Chemical Corrosion: Causes, Mechanisms, and Solutions
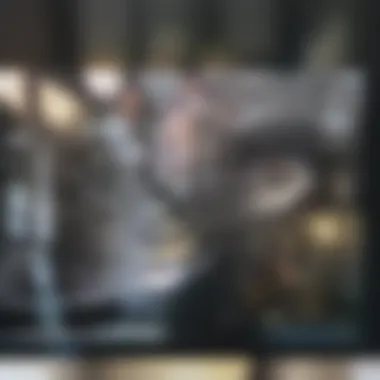
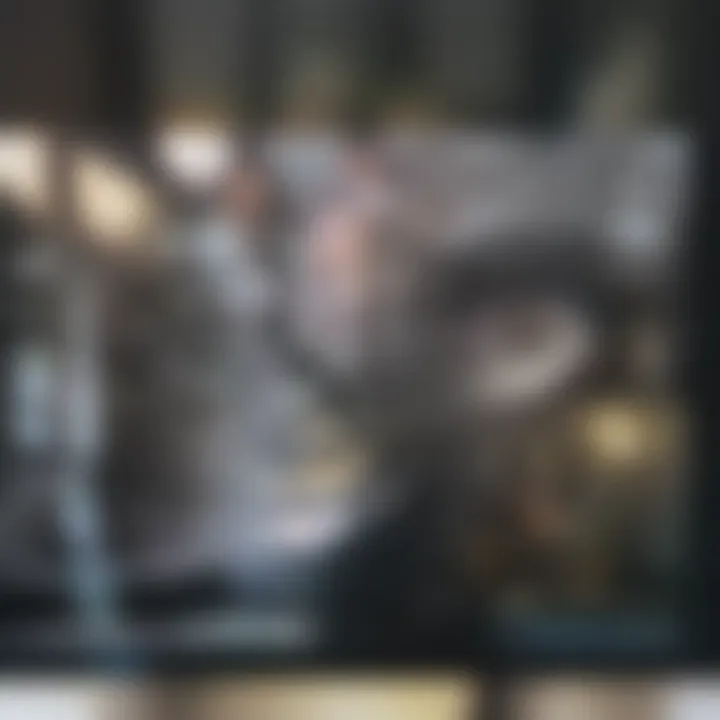
Intro
Chemical corrosion is a phenomenon that significantly impacts various materials and infrastructures across multiple fields. A thorough understanding of the causes, mechanisms, and effective mitigation strategies for this process is essential for professionals, educators, and researchers involved in engineering, chemistry, and environmental science. As industries strive for durability and sustainability, addressing corrosion becomes not just a technical necessity but a matter of operational efficiency and safety.
In this article, we serve to illuminate the intricate dynamics surrounding chemical corrosion. We will delve into its fundamental concepts, explore its historical background, and assess its relevance across different disciplines. Furthermore, we will discuss the implications of corrosion in practical applications and review contemporary research trends focused on improving corrosion resistance and management.
Prelude to Chemical Corrosion
Chemical corrosion is a pervasive and critical issue that affects various industries and infrastructures globally. Understanding this phenomenon is essential for engineers, researchers, and anyone involved in material science as it can lead to significant economic losses and safety concerns. The forms of chemical corrosion can be diverse, impacting metals and alloys through different mechanisms and environmental factors.
Definition and Significance
Chemical corrosion can be defined as the degradation of materials, primarily metals, caused by chemical reactions with their environment. This process can result in the material loss and decreased integrity of structures. The significance of this topic lies in its implications. For instance, the failure of a corroded pipeline can lead to spills, causing environmental harm and financial losses while compromising public safety. Therefore, understanding the mechanisms and types of corrosion is vital for developing effective prevention strategies.
In a practical sense, recognizing the signs of corrosion and understanding its causes can help in the selection of appropriate materials for construction and manufacturing. The early detection of corrosion can also mitigate potential failures before they escalate into more damaging consequences.
Historical Context
Historically, the study of corrosion dates back centuries. Ancient civilizations, such as those in Egypt and Rome, dealt with corroded metal artifacts and structures, leading to a gradual understanding of how and why materials failed over time. Modern insights began to emerge in the 19th century with advancements in electrochemistry, which clarified the mechanisms behind corrosion. For example, in 1824, scientist Michael Faraday led studies on electrochemical reactions, establishing foundational theories that would support modern corrosion science.
Moreover, notable events in history, such as the corrosion of ships during maritime trade or that of bridges and other structures due to poor material choices, highlighted the need for ongoing research and proactive measures against corrosion. Today, our understanding continues to evolve. Newer materials, coatings, and technologies are developed every year, presenting unique solutions to reduce corrosion rates and enhance material longevity.
Understanding chemical corrosion is not just a matter of material science; it plays a critical role in safety, economy, and the longevity of structures in contemporary society.
Understanding chemical corrosion is not just a matter of material science; it plays a critical role in safety, economy, and the longevity of structures in contemporary society.
The interplay between environmental factors, material composition, and exposure conditions continues to present challenges for industries worldwide. This article will explore in-depth each aspect of chemical corrosion, addressing its causes, consequences, and approaches for mitigation.
Fundamental Principles of Corrosion
Understanding the fundamental principles of corrosion is essential for effectively addressing this pervasive issue in various industries. Corrosion not only compromises the integrity of materials but also incurs significant economic losses. This section aims to elucidate the core aspects of corrosion's electrochemical nature, providing insights into the intricate interactions between materials and their environments. Grasping these principles allows professionals and researchers to devise better prevention and mitigation strategies, ultimately leading to safer and more efficient systems.
The Electrochemical Basis of Corrosion
Corrosion originates from electrochemical reactions that occur when a metal interacts with its environment. These reactions are often dependent on the material's properties and its exposure to moisture, temperature, and various chemicals. To understand this process, it is crucial to recognize that metals naturally strive to revert to their ionic state. This reversion occurs through oxidation, a process where a metal loses electrons, leading to its degradation.
Electrochemical corrosion can be divided into two main components: anodic and cathodic reactions. The anodic reaction involves the metal losing electrons, while the cathodic reaction typically leads to the reduction of another species that gains those electrons. The driving force of corrosion is the potential difference between the anodic and cathodic areas on the metal's surface. This potential difference creates an electrochemical cell, facilitating the flow of electrons and promoting further corrosion.
In summary, understanding the electrochemical basis of corrosion is vital as it informs the selection of materials and the design of protective systems. The ability to predict and analyze corrosion behavior can lead to more durable products and infrastructure.
Anodic and Cathodic Reactions
In the study of corrosion, anodic and cathodic reactions play a crucial role. Each reaction contributes differently to the overall corrosion process.
- Anodic Reactions: The anodic reaction is characterized by the oxidation of the metal, where it loses electrons. For example, in the case of iron, the reaction can be represented as follows:This reaction indicates that solid iron (Fe) is converted into ferrous ions (FeΒ²βΊ) upon losing two electrons, signifying the degradation of the metal.
- Cathodic Reactions: In contrast, cathodic reactions involve the reduction of an oxidizing agent. In many scenarios, this can include the reduction of oxygen. A common cathodic reaction in the presence of water is:This reaction shows how oxygen reacts with water and electrons to produce hydroxide ions. The formation of hydroxide ions in water often leads to the establishment of a protective layer on the metal's surface, which can mitigate the overall corrosion process.
The interplay between anodic and cathodic reactions is critical for understanding the kinetics of corrosion. By controlling these reactions, researchers can devise effective corrosion prevention techniques.
"Knowledge of anodic and cathodic reactions is integral to advancing corrosion management technologies."
"Knowledge of anodic and cathodic reactions is integral to advancing corrosion management technologies."
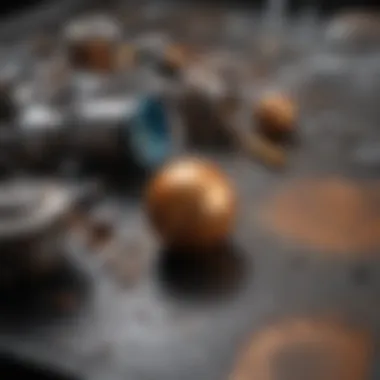
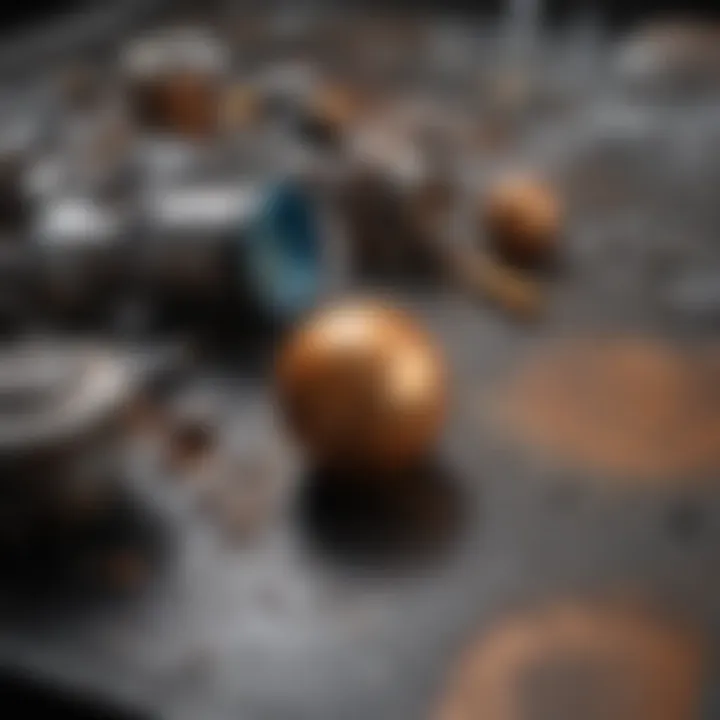
In summary, a deep understanding of anodic and cathodic reactions not only elucidates the mechanisms behind corrosion but also aids in the development of strategies to prolong the life of materials, ultimately enhancing safety and efficiency.
Types of Corrosion
Understanding the types of corrosion is essential for engineers, researchers, and industry professionals alike. Each type presents unique challenges and implications for material integrity and lifespan. By identifying specific corrosion types, one can better tailor mitigation strategies to combat deterioration effectively. This section details several prevalent forms of corrosion: uniform, pitting, crevice, galvanic, and intergranular corrosion.
Uniform Corrosion
Uniform corrosion occurs evenly across a material's surface and is often the most predictable form of corrosion. It affects materials in a consistent manner, leading to a gradual loss of thickness. This type is common in metals exposed to various environments. For instance, mild steel in a moist atmosphere will fall prey to uniform corrosion.
Important aspects include:
- Measurement: Its effects can be easily measured by taking periodic thickness readings.
- Predictability: The uniform loss of material allows for easier scheduling of maintenance and replacement.
- Cost Implications: Predictable rates help businesses anticipate material replacement costs.
Minimizing uniform corrosion typically involves selecting corrosion-resistant materials or implementing protective coatings.
Pitting Corrosion
Pitting corrosion is localized and results in small, deep cavities or
Factors Influencing Corrosion Rates
Understanding the factors that influence corrosion rates is essential in managing and mitigating chemical corrosion effectively. This section delves into three primary elements: Environmental Conditions, Material Composition, and Presence of Contaminants. Each of these aspects plays a critical role in the rate at which corrosion occurs. Recognizing these factors helps engineers, researchers, and industry professionals develop strategies that can significantly reduce material degradation over time.
Environmental Conditions
The environment in which materials operate has a profound effect on corrosion. Factors such as humidity, temperature, and the presence of salts or acids in the atmosphere can accelerate corrosive processes.
- Humidity: High humidity levels often lead to increased moisture on surfaces, which creates an ideal setting for electrolytic reactions. The higher the moisture, the more rapid the corrosion can become.
- Temperature: Elevated temperatures generally increase the rate of chemical reactions, including corrosion. For many metals, corrosion rates can double with every 10 degrees Celsius increase in temperature.
- pH Levels: The acidity or alkalinity of the environment also impacts corrosion. Acidic conditions can enhance the solubility of metal ions, speeding up the corrosion process. Conversely, alkaline environments may provide some degree of protection to certain materials.
Overall, a thorough understanding of these environmental factors allows for better planning and protective measures.
Material Composition
The inherent properties of materials themselves significantly shape their corrosion resistance. Different alloys and metals exhibit varying levels of susceptibility to corrosion based on their composition.
- Alloying Elements: Elements such as chromium in stainless steel provide protective oxide layers that enhance resistance to corrosion. Understanding how each element influences the overall corrosion resistance is vital for proper material selection.
- Microstructure: The grain structure of a metallic material is also critical. Smaller grain sizes often lead to increased strength and lower corrosion rates due to the uniform distribution of alloying elements.
- Surface Treatments: Processes such as anodizing or galvanizing can provide protective barriers against corrosion. These treatments enhance the natural properties of the material, making them more resistant to environmental impacts.
Careful consideration of material selection is essential for predicting and managing corrosion behavior.
Presence of Contaminants
Contaminants in the environment can significantly accelerate corrosion. These may include both environmental pollutants and surface impurities that come into contact with materials.
- Chlorides: Salts, especially chlorides, are particularly aggressive in corrosive environments. They can penetrate protective oxide layers on metals, leading to localized corrosion, such as pitting.
- Pollutants: Industrial emissions, including sulfur dioxide and nitrogen oxides, can react with moisture to form acids, creating an environment conducive to corrosion.
- Organic Compounds: Hydrocarbons and other organic substances can also interact with materials, potentially leading to degradation of protective coatings and increase the risk of corrosion.
Effective monitoring and controlling the presence of these contaminants is critical in corrosion management.
Understanding the factors influencing corrosion rates aids in developing targeted mitigation strategies, thus ensuring longevity in material performance.
Understanding the factors influencing corrosion rates aids in developing targeted mitigation strategies, thus ensuring longevity in material performance.
Detection and Evaluation of Corrosion
Detection and evaluation of corrosion are crucial for understanding the condition of materials and structures over time. Early identification of corrosion can prevent catastrophic failure and mitigate extensive repair costs. It assists in maintaining the integrity of infrastructure and industrial equipment. By observing and measuring corrosion, it is possible to develop better strategies for managing and mitigating its effects, ensuring safe and reliable operation in various environments.
Visual Inspection Techniques
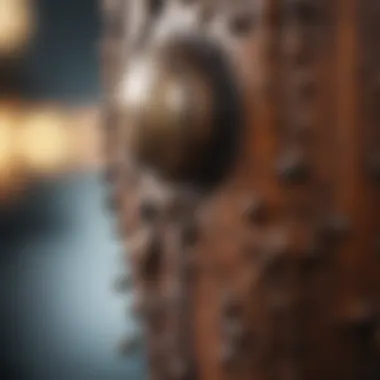
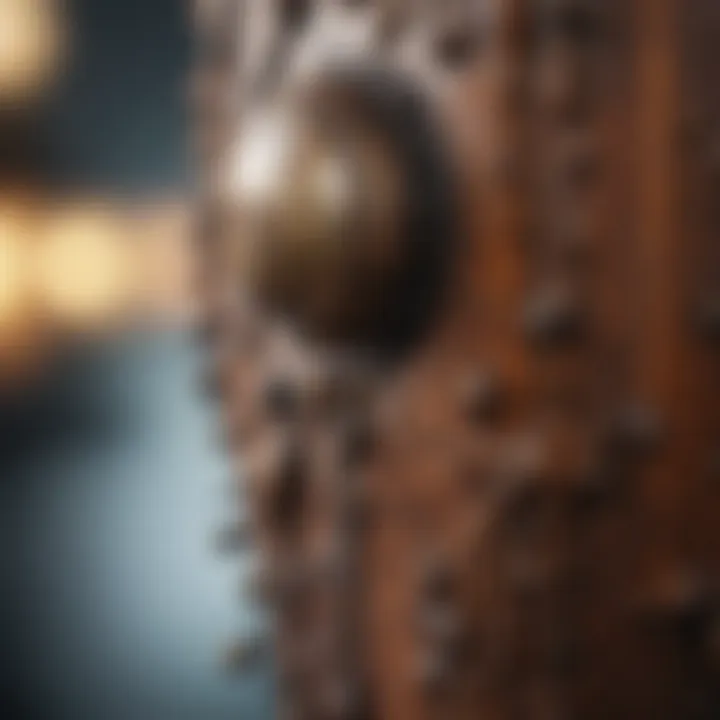
Visual inspection remains one of the simplest and most effective methods for detecting corrosion. It involves a careful examination of surfaces for any signs of rust, discoloration, or structural changes. Inspectors often use tools like magnifying glasses or borescopes to get a closer look at hard-to-reach areas.
Benefits of Visual Inspection:
- Cost-effective: It does not require sophisticated equipment.
- Quick assessment: Allows for immediate identification of visible issues.
- Foundation for further testing: It can indicate where more detailed analysis is necessary.
Despite its advantages, visual inspection has limitations. It might not detect subsurface corrosion or internal damage, thus necessitating additional methods for comprehensive evaluation.
Electrochemical Methods
Electrochemical methods provide a more in-depth analysis of corrosion processes. These techniques involve measuring the electrical properties of materials, which can reveal details about corrosion rates and environmental effects. This can includes methods like potentiodynamic polarization, electrochemical impedance spectroscopy, and linear polarization resistance.
Advantages of Electrochemical Methods:
- Quantification of Corrosion Rate: Offers measurable data on how quickly corrosion occurs.
- Real-time Analysis: Data can be gathered while the material is in its working condition.
- Detailed Insight: Provides valuable information about the surrounding environment and how it impacts material degradation.
However, electrochemical methods require skilled personnel and specialized equipment, making them more expensive than basic visual inspections.
Non-Destructive Testing
Non-destructive testing (NDT) techniques are vital when evaluating critical components without causing any damage. Methods such as ultrasonic testing, radiography, and magnetic particle testing enable engineers to assess the integrity of structures reliably.
Benefits of Non-Destructive Testing:
- Preservation of Integrity: The material remains intact while evaluations are done.
- Thoroughness: Offers detailed insights into hidden corrosion that might not be apparent through other methods.
- Versatility: Applicable to a wide range of materials and structures.
While NDT can be more expensive and time-consuming, the flexibility and thoroughness of the approach often justify the investment.
"Effective corrosion detection is not just a practice; it is an essential strategy for preserving material integrity and safety."
"Effective corrosion detection is not just a practice; it is an essential strategy for preserving material integrity and safety."
Mitigation Strategies
Mitigation strategies hold a pivotal role in managing chemical corrosion. The effects of corrosion can be detrimental, leading to significant financial losses and safety hazards. Therefore, understanding and implementing effective mitigation methods is crucial. These strategies not only prolong the lifespan of materials and structures but also enhance their overall performance. They involve careful planning, choosing suitable materials, applying protective measures, and monitoring systems that can efficiently detect corrosion before it escalates.
Material Selection
Material selection serves as a fundamental step in corrosion mitigation. Identifying and using materials that are less susceptible to chemical degradation is vital. Factors such as environmental exposure, mechanical loads, and the presence of corrosive substances must be considered. For example, stainless steels are often chosen for their resistance to rust and corrosion, especially in moist environments. Moreover, newer materials like composite alloys or advanced polymers can further improve resistance. Corrosion-resistant materials usually cost more initially, yet they provide long-term savings by reducing maintenance costs and replacement needs.
Protective Coatings
Protective coatings act as barriers between the environment and the underlying material. These coatings can significantly decrease the rate of corrosion. Common types include paints, galvanizing, and powder coatings. Selection depends on the specific application and environmental conditions. Proper application of coatings is also essential. A poorly applied coating can trap moisture and worsen corrosion. Regular inspections can ensure durability and function over time. The use of such coatings not only enhances appearance but also contributes greatly to longevity of structures and equipment.
Cathodic Protection Systems
Cathodic protection is an electrochemical technique widely adopted to preserve metal surfaces. It works by making the metal surface the cathode in an electrochemical cell. Two primary methods are used: galvanic anodes and impressed current systems. Galvanic anodes involve attaching a more reactive metal to the protected metal. In contrast, impressed current systems utilize an external power source to produce a protective current. Both systems are effective in varying applications, such as pipelines and storage tanks. However, the installation and maintenance of cathodic protection systems require careful assessment, planning, and periodic monitoring to ensure optimal performance.
Corrosion Inhibitors
Corrosion inhibitors are substances added to environments to decrease the rate of corrosion reactions. They can be categorized as anodic, cathodic, or mixed inhibitors based on their mode of action. For instance, anodic inhibitors create a passive film on metal surfaces, while cathodic inhibitors interfere with cathodic reactions. The application of inhibitors is often used in industrial systems, such as cooling water systems and oil pipelines. However, when using corrosion inhibitors, it is crucial to understand their potential environmental impact. Relying solely on inhibitors may not lead to sustainability; therefore, combining them with other mitigation strategies often yields the best results.
The integration of multiple mitigation strategies is key in achieving optimal corrosion management.
The integration of multiple mitigation strategies is key in achieving optimal corrosion management.
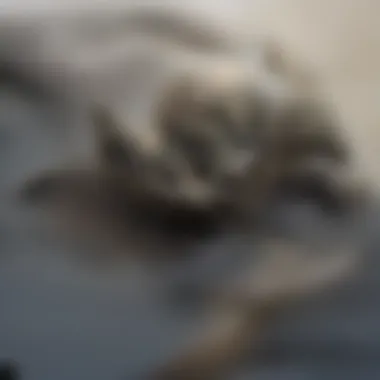
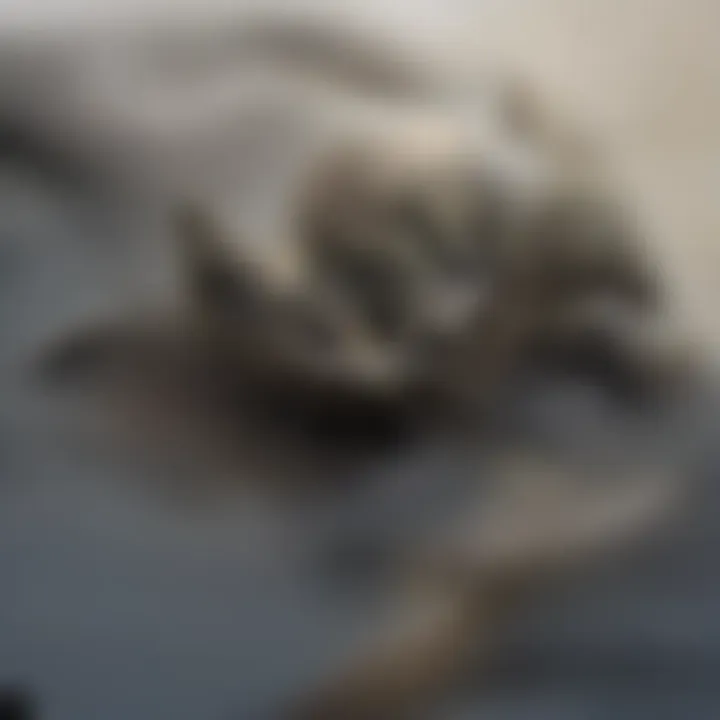
In summary, effective corrosion mitigation strategies hinge on prudent material selection, application of protective coatings, utilization of cathodic protection, and implementation of corrosion inhibitors. Each method presents unique advantages and considerations. By employing a combination of these strategies, industries can proactively address the challenges of chemical corrosion.
Case Studies in Corrosion Management
Understanding corrosion management through case studies presents a nuanced picture of how various industries combat this omnipresent challenge. These studies allow us to observe practical implementations of theoretical knowledge, bridging the gap between research and real-world application. Analyzing specific instances of corrosion both sheds light on effective strategies and highlights pitfalls, ensuring future projects benefit from previous experiences. The benefits of these case studies extend beyond mere documentation; they offer tangible lessons in both failure and success, essential for effective corrosion management.
Corrosion in Infrastructure
Corrosion in infrastructure remains a pressing issue globally. Bridges, highways, and pipelines are not only vital for transportation and supply but also costly and complex to maintain. The case of the Tacoma Narrows Bridge serves as a historical lesson in understanding infrastructural failure due to corrosion. A series of inspections detected corrosion in the steel components, prompting a comprehensive rehabilitation effort. This incident illustrates the need for regular assessments and preventive measures in construction.
Effective corrosion management techniques employed include the application of protective coatings, such as polyurethane paint, which enhances resilience against environmental stressors. Additionally, ongoing monitoring systems now play a critical role in detecting early signs of corrosion, allowing timely interventions and extending infrastructure lifespan. Infrastructure managers increasingly favor real-time monitoring technologies, which help predict and prevent deterioration, showcasing the successful integration of advanced technologies into corrosion management practices.
Industrial Equipment Failure
The industrial sector faces significant challenges from corrosion-related failures. A prominent case is that of Petrobras, a leading Brazilian petroleum company. The company reported debilitating corrosion issues in offshore drilling platforms, which led to equipment failure and substantial economic losses. This incident underscored the critical nature of preventive maintenance and regular inspections in industrial contexts.
To mitigate similar risks, companies are reevaluating their material choices, shifting towards high-performance alloys or plastics designed to withstand harsh environments. Furthermore, rigorous training for personnel in identifying corrosion and understanding its impact becomes essential. By learning from such instances, industrial operators can refine their protocols, ensuring better outcomes in corrosion management.
It is crucial for industries to embrace a proactive approach rather than a reactive one, turning to innovative materials and monitoring techniques to combat corrosion before it manifests as catastrophic failure.
It is crucial for industries to embrace a proactive approach rather than a reactive one, turning to innovative materials and monitoring techniques to combat corrosion before it manifests as catastrophic failure.
Future Trends in Corrosion Research
Future trends in corrosion research are pivotal as societies increasingly rely on infrastructure and materials that must withstand various environmental stresses. Understanding the cause and effect relationships within corrosion phenomena has always been critical, but the advent of innovative materials and advanced monitoring technologies is unlocking new avenues for enhanced protection and management strategies.
As industries evolve, adopting materials that resist corrosion will not only reduce maintenance costs but also extend the lifespan of components. The role of researchers is thus indispensable in identifying and developing these materials, ensuring that the foundations of modern infrastructures remain robust against degradation.
Moreover, technological advancements in monitoring assist in predicting corrosion issues before they escalate. Accurate and timely data can inform maintenance schedules and design choices, leading to more sustainable engineering practices. The subsequent sections will delve deeply into these innovative materials and monitoring methodologies that outline the future of corrosion research.
Innovative Materials
The development of innovative materials is at the forefront of corrosion research. Materials scientists are exploring several options that exhibit superior resistance to corrosion while maintaining essential mechanical properties. This includes alloys, composites, and coatings specifically designed for harsh environments.
- Zinc-Aluminum Alloys: These provide significant resistance to corrosion, especially in urban environments. Their application in construction can result in longer-lasting structural integrity.
- Polymer Coatings: Modern polymers, when used as protective coatings, create barriers against environmental attacks. Epoxy and polyurethane coatings help in mitigating corrosion by reducing moisture penetration.
- Corrosion-Resistant Steels: Advances in metallurgy now allow for producing steels with higher resistance to environmental factors. This is essential in sectors like automotive and aerospace where weight and durability matter.
The advantages of these materials go beyond just resistance. They can also contribute to sustainability, as longer-lasting materials lead to reduced waste and lower lifecycle costs. The pursuit of innovative portfolios in materials science is likely to determine the effectiveness of future corrosion management strategies.
Advanced Monitoring Technologies
Advanced monitoring technologies have transformed how industries approach corrosion management. With the integration of smart technologies and data analytics, it is possible to monitor corrosion in real-time, facilitating proactive maintenance practices.
- Electrochemical Impedance Spectroscopy (EIS): This technique provides valuable insights into the electrochemical behavior of materials in situ, allowing for the early detection of corrosion processes.
- Ultrasonic Testing: By employing sound waves, this non-destructive testing method can assess the integrity of materials, revealing hidden corrosion without physically altering the structure.
- Wireless Sensor Networks: These systems collect data from multiple sensors distributed over a large area, providing comprehensive monitoring capabilities. The data can be analyzed in real time, thereby alerting operators to potential issues.
"Timely detection and intervention can save significant costs and extend the life of critical infrastructures."
"Timely detection and intervention can save significant costs and extend the life of critical infrastructures."
Incorporating these monitoring technologies enables a more dynamic understanding of corrosion, transforming static management strategies into adaptive frameworks. This empowers industries to allocate resources efficiently while minimizing risk and enhancing safety.
As the field progresses, continued investment in both materials research and monitoring technology will be essential. The alignment of these trends signifies a proactive approach to mitigating corrosion, prioritizing long-term durability in various applications.
Ending
Understanding chemical corrosion is essential for anyone involved in industries reliant on metals, infrastructure, and engineering practices. Corrosion impacts material lifespan, safety, and functional integrity. The conclusions drawn here reflect on the necessity of recognizing various corrosion types, their causes, and ways to manage their effects.
Summary of Key Points
- Definition of Chemical Corrosion: Corrosion is a destructive process through which materials, often metals, degrade due to chemical reactions with their environment.
- Types of Corrosion: The article categorized several corrosion types, including uniform, pitting, crevice, galvanic, and intergranular corrosion, emphasizing their unique mechanisms.
- Factors Influencing Corrosion: Key factors such as environmental conditions, material properties, and contaminants play a significant role in corrosion rates.
- Detection and Evaluation: Methods for detecting and assessing corrosion include visual inspections, electrochemical techniques, and non-destructive testing, each providing insight into corrosion presence and severity.
- Mitigation Strategies: Effective strategies for managing corrosion encompass material selection, applying protective coatings, utilizing cathodic protection, and deploying corrosion inhibitors.
- Future Trends: Innovations in materials and advanced monitoring technologies are paving the way for enhanced corrosion management, essential for sustainability and safety in various sectors.
Final Thoughts
Moving forward, continuous research and advancements in corrosion studies will play an integral role in developing materials and technologies capable of withstanding corrosive environments. Through engagement with these advancements, professionals can better equip themselves to face the challenges posed by corrosion in their respective fields.