Direct Catalyst Recycling: Innovations and Implications
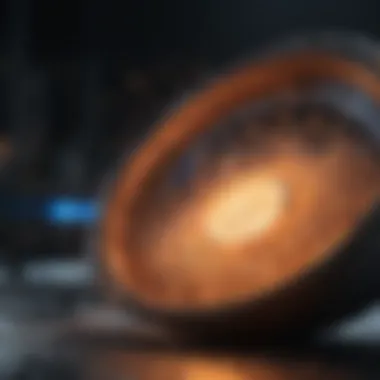
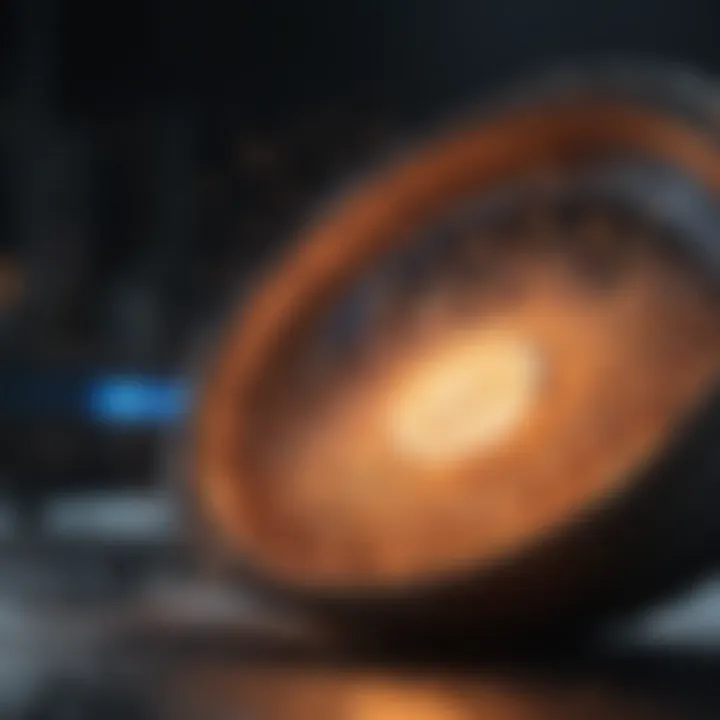
Intro
Direct catalyst recycling is a crucial evolution in sustainable chemistry. It represents a shift toward more efficient and environmentally friendly industrial practices. The significance of this topic cannot be overstated. As industries face increasing pressure to minimize waste and reduce costs, direct recycling of catalysts emerges as an innovative solution.
This section begins the exploration of catalyst recycling's role in modern industrial processes. Understanding both the theoretical and practical implications of this method is essential for researchers, educators, and professionals in fields relevant to chemistry and manufacturing.
An interdisciplinary approach is fundamental when discussing direct catalyst recycling. By examining the connections between chemical engineering, environmental science, and economics, one can appreciate the broader impact this innovation might have across various sectors.
Article Overview
Purpose of the Article
The focus of this article is to delve into the methods, challenges, and advantages of direct catalyst recycling. It aims to highlight how this practice not only aids in sustainability but also contributes positively to economic factors. The article will review several case studies, showcasing how different industries have successfully implemented direct recycling strategies. Furthermore, it intends to present a comprehensive overview that enhances our understanding of catalyst management for all stakeholders involved.
Relevance to Multiple Disciplines
Direct catalyst recycling is relevant to a variety of disciplines, including:
- Chemistry: Innovates traditional processes by improving catalyst efficiency.
- Environmental Science: Highlights waste reduction and resource conservation.
- Economics: Presents cost-effective alternatives that can boost profitability.
- Engineering: Involves expertise in designing systems for optimal catalyst recovery.
Understanding these intersections can foster collaboration across fields, ultimately advancing research and practical applications in catalyst recycling.
Research Background
Historical Context
To appreciate direct catalyst recycling, one must consider the historical development of catalyst usage. In the early days of chemical manufacturing, catalysts were often discarded after a single use. As industries grew and regulations tightened, the realization that catalyst recovery could reduce costs and environmental impact became evident. This led to more sophisticated methods aimed at recycling catalysts effectively.
Key Concepts and Definitions
Defining key concepts is vital for clarity:
- Catalyst: A substance that accelerates a chemical reaction without being consumed.
- Recycling: The process of converting waste materials into reusable products.
- Direct Catalyst Recycling: A method that enables the reuse of catalysts in chemical processes without significant alteration in their structure or function.
"In direct catalyst recycling, the emphasis is on recovering the catalyst directly from the reaction mixture, enhancing both sustainability and economic viability."
"In direct catalyst recycling, the emphasis is on recovering the catalyst directly from the reaction mixture, enhancing both sustainability and economic viability."
As we proceed, we will examine various methods of catalyst recovery and the specific benefits tied to direct recycling. This exploration illuminates the path forward for sustainable industrial practices.
Prelude to Direct Catalyst Recycling
Direct catalyst recycling is a critical area of focus in modern chemistry, particularly within the realm of sustainable practices. The significance of this topic lies in its potential to revolutionize how catalysts are managed in various industrial applications.
Catalysts play a vital role in chemical processes, enhancing reaction rates and efficiency. However, traditional recycling methods often result in substantial loss of valuable materials and can be environmentally harmful. Direct catalyst recycling enables industries to recover catalysts from used materials efficiently and effectively, minimizing waste and promoting resource sustainability. This not only helps preserve precious resources but also reduces the environmental footprint associated with traditional catalyst disposal methods.
In the context of this article, the discussion will center on two primary aspects of direct catalyst recycling:
- Definition and overview of the process.
- The broader importance of this method in the transition towards sustainable chemistry practices.
This topic becomes more relevant as industries face increasing pressure to adopt greener practices and demonstrate social responsibility. With innovations emerging in recycling techniques and technology, understanding direct catalyst recycling can empower researchers and professionals alike to make informed decisions that contribute to a more sustainable future.
Definition and Overview
Direct catalyst recycling refers to methods that facilitate the recovery of catalysts from reactions without the need for intermediate processing stages. This contrasts with traditional methods that often involve complex purification steps, leading to lower recovery rates and higher environmental impacts.
The main goal of direct catalyst recycling is to reclaim catalysts in a more streamlined manner. Techniques may include solvent extraction, precipitation, or even solid-state processes that allow for rapid recovery with minimal loss. By effectively leveraging these techniques, the industry can improve overall efficiency and reduce operational costs.
Importance in Sustainable Chemistry
The importance of direct catalyst recycling in sustainable chemistry cannot be understated. Here are several reasons why this method is crucial:
- Resource Conservation: Direct recycling helps preserve finite resources by minimizing the demand for new catalysts.
- Environmental Benefits: Reducing the ecological impacts of catalyst waste contributes to a cleaner environment. This aspect is particularly vital given the growing concerns over pollution and waste management.
- Cost Efficiency: By reclaiming materials effectively, companies can lower production costs and increase profitability. This economic advantage can incentivize more firms to adopt sustainable practices.
"The shift towards direct catalyst recycling highlights the industry's commitment to sustainability and resource management."
"The shift towards direct catalyst recycling highlights the industry's commitment to sustainability and resource management."
The Mechanisms of Catalyst Functionality
Understanding the mechanisms of catalyst functionality is essential for grasping the nuances of direct catalyst recycling. Catalysts, by nature, are substances that enhance the rate of chemical reactions without undergoing permanent change themselves. This unique characteristic underlines why effective recycling of these materials is crucial in both chemical and industrial processes. As the demand for sustainable practices rises, implementing efficient catalyst functionality allows industries to maintain productivity while minimizing waste.
Catalyst Types and Their Roles
Catalysts can be broadly categorized into two main types: heterogeneous and homogeneous catalysts. Heterogeneous catalysts operate in a different phase than the reactants, generally solid catalysts facilitating reactions in liquid or gas phases. An example includes the use of platinum in catalytic converters in vehicles, aiding in the conversion of harmful gases into benign substances. On the other hand, homogeneous catalysts exist in the same phase as their substrates. They often enhance reaction rates in solution-based processes, such as in pharmaceutical synthesis.
Each type brings unique benefits. Heterogeneous catalysts can be easily separated from the reaction mixture after the process, making them ideal for recycling. This ability to recover them allows for multiple usage cycles with minimal loss of efficacy. Conversely, homogeneous catalysts can provide higher selectivity and efficiency in some reactions but often pose challenges for separation and recovery. Both types of catalysts play vital roles in various industrial applications, influencing not only reaction efficiency but also the overall sustainability of the processes involved.
Catalyst Deactivation Processes
Catalysts, while effective, are subject to deactivation, which can significantly affect their performance. Understanding these deactivation processes is critical for enhancing the longevity of catalysts and improving recycling methods. Common forms of deactivation include poisoning, sintering, and coking.
- Poisoning occurs when an undesired substance binds to the active site of the catalyst, inhibiting its ability to facilitate reactions. This scenario is often found in catalytic converters, where specific toxins from exhaust gases can diminish catalytic activity.
- Sintering refers to the agglomeration of catalyst particles leading to a reduction in surface area. This process adversely affects reaction rates as fewer active sites are available for reaction.
- Coking involves the deposition of carbonaceous materials on the catalyst surface, physically obstructing access to active sites.
Understanding these deactivation mechanisms aids in formulating better recycling strategies. For example, techniques that regenerate catalysts could help mitigate the effects of poisoning or coking. By addressing these issues, direct catalyst recycling can significantly enhance both economic viability and environmental sustainability.
Traditional Catalyst Recycling Methods
The significance of traditional catalyst recycling methods lies in their established role within chemical processes. These methods have served as the backbone for optimizing resource use in industries where catalysts are critical. By recognizing how these conventional techniques work, one can appreciate the progression towards direct catalyst recycling. Traditional recycling methods help maximize efficiency while minimizing waste, which is essential in the pursuit of sustainable chemistry.
Overview of Conventional Techniques
Conventional techniques for catalyst recycling include approaches like thermal regeneration, chemical leaching, and solvent extraction. These methods have been used for many years and are well understood.
- Thermal Regeneration: This method utilizes heat to restore catalyst activity. It works best with catalysts that can endure high temperatures.
- Chemical Leaching: In this technique, solvents dissolve the catalyst, allowing for its recovery. It is often applied to metal catalysts.
- Solvent Extraction: This method separates catalysts from mixtures through solubility differences. Organic solvents are typically used.
Each of these methods has its specific use cases, advantages, and challenges. While effective in many scenarios, they are not without limitations.
Limitations of Traditional Approaches
Despite their established effectiveness, traditional recycling methods may not always be the best solution. Some of the key limitations include:
- Energy Intensive: Many conventional methods require significant energy input, potentially offsetting environmental benefits.
- Chemical Waste: The use of solvents and chemicals in processes like leaching creates additional waste, which poses disposal challenges.
- Material Loss: Often, a portion of the catalyst cannot be recovered, leading to material wastage.
- Cost: These methods can be expensive, particularly when high-purity catalysts are required.
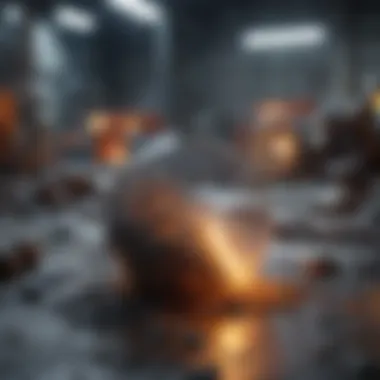

The drawbacks highlight the necessity to innovate beyond traditional methods.
The drawbacks highlight the necessity to innovate beyond traditional methods.
Understanding these limitations is essential when exploring more advanced recycling techniques, especially direct catalyst recycling. By addressing the downsides of conventional methods, the industry moves toward solutions that are more aligned with environmental and economic goals.
Innovative Techniques in Direct Catalyst Recycling
Innovative techniques in direct catalyst recycling represent a crucial element in the pursuit of sustainable industrial practices. As industries strive to reduce their environmental footprint, the adoption of these methods offers numerous advantages. Direct catalyst recycling minimizes waste, optimizes material use, and enhances economic efficiency. The exploration of various techniques is essential for understanding their implications in real-world applications.
Advancements in recycling technologies are not just about improving existing processes. They suggest a shift towards a more circular economy where valuable materials are continuously reused. This is where efficient recycling plays a pivotal role. By streamlining the recovery of catalysts, industries can not only comply with regulations but also enhance their sustainability profiles. The adoption of innovative techniques often translates into cost savings, which can be a compelling factor for businesses looking to improve their bottom lines while being environmentally responsible.
In this section, we will delve into two prominent approaches: solvent-based recovery techniques and solid-state recovery methods, each with its unique benefits and considerations.
Solvent-Based Recovery Techniques
Solvent-based recovery techniques have emerged as a prominent method in catalyst recycling. These methods often involve the use of liquid solvents to recover catalysts from reaction mixtures, allowing for easier separation and purification. A key advantage of solvent-based recovery is its versatility; it can be applied to various types of catalysts regardless of their structure or composition.
Benefits of Solvent-Based Techniques:
- High Recovery Rates: These techniques often yield high purity levels of the recovered materials, ensuring that the catalysts can be reused effectively.
- Flexibility: The process can be tailored to different catalysts, making it suitable for diverse industrial applications.
- Reduced Chemical Waste: By optimizing recovery processes, less waste is generated compared to traditional disposal methods.
However, solvent-based techniques are not without challenges. The selection of the appropriate solvent is crucial and can heavily influence the efficiency of recovery. Additionally, the environmental impact of solvents themselves must be considered. To mitigate potential risks, industries must prioritize the use of green solvents or recycle the solvents used in these processes.
Solid-State Recovery Methods
Solid-state recovery methods are another innovative approach gaining traction in catalyst recycling. Unlike solvent-based techniques, these methods allow for the recovery of catalysts while they remain in solid form, which can simplify the recycling process and minimize losses.
Key Features of Solid-State Methods:
- Reduced Solvent Use: These methods significantly decrease the need for solvents, which can lower environmental concerns surrounding chemical waste.
- Energy Efficiency: Solid-state processes can often operate at lower temperatures, reducing energy consumption and costs.
- Stability of Catalysts: Some catalysts can lose their effectiveness when exposed to solvents; solid-state recovery can preserve their activity.
Yet, it is important to acknowledge the technical complexities involved in solid-state recovery. Process optimization and careful control of reaction conditions are required to maximize recovery and maintain catalyst integrity.
Comparative Analysis: Direct vs Indirect Recycling
In the realm of catalyst recycling, understanding the distinctions between direct and indirect methods is crucial. Direct catalyst recycling refers to the reclaiming of catalysts without significant alteration to their chemical structure, while indirect recycling often involves more complex processes that can alter the catalysts chemically. This section articulates the importance of distinguishing these methods, particularly their implications for efficiency, costs, and environmental effects.
Efficiency Metrics
Efficiency in catalyst recycling is measured by the ability to recover valuable materials and restore their functionality. In direct recycling, efficiency metrics often showcase higher recovery rates of active catalysts. This method typically maximizes economic value while minimizing environmental footprint. For instance, direct methods can yield up to 90% recovery of certain catalysts with minimal waste generation. On the other hand, indirect recycling approaches may involve steps such as chemical modifications or thermal treatments, leading to some loss of the material's original properties. Therefore, from an efficiency perspective, direct recycling often presents advantages that are hard to overlook.
Key points regarding efficiency in recycling include:
- Higher recovery rates in direct recycling methods.
- Minimal waste phase generation.
- Faster processing times compared to indirect methods.
- Economic benefits derived from reduced material loss.
Environmental Impact Assessment
The environmental consequences of catalyst recycling are increasingly vital in today's economic and ecological landscape. Direct recycling methods typically have a lower environmental impact. This is due in part to their efficiency, which results in less waste generation and fewer associated emissions and pollutants.
In contrast, indirect recycling's complexity often involves significant energy consumption and potential environmental hazards from chemical treatments or byproducts. Direct recycling also aligns better with sustainability goals, as it promotes the circular economy by reusing materials effectively.
Important environmental factors to consider are:
- Reduction in energy consumption: Direct recycling generally requires less energy than indirect methods, thereby lowering greenhouse gas emissions.
- Less chemical waste: Indirect processes often lead to chemical byproducts that may require extensive management or disposal protocols.
- Biodiversity protection: Efficient direct recycling contributes less pollution, which is beneficial for surrounding ecosystems.
"Direct recycling reduces overall material waste, promoting environmental sustainability."
"Direct recycling reduces overall material waste, promoting environmental sustainability."
In summary, comprehensively analyzing the efficiency and environmental impacts of direct versus indirect catalyst recycling highlights direct methods as the preferable choice. Their benefits extend beyond immediate economic gains to foster a more sustainable industrial practice.
Applications of Direct Catalyst Recycling
The applications of direct catalyst recycling are essential for understanding its role in sustainable chemistry and industrial processes. This section highlights the relevance of catalyst recycling and presents its advantages in specific industries. The effective recovery and reuse of catalysts can result in significant resource savings and reduction of environmental impact. By implementing these technologies, companies can improve efficiency and promote sustainability.
Case Studies in the Chemical Industry
In the chemical sector, catalyst recycling has shown notable benefits. For instance, in the production of chemicals like polypropylene, direct recycling demonstrates high efficacy. Companies employ innovative methods to extract catalysts without major loss of their functional capabilities. The case of Huntsman Corporation exemplifies success in catalyst recovery from polymer processing. They achieved a 95% recovery rate with minimal quality compromise, showcasing how direct catalyst recycling can streamline production processes.
Another significant example is Chevron Phillips Chemical, which successfully integrated direct catalyst recycling in their olefins production. By utilizing solvent-based recovery techniques, they reported as much as a 90% reduction in waste generation. This not only cuts down costs but also enhances product yield. Such applications illustrate the practicality and effectiveness of direct catalyst recycling in the chemical industry.
Recycling in the Pharmaceutical Sector
In pharmaceuticals, catalyst recycling is particularly vital owing to the high cost and intricacies involved in drug synthesis. Companies are increasingly recognizing the potential of catalyst recovery to maximize output while reducing raw material usage. A prominent case is Pfizer, which has made strides in catalyst management through direct recycling methods. Their research indicated a 25% cost savings on average when employing recycled catalysts in their synthesis processes.
Additionally, Novartis is leveraging direct catalyst recycling to enhance the sustainability of their production lines. They focus on experiments that optimize catalyst life cycle, ensuring that active materials are reused effectively. This practice not only meets economic goals but further aligns with the company's sustainability pledges.
Through these case studies, the pharmaceutical sector clearly showcases the value of implementing direct catalyst recycling strategies. By overcoming operational challenges, companies can not only improve their economic performance but also contribute significantly to environmental sustainability.
"Direct catalyst recycling paves the way for a greener future in the chemical and pharmaceutical industries, proving that sustainability and profitability are not mutually exclusive."
"Direct catalyst recycling paves the way for a greener future in the chemical and pharmaceutical industries, proving that sustainability and profitability are not mutually exclusive."
These examples serve as a foundation for understanding the broader implications of catalyst recycling across industries. As companies continue to innovate and adapt these methods, the potential for economic and environmental benefits will only increase.
Regulatory Framework and Guidelines
The regulatory framework governing catalyst recycling plays a crucial role in ensuring both environmental safety and economic viability. A well-defined set of guidelines can facilitate innovation and drive practices that enhance sustainability across the chemical and pharmaceutical industries. Compliance with regulations is not merely a legal obligation; it reflects a commitment to environmental stewardship and can lead to increased public trust. Such frameworks help to standardize processes, reduce risks, and promote best practices in catalyst management.
Global Regulations on Catalyst Recycling
Regulations vary significantly by region but often share common goals. For instance, the European Union has established directives aimed at waste management and resource recovery. The Waste Framework Directive mandates member states to minimize waste and encourage recycling through specific targets. In the United States, the Environmental Protection Agency (EPA) oversees federal regulations that impact waste management practices, including catalyst recycling. Key regulations include the Resource Conservation and Recovery Act (RCRA), which governs hazardous waste materials.
Global regulations often emphasize the importance of lifecycle assessments, requiring companies to track the usage and reclamation of catalysts throughout their lifecycle. This holistic approach not only facilitates compliance but also enables organizations to identify opportunities for improvement in sustainability practices.
"Effective regulations can create a balanced environment where both the industry and the environment thrive."
"Effective regulations can create a balanced environment where both the industry and the environment thrive."
Industry Standards and Practices
Industry standards, such as those published by the American National Standards Institute (ANSI) or the International Organization for Standardization (ISO), provide frameworks for best practices in catalyst recycling. These standards help ensure consistent quality in the methodologies utilized for recovery and reuse.
Adopting these practices can provide numerous benefits, including:
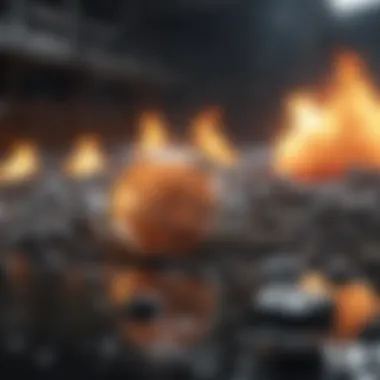
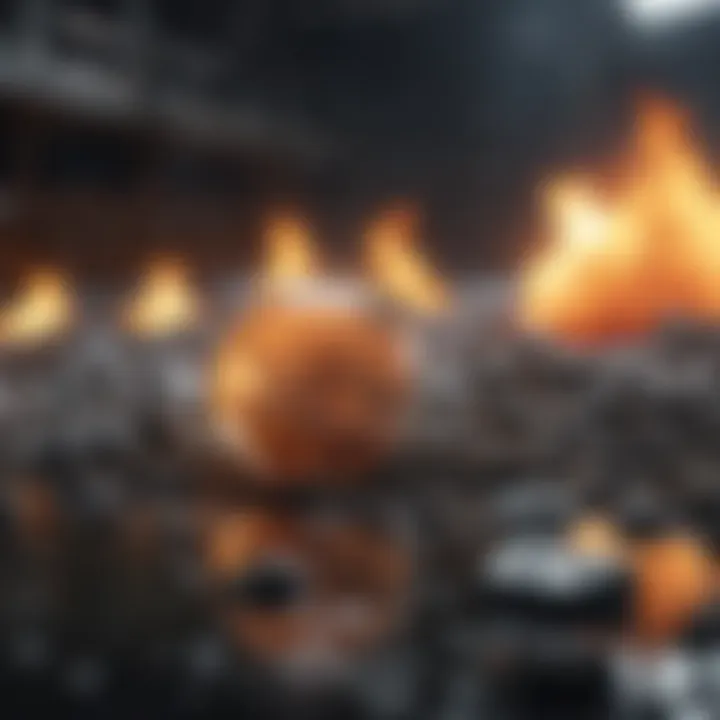
- Improved operational efficiency
- Reduction in environmental liability
- Enhanced market competitiveness
Moreover, industry guidelines often advocate for collaborative efforts among stakeholders. By fostering partnerships between academia, industry, and regulatory bodies, organizations can better navigate the complexities of catalyst recycling. The sharing of research, resources, and expertise promotes innovative solutions to address technical and economic challenges.
Challenges in Implementing Direct Catalyst Recycling
The topic of challenges in implementing direct catalyst recycling is critical in understanding the full scope of its impact on sustainable chemistry and industrial practices. As industries strive to adopt more eco-friendly practices, direct catalyst recycling presents a promising solution. However, several obstacles hinder its widespread adoption. Addressing these challenges is vital for unlocking the full potential of catalyst recycling, leading to enhanced efficiency, reduced environmental footprint, and long-term economic viability.
Technical Barriers
Technical barriers refer to the inherent limitations in processes, materials, and technologies used for catalyst recycling. The complexity of catalysts themselves plays a significant role. Catalysts like palladium, platinum, and rhodium are often costly and highly complex in their structure and function. Recovery techniques must be able to maintain their integrity and performance level after recycling. This is not always achievable due to varied chemical interactions during the recycling procedure.
Moreover, there is a lack of standardized methods for direct catalyst recycling. Each type of catalyst may require tailored strategies for efficient recovery. This customization can lead to increased costs and longer timeframes when implementing new technologies for different catalysts.
In addition, many companies working with catalysts have established processes that do not currently integrate recycling. Modifying or replacing these systems can prove to be a significant technological undertaking. Moreover, the equipment and processes to assess catalyst degradation and longevity are still evolving. Without well-defined technical standards, the adoption of efficient recycling methods becomes more difficult.
Economic Constraints
Economic constraints can significantly impact the implementation of direct catalyst recycling. High initial investment costs are often a deterrent for industries considering the switch to recycling practices. Companies may find it more cost-effective to continue with traditional disposal methods rather than invest in new technologies or processes for recycling catalysts.
In addition, the fluctuating market prices for recovered materials can create uncertainty. Industries dependent on specific catalysts may not see a clear financial return on investment from recycling efforts, particularly when market volatility affects the prices of raw materials. This risk can discourage investment in recycling technologies.
Furthermore, the economic landscape is influenced by regulatory pressures and compliance costs, which can vary greatly by region. Companies might hesitate to engage in recycling initiatives if they are unsure about whether the economic gains will outweigh the regulatory burdens.
Consequently, a comprehensive economic analysis that considers both short-term and long-term financial benefits is essential for overcoming these constraints. Such an analysis would help to create compelling business cases for direct catalyst recycling, showing that it can be not only environmentally friendly but also economically beneficial.
The successful implementation of direct catalyst recycling hinges on overcoming technical and economic challenges. By doing so, industries can reap the benefits of sustainability while also enhancing their bottom line.
The successful implementation of direct catalyst recycling hinges on overcoming technical and economic challenges. By doing so, industries can reap the benefits of sustainability while also enhancing their bottom line.
Future Directions in Catalyst Recycling Research
The focus of future research in catalyst recycling is important to ensure sustainability, efficiency, and economic viability. With increasing awareness around environmental concerns, researchers and industries must explore innovative solutions to enhance catalyst recovery methods. Direct catalyst recycling presents unique opportunities that can redefine how materials are managed within chemical processes. By emphasizing research endeavors, we can uncover novel technologies and pave the way for a more sustainable future.
Emerging Technologies
Research in direct catalyst recycling has unveiled numerous emerging technologies that can significantly improve recovery rates and reduce waste. One key area is the development of advanced materials that allow for better selectivity and efficiency in catalyst recovery.
- Nano-structured catalysts: These have shown better stability and reusability, which can lower the frequency of disposal.
- Biological methods: Utilizing microorganisms or enzymes can enable more environmentally friendly recycling processes, thus reducing chemical usage.
- Wastes streams utilization: Exploring ways to recover catalysts from spent materials, such as in mining or industrial processing, will provide avenues to improve resource management.
Despite these promising advancements, challenges remain. For example, integrating these new technologies into established processes requires time and investment. Researchers must also focus on ensuring that these technologies comply with regulatory standards and can be easily adopted by existing industries.
Interdisciplinary Collaborations
Collaborations among various disciplines are crucial for the advancement of catalyst recycling technologies. When chemistry, engineering, environmental science, and economics converge, a more holistic approach can be developed.
- Academic-Industry Partnerships: These can facilitate the transition of research findings to practical applications. Engaging industry players early in the research phase can help align efforts with real-world challenges.
- Cross-Disciplinary Research Teams: Encouraging teams that include chemists, biologists, and material scientists can lead to innovative approaches in the recycling of catalysts.
- Workshops and Conferences: Regular interactions between academia and industry, through conferences or educational programs, can help foster relationships and spark innovative ideas.
"The future of catalyst recycling lies not just in the technology itself but in the collaboration and ideas that come from diverse fields."
"The future of catalyst recycling lies not just in the technology itself but in the collaboration and ideas that come from diverse fields."
As researchers push boundaries and explore these new frontiers, it becomes evident that interdisciplinary efforts will be key in overcoming barriers faced by the catalyst recycling sector.
The Role of Industry and Academia
The intersection of industry and academia plays a critical role in advancing the field of direct catalyst recycling. This collaborative ecosystem enhances research, drives innovations, and facilitates the practical application of findings in real-world scenarios. Establishing strong partnerships between academic institutions and industry players is paramount for various reasons.
Firstly, industry provides valuable resources and funding for research projects. This financial support allows academic researchers to focus on innovative solutions without the burden of securing individual grants. By leveraging industry partnerships, academic institutions can access cutting-edge technologies and facilities that may be unavailable otherwise. This can expedite the research and development cycle, leading to quicker advancements in recycling methods and technologies.
Moreover, academia produces a wealth of knowledge that can be transformed into practical applications. Researchers often explore theoretical aspects and fundamental principles, which can be translated into valuable insights for industries engaged in catalyst recycling. When these insights are merged with industry needs, specific problems can be addressed effectively, thus improving overall efficiency in recycling operations.
Finally, the synergy between academia and industry fosters the generation of skilled professionals equipped with the necessary competencies to succeed in the field of catalyst recycling. Graduates from academic programs designed in collaboration with industry practitioners possess the technical skills and problem-solving abilities that are highly sought after in the workforce.
Collaborative Initiatives
Collaborative initiatives between industry and academia have led to significant advancements in catalyst recycling. Such efforts often include joint research projects, technology transfer partnerships, and consortiums that focus specifically on sustainability and resource recovery.
For example, companies and universities may align their research agendas to develop new catalyst recovery technologies that are both economically viable and environmentally friendly. Working together on funded projects can expand the scope of research that individual organizations might not achieve alone.
The establishment of research networks can also facilitate knowledge sharing. Participants from multiple sectors can bring their expertise to the table, resulting in a well-rounded approach to challenges in catalyst recycling.
Some benefits of collaborative initiatives include:
- Enhanced problem-solving capabilities through diverse expertise.
- Joint access to large-scale testing facilities and equipment.
- Increased visibility and credibility in the academic and industrial landscape.
These initiatives are integral to the evolutionary trajectory of direct catalyst recycling.
Educational Outreach and Training
Effective educational outreach and training programs are essential to raise awareness on the significance of direct catalyst recycling and foster interest among future generations. Academic institutions, together with industry partners, should design curriculum that not only covers theoretical knowledge but also emphasizes practical skills tailored for real-world application.
Workshops, seminars, and internships can greatly benefit students by providing hands-on experience. This exposure allows them to understand the nuances of catalyst recycling processes and develops competencies that prepare them for careers in this field.
Moreover, these outreach efforts can extend beyond traditional student populations. Engaging local communities and industries through public lectures, educational materials, or partnerships with non-profits can promote greater understanding of the environmental impacts of catalyst waste and the benefits of recycling.
Ultimately, establishing rigorous educational frameworks equips a new generation of researchers, engineers, and managers with the tools needed to enhance catalyst recycling efforts globally.
"The collaboration between academic researchers and industry practitioners catalyzes the development of innovative solutions in catalyst recycling systems."
"The collaboration between academic researchers and industry practitioners catalyzes the development of innovative solutions in catalyst recycling systems."
By investing in both educational outreach and collaborative initiatives, direct catalyst recycling can make informed strides toward becoming an integral component of sustainable practices in various sectors.
Economic Benefits of Direct Catalyst Recycling
Direct catalyst recycling offers significant economic advantages that are essential for industries aiming to optimize their operations. The transition towards direct recycling is increasingly recognized for its potential to enhance efficiency and reduce costs. In this section, we will explore the monetary implications of direct catalyst recycling, particularly focusing on cost savings and the evolving market landscape.
Cost Analysis and Savings
The financial implications of direct catalyst recycling are profound. By eliminating the need for new catalyst production, companies can substantially lower their raw material costs. This aspect is particularly crucial considering that catalyst materials, which often include precious metals such as platinum, palladium, and rhodium, can be highly expensive. Savings can accumulate in several areas:
- Reduced Raw Material Costs: Recycling catalysts allows for the reuse of valuable components, minimizing the need for purchasing new materials. This not only leads to significant cost reductions but also mitigates supply chain risks.
- Lower Waste Disposal Costs: Direct catalyst recycling decreases the volume of waste, which translates into reduced disposal fees. Consequently, companies can allocate resources more efficiently.
- Decreased Production Downtime: When catalysts are recycled effectively, the turnaround time for processes can be reduced. Less downtime means increased production efficiency and higher profit margins.
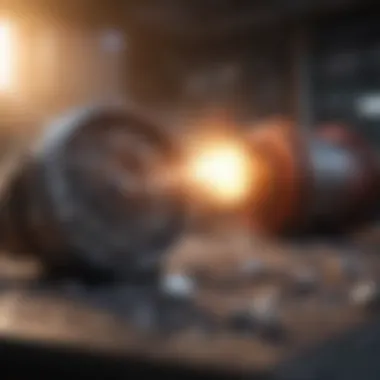
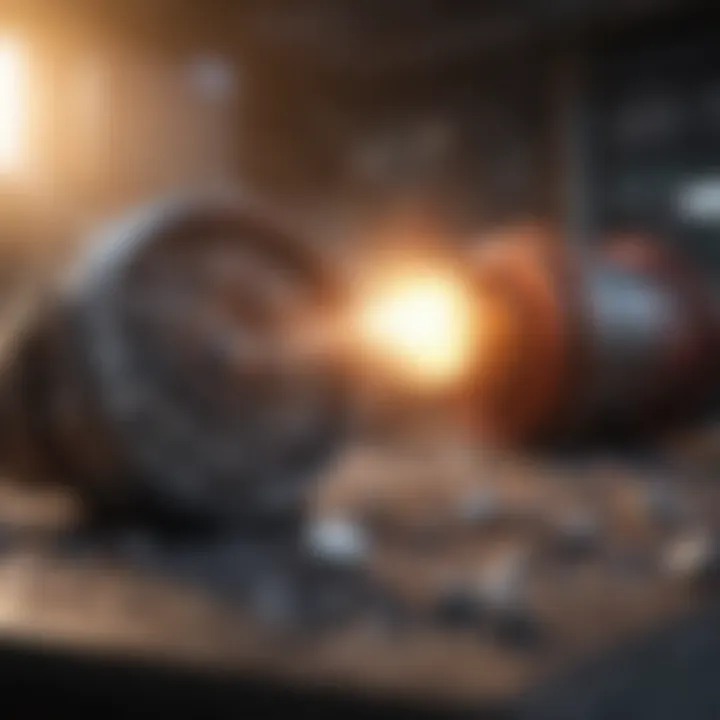
An effective cost analysis should include both short-term savings and long-term benefits, examining how direct catalyst recycling can contribute to overall financial health in a sustainable manner. For businesses operating in competitive markets, these savings can create a viable edge.
Market Trends and Opportunities
As industries expand their sustainability efforts, the significance of direct catalyst recycling in market strategies cannot be overstated. Several trends are reshaping the landscape:
- Growing Demand for Sustainable Practices: There is an increasing consumer demand for environmentally friendly manufacturing processes. Companies adhering to sustainable practices, including the recycling of catalysts, are often favored in both local and global markets.
- Innovation in Recycling Technologies: Advancements in recycling methods present new business opportunities. Firms investing in innovative direct recycling technologies can see enhanced efficiency, attracting both investors and customers.
- Collaboration with Research Institutions: Partnerships between industry and academia can lead to the development of improved recycling technologies. Such collaborations can foster innovation, demonstrating the economic merit of direct catalyst recycling.
In looking forward, industry players must adapt to changing consumer preferences and regulatory landscapes. The embrace of catalyst recycling will not only bolster profitability but also enhance sustainability, aligning economic and environmental imperatives.
In summary, direct catalyst recycling represents a financially prudent choice for many industries, driving cost efficiency while capitalizing on the growing demand for sustainable practices.
In summary, direct catalyst recycling represents a financially prudent choice for many industries, driving cost efficiency while capitalizing on the growing demand for sustainable practices.
Environmental Impact of Catalyst Recycling
The environmental impact of catalyst recycling is a critical component of sustainable chemistry. As industries continue to seek ways to lower their carbon footprints and minimize waste, catalyst recycling emerges as an effective strategy. The recycling process not only conserves resources but also reduces the environmental damage associated with mining and processing new materials. This section examines the ecological and economic benefits of direct catalyst recycling, along with significant factors influencing its implementation.
Ecological Considerations
Direct catalyst recycling significantly affects ecosystems by mitigating the need for raw materials. This process conserves natural resources, such as minerals and metals, which decreases habitat destruction and biodiversity loss. When catalytic materials are extracted, there is a tendency for pollution to occur, often resulting in soil and water contamination. By recycling these materials, the risk of environmental degradation is reduced.
- Reduction in Waste: Catalyst recycling can drastically lower the volume of waste produced. Instead of discarding used catalysts, they can be regenerated or reprocessed for future use.
- Energy Savings: Recycling often requires less energy than producing new catalysts from raw materials. This leads to decreased greenhouse gas emissions.
- Ecosystem Health: Reduced extraction and processing lead to fewer disturbances in natural habitats, allowing ecosystems to remain intact.
Recycling catalysts is a crucial step toward a more sustainable industry, making ecological sense for current and future generations.
Recycling catalysts is a crucial step toward a more sustainable industry, making ecological sense for current and future generations.
Life Cycle Assessment Studies
Life cycle assessments (LCA) serve a vital role in evaluating the sustainability of catalyst recycling. This method analyzes the environmental impacts of a product throughout its entire life cycle—from raw material extraction to disposal. In the context of catalyst recycling, LCA can offer insights into resource efficiency and environmental trade-offs.
- Assessment Tools: Various software and methodologies can capture the sustainability metrics of catalyst recycling processes. These tools can highlight energy use, emissions, and waste generation.
- Comparative Analysis: LCAs allow for comparisons between traditional catalyst usage and recycled catalysts, showcasing the benefits of adopting recycling practices.
- Long-Term Implications: By assessing the full life cycle, stakeholders can make informed decisions that favor environmental sustainability, thus fostering long-term ecological balance.
Technological Integration and Industry Readiness
The integration of technological advancements plays a critical role in the realm of direct catalyst recycling. As industries strive for more sustainable practices, the readiness to adopt these technologies becomes essential. Organizations must focus on aligning their operations with state-of-the-art recycling methods to maximize efficiency and reduce environmental impact.
The process of integrating new technologies encompasses various elements, including extensive research and development, as well as the availability of suitable infrastructure. This alignment is paramount as it directly influences the effectiveness of catalyst recovery initiatives. Direct catalyst recycling fosters the sustainable re-use of catalysts, significantly lowering the demand for raw materials and reducing waste. The benefits of this integration are manifold:
- Improved Recovery Rates: Innovative techniques can enhance the efficiency of catalyst recovery, ensuring a higher percentage of valuable material is reclaimed.
- Cost Efficiency: Investing in advanced technologies may initially seem high, but the long-term savings from reduced material costs can be substantial.
- Environmental Advantages: With enhanced recycling, industries can lower their carbon footprint, thus promoting a more eco-conscious image.
Technology Transfer Processes
One of the significant challenges in technological integration is the transfer of technology from research institutions to the industrial sector. This process requires collaboration between academia and industry to ensure that novel solutions are effectively adapted for practical application. Successful technology transfer involves several key steps:
- Pilot Programs: Before full-scale implementation, trials on a smaller scale can validate the efficacy of the technology.
- Feedback Mechanisms: Constructive feedback from early adopters helps refine processes.
- Training and Support: Providing training for personnel on new systems increases adoption rates and maximizes efficiency.
Encouragingly, many organizations are now establishing partnerships with academic institutions, facilitating smoother technology transfers.
Industry Adoption Strategies
Adopting new technologies in catalyst recycling requires strategic planning and execution. A few effective industry adoption strategies include:
- Assessing Readiness: Organizations should evaluate their current capabilities and readiness to integrate direct catalyst recycling solutions.
- Building Stakeholder Consensus: Engaging various stakeholders, including corporate leaders, regulatory bodies, and environmental groups, fosters support for new initiatives.
- Incorporating Flexibility: Industries must remain adaptable, as technologies and market conditions change, ensuring that their strategies can evolve over time.
By emphasizing these strategies, industries can move towards a more sustainable model. Successful adoption of advanced recycling technologies can lead to a paradigm shift in how catalysts are viewed in the production process.
The sustainable growth of industrial practices hinges on the ability to effectively integrate innovative recycling technologies, making readiness and adaptability paramount.
The sustainable growth of industrial practices hinges on the ability to effectively integrate innovative recycling technologies, making readiness and adaptability paramount.
Consumer Perspectives on Catalyst Recycling
The role of consumers in the domain of catalyst recycling can't be understated. Their attitudes, beliefs, and behaviors directly impact the success of recycling initiatives across various industries. Understanding consumer perspectives on catalyst recycling provides insights into not only the acceptance of innovative technologies but also the potential for industry-wide changes toward sustainable practices.
As industries seek to implement direct catalyst recycling, awareness and education among consumers become vital. The more informed consumers are about the significance and benefits of these recycling methods, the more likely they are to support and advocate for such initiatives. This engagement can enhance industry accountability while encouraging companies to adopt more environmentally-friendly practices. Moreover, promoting consumer participation positively influences market dynamics, amplifying demand for recycled materials and sustainable products.
Awareness and Education
Increasing awareness about catalyst recycling is essential for fostering appreciation and understanding of its benefits. Educating consumers about the environmental impact of catalyst disposal and the advantages of recycling can lead to better public support. Educational initiatives should focus on clear and actionable information that highlights how direct recycling reduces waste and conserves resources.
Strategies for education may include:
- Workshops and Seminars: These events can educate the public about the recycling processes, showcasing regional success stories.
- Informative Campaigns: Marketing campaigns can run through online platforms and social media to reach a broader audience. These can include videos, infographics, and articles that simplify complex concepts related to catalyst recycling.
- Partnerships with NGOs: Collaboration with non-governmental organizations can help in spreading educational materials and programs to target audiences.
Public Engagement Initiatives
Public engagement initiatives are critical for fostering a community-oriented approach to catalyst recycling. These initiatives offer a platform where consumers can express their views and contribute ideas. When consumers feel involved, they are more likely to support recycling programs and initiatives.
Examples of effective public engagement include:
- Community Discussions: Hosting forums where community members can openly talk about catalyst recycling can stimulate interest and involvement. Participants can voice opinions, ask questions, and suggest improvements to recycling programs.
- Incentive Programs: Offering incentives for consumers who actively participate in recycling programs can drive higher engagement rates. This may include financial discounts, rewards, or recognition programs for businesses and individuals that promote recycling.
- Social Media Campaigns: Creating online challenges or campaigns can draw attention to the recycling topic and encourage sharing personal experiences or pledges to promote recycling.
Fostering comprehensive consumer perspectives on catalyst recycling is not just about creating awareness; it's about initiating a shift in societal values toward sustainability.
Fostering comprehensive consumer perspectives on catalyst recycling is not just about creating awareness; it's about initiating a shift in societal values toward sustainability.
In summary, integrating consumer perspectives into catalyst recycling initiatives is essential for driving change. By focusing on education and engagement, stakeholders can ensure that consumers are not only aware but also active participants in promoting sustainable practices.
Closure: The Path Forward
In this discourse on direct catalyst recycling, the implications of its adoption are profound. The ongoing shift towards sustainability is not merely an option but a necessity. Direct catalyst recycling presents the critical opportunity to enhance efficiency while significantly reducing waste. As industries face increasing scrutiny over their environmental footprints, the integration of innovative recycling methods becomes essential for both compliance and ethical responsibility.
Strengthening the Sustainability Agenda
A key element in progressing towards a sustainable future lies in understanding and implementing direct catalyst recycling. The environmental benefits are clear: it lowers the consumption of raw materials and minimizes waste.
- Resource Conservation: By recovering catalysts, industries can limit the extraction of virgin materials.
- Energy Efficiency: Recycled catalysts often require less energy to produce and use compared to their newly synthesized counterparts.
- Emission Reduction: The recycling processes can lead to lower greenhouse gas emissions, contributing to climate change mitigation.
Thus, strengthening the sustainability agenda includes not just adopting practices, but also institutionalizing innovations in recycling technologies. The focus must remain on research collaboration and the development of standards that support sustainable practices. The commitment to sustainability in catalyst management can yield significant advantages across various industries.
Call to Action for Researchers and Practitioners
The evolving landscape of catalyst recycling demands that researchers and practitioners alike take proactive steps.
- Invest in Research: It is vital that funding and resources be directed towards exploring new recycling techniques and improving existing methods.
- Foster Collaboration: Partnerships between academia and industry can help bridge knowledge gaps, facilitating technology transfer and innovation.
- Promote Education: Training programs can equip future professionals with the necessary skills, ensuring that the workforce is prepared to implement sustainable practices effectively.
Ultimately, a collaborative approach can drive advancements in direct catalyst recycling. Engaging diverse stakeholders can amplify efforts and bring about substantial change in the implementation of sustainable chemical practices.
The way forward is shaped by collective awareness and committed action, aimed at achieving a balance between industrial growth and ecological preservation.