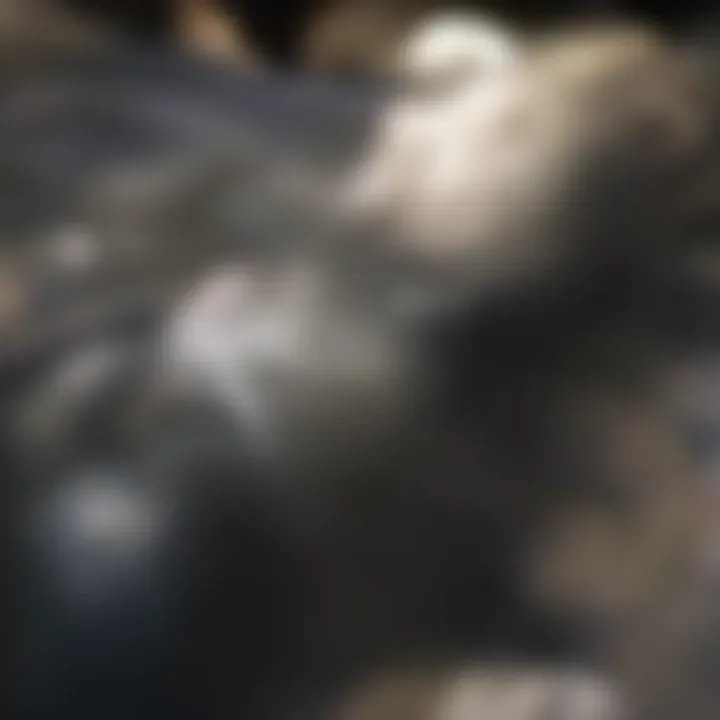
Another significant limitation in the use of uni-directional carbon fiber is achieving consistent parameters during the manufacturing process. Variability can occur during multiple stages of production, leading to performance inconsistencies in the final product.
- Process Control: Maintaining stability in temperatures, pressure, and time can be difficult. Any deviation can drastically affect the fiber's properties, including strength and flexibility.
- Material Properties: Inconsistencies in thickness or weave pattern can compromise the quality of materials used. This variability can manifest as differences in tensile strength or other mechanical properties.
- Quality Assurance: Rigorous testing is essential to ensure product quality. Each batch might demand different testing, leading to time delays and additional costs.
"Without addressing parameter consistency, industries relying on uni-directional carbon fiber risk significant performance failures."
"Without addressing parameter consistency, industries relying on uni-directional carbon fiber risk significant performance failures."
In summary, while uni-directional carbon fiber presents transformative possibilities, these challenges must be navigated for its optimal use. Cost and variability are at the forefront of discussions surrounding its integration into more sectors. Attention to these elements is essential for engineers and decision-makers aiming for the successful application of this advanced material.
Current Research Trends in Uni-Directional Carbon Fiber
Research in uni-directional carbon fiber is evolving rapidly. Scientists and engineers are focusing on new methodologies to optimize its properties and address existing challenges. As industries demand lighter, stronger, and more sustainable materials, the exploration of innovative techniques becomes crucial. This section explores recent advancements in nanotechnology and sustainable manufacturing, emphasizing their potential impact on the future of uni-directional carbon fiber.
Nanotechnology Innovations
Nanotechnology plays a significant role in enhancing the properties of uni-directional carbon fiber. It involves manipulating materials at the nanoscale. One of the key advancements is the integration of nanoparticles into the fiber structure, which can improve strength and functionality. For example, incorporating carbon nanotubes enhances the tensile strength significantly while maintaining lightweight properties. This can lead to applications in advanced industries like aerospace, where performance and weight matter critically.
Research also indicates that nano-coatings can provide enhanced barrier properties, improving resistance to moisture and chemical degradation. This advancement not only extends the lifespan of carbon fiber products but also ensures better performance in harsh environments, which is essential for sectors like automotive and construction.
"The integration of nanotechnology in uni-directional carbon fiber is set to revolutionize its applications, making it a frontrunner in advanced materials science."
"The integration of nanotechnology in uni-directional carbon fiber is set to revolutionize its applications, making it a frontrunner in advanced materials science."
Sustainable Manufacturing Approaches
In response to the growing concerns about environmental sustainability, researchers are examining sustainable manufacturing approaches for uni-directional carbon fiber. Traditional production methods have been criticized for their energy consumption and waste generation. By exploring less resource-intensive techniques and renewable materials, the aim is to minimize the ecological footprint of production.
One promising area is the use of bio-based resins derived from plant materials instead of petroleum-based alternatives. These resins can significantly reduce the carbon footprint of the manufacturing process.
Furthermore, advancements in recycling methods are being developed. Engineers are exploring processes that allow for the reprocessing of carbon fiber composites, thus reducing the waste associated with end-of-life products.
As regulations tighten and public awareness increases, industries that adopt these sustainable practices may enhance their market competitiveness and contribute positively to environmental goals.
Future Perspectives on Uni-Directional Carbon Fiber
The exploration of future perspectives regarding uni-directional carbon fiber is essential for understanding its evolving role in various industries. Technological advancements and increased demand for high-performance materials are propelling its relevance across multiple sectors. This section aims to illuminate the emerging trends and potential avenues for growth.
Potential Emerging Markets
One of the significant areas of interest is the potential emerging markets for uni-directional carbon fiber. As industries strive for enhanced performance and reduced weight, sectors like aerospace, automotive, and construction are evaluating the benefits. Notably,
- Aerospace: The demand for lightweight yet strong materials is surging. Uni-directional carbon fiber can decrease fuel consumption and extend the lifespan of aircraft components.
- Automotive: In the pursuit of electric vehicles, uni-directional carbon fiber can significantly reduce overall vehicle weight, improving energy efficiency. This transition is crucial for meeting regulations on emissions.
- Sports Equipment: As athletes seek gear that maximizes performance, the sport industry is increasingly incorporating carbon fiber, which allows for innovative designs and better equipment durability.
Additionally, the medical sector shows potential for growth. Prosthetics and orthopedic implants utilizing uni-directional carbon fiber promise lighter, more robust solutions for patients.
Long-Term Industry Predictions
Looking ahead, long-term predictions indicate a promising future for uni-directional carbon fiber. Technological advancements in manufacturing processes, like automation and sustainability, are likely to redefine production efficiency. Key aspects to consider include:
- Cost Reduction: Improvements in production methods could lead to decreased costs, making carbon fiber more accessible for small- to mid-sized companies.
- Increased Versatility: Ongoing research into composite materials suggests a trajectory toward creating multi-functional applications. This could broaden utility beyond traditional uses.
- Sustainability Initiatives: As environmental regulations become stricter, incorporating sustainable practices in carbon fiber production could enhance its marketability and acceptance.
In summary, the future of uni-directional carbon fiber is not just about material properties. It encompasses a broader landscape of innovations, expanding markets, and sustainability efforts that will shape industry dynamics. The continuous evolution of this material signifies that both researchers and industry players must stay attuned to these developments to leverage competitive advantages.
Epilogue and Summary
The exploration of uni-directional carbon fiber, as detailed throughout this article, highlights its significance in material science and various industrial applications. Understanding the properties of this material is crucial for scientists and engineers who aim to innovate and enhance product performance. Efficient use of resources in production and a thorough grasp of challenges faces engineers in practical applications. Each section contributed to a holistic view of the subject.
Recap of Key Points
- Definition and Characteristics: Uni-directional carbon fiber is defined by its fiber alignment, which provides exceptional tensile strength in a single direction.
- Chemical Composition: The intricate balance of polymer matrix materials and the properties of carbon fibers contribute to the overall strength and durability.
- Production Methods: Insight into different manufacturing techniques showcases the innovations driving the industry forward.
- Material Properties: Key metrics include strength-to-weight ratio and fatigue resistance, critical for high-performance applications.
- Applications: Industries like aerospace, automotive, and sports demonstrate the vast utility of this material.
- Advantages and Limitations: Notable advantages include high strength and low weight, while challenges mainly revolve around production costs and consistency.
- Research Trends: Nanotechnology and sustainable manufacturing represent pivotal areas of growth.
- Future Perspectives: The anticipated emergence in diverse markets highlights new avenues for the application of uni-directional carbon fiber.
Final Thoughts
Uni-directional carbon fiber continues to be a game changer in multiple sectors. Its unique properties allow for innovative designs and more sustainable practices in manufacturing. Future trends suggest an increasing integration of advanced technologies, which will further enhance its applications. Industry predictions indicate that as research advances, the material's adaptability will become even more critical.
"The future of materials science rests not only in improving performance but also in maximizing sustainability."
"The future of materials science rests not only in improving performance but also in maximizing sustainability."
In summary, by following the outlined paths within this article, the relevance of uni-directional carbon fiber to modern engineering cannot be overstated. This material is not just a component; it is part of a broader narrative of innovation and efficiency.