Exploring Carbon Fiber Additive Manufacturing
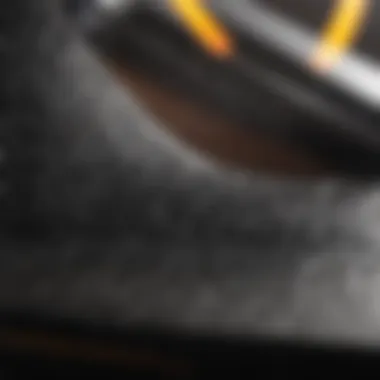
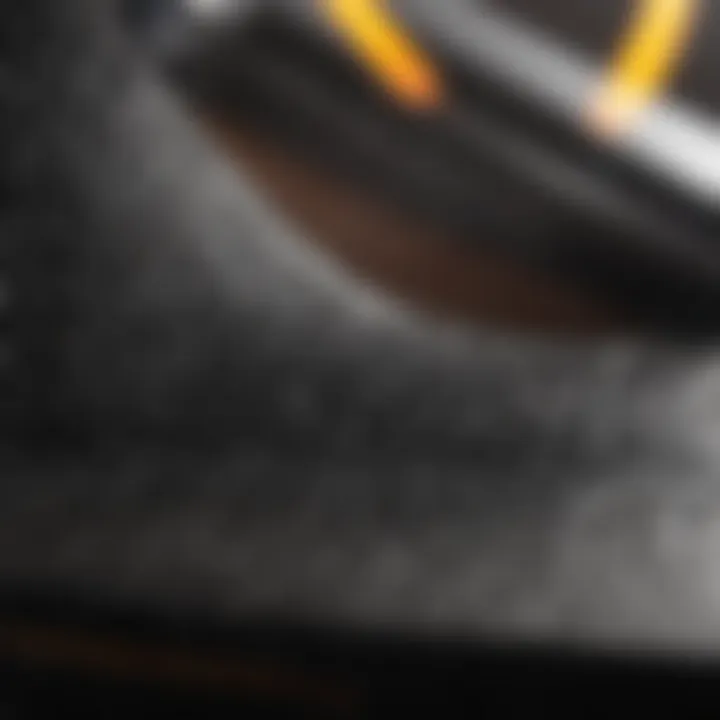
Article Overview
Purpose of the Article
This article aims to present a comprehensive analysis of carbon fiber additive manufacturing. The objective is to examine the technological framework that forms its basis, highlight the unique properties of carbon fiber composites, and discuss a variety of applications across industries such as aerospace, automotive, and healthcare. Furthermore, it seeks to provide insights into the current opportunities and challenges within this innovative field, setting the stage for future developments.
Relevance to Multiple Disciplines
Carbon fiber additive manufacturing is increasingly relevant across a broad spectrum of disciplines. The intersection of materials science and engineering is evident as new technologies emerge. Additionally, it impacts industries where performance, weight, and durability are crucial. Therefore, professionals in engineering, manufacturing, and research can derive immense value from understanding the principles and potentials of carbon fiber composites.
Research Background
Historical Context
The journey of carbon fiber composite materials dates back to the 1960s when researchers first developed them for specialized uses in aerospace and military applications. Over the decades, advancements have propelled these materials into wider industries, driven by their unique properties such as high strength-to-weight ratios. This historical perspective provides the foundation for understanding contemporary development in additive manufacturing processes.
Key Concepts and Definitions
To navigate this topic effectively, a few key terms require clarification:
- Carbon Fiber: A material consisting of thin strands of carbon atoms bonded together, known for its strength and lightweight characteristics.
- Additive Manufacturing: A layered production method that builds objects from 3D model data, often referred to as 3D printing.
- Composite Material: A combination of two or more materials that when combined result in properties superior to those of the individual components.
- Filament: The precursor material used in 3D printing, in the context of carbon fiber, it is typically a plastic polymer reinforced with carbon fiber.
By laying this groundwork, the article intends to guide readers through the complexities of carbon fiber additive manufacturing, elucidating its significance in the modern manufacturing landscape.
Prolusion to Carbon Fiber Additive Manufacturing
Understanding carbon fiber additive manufacturing is crucial in today's industrial landscape. This method is not just about producing parts; it represents a paradigm shift in how we think about design and engineering. The incorporation of carbon fiber enhances the structural integrity of printed objects, enabling lighter alternatives to traditional manufacturing. This allows industries to develop more efficient products, which is particularly valuable in sectors such as aerospace and automotive where weight reduction directly impacts performance and fuel efficiency.
Definition and Overview
Carbon fiber additive manufacturing integrates carbon fiber materials with additive manufacturing technologies, commonly known as 3D printing. This process involves creating objects layer by layer, using materials that include carbon fiber composites. The result is a finished product that combines the best properties of carbon fiber—high strength-to-weight ratio, durability, and resistance to environmental degradation. As a term, additive manufacturing describes a range of techniques, including fused deposition modeling and selective laser sintering, which facilitate the precise construction of complex geometries.
Historical Perspective
The journey of carbon fiber and additive manufacturing dates back several decades. Carbon fiber itself was developed in the mid-20th century, primarily for aerospace applications. Its introduction marked a significant advancement in material science, allowing engineers and designers to explore new possibilities. In the 1980s and 1990s, additive manufacturing began to gain traction, initially focused on prototyping. Over time, advancements in technology led to the combination of these fields. This amalgamation opened a new chapter, enabling the use of carbon fiber composites in additive manufacturing. As research progressed, industries recognized the potential benefits and started integrating these methodologies into production lines, significantly evolving manufacturing processes.
Understanding Carbon Fiber Materials
Understanding carbon fiber materials is crucial in comprehending the entire scope of carbon fiber additive manufacturing. Carbon fiber, recognized for its unique properties, plays a pivotal role in various industries due to benefits like high strength-to-weight ratio and resistance to corrosion.
The importance of carbon fiber extends to its ability to enhance structural integrity while minimizing the overall weight of components. By integrating these materials into additive manufacturing processes, manufacturers can innovate designs that were previously deemed too complex or impossible. This creates opportunities to develop lighter, more robust products that improve energy efficiency, particularly in automotive and aerospace applications.
Properties of Carbon Fiber
Carbon fiber exhibits several notable properties that distinguish it from conventional materials. These include:
- High Strength: Carbon fiber possesses incredible tensile strength, which contributes to its use in applications where durability is critical.
- Lightweight: Weighing significantly less than metals such as steel, carbon fiber supports the creation of lightweight components without sacrificing performance.
- Stiffness: It exhibits excellent rigidity, retaining shape under stress, which is essential in sensitive engineering applications.
- Corrosion Resistance: Carbon fiber is resistant to many chemicals and environmental conditions, offering longevity in various applications.
These attributes make carbon fiber a standout in today's manufacturing landscape, especially within the domains of additive manufacturing. When combined with advanced techniques, these properties can be leveraged to build intricate designs that traditional fabrication methods struggle to produce.
Comparison with Traditional Materials
When comparing carbon fiber with traditional materials like steel and aluminum, several factors become evident:
- Weight: Carbon fiber is much lighter. This reduction in weight can lead to energy savings in transport and reduced material costs in production.
- Strength: While steel is strong, carbon fiber provides a better strength-to-weight ratio, making it preferable for applications requiring lightweight structures without compromising on strength.
- Flexibility in Design: Traditional materials often limit design possibilities due to their physical characteristics. Carbon fiber materials allow for innovative designs with complex geometries, enabling additive manufacturing to reach its full potential.
- Cost Considerations: While the initial cost of carbon fiber may be higher than traditional materials, its durability and lightweight properties can result in overall cost savings. Thus, when assessing long-term benefits, carbon fiber often proves more economical in high-performance contexts.
"Carbon fiber, while initially costly, presents a compelling case for its application within industries demanding high strength and low weight."
"Carbon fiber, while initially costly, presents a compelling case for its application within industries demanding high strength and low weight."
Additive Manufacturing Technologies
Additive Manufacturing Technologies represent a pivotal advancement in modern industrial practices. These methods, significantly transformed by innovations, offer unique advantages in producing complex shapes and lightweight structures using materials like carbon fiber. The core importance of these technologies lies in their ability to create tailored components that traditional processes struggle to manufacture. The suitability of additive manufacturing in the realm of carbon fiber composites drives numerous industries, enhancing flexibility and efficiency.
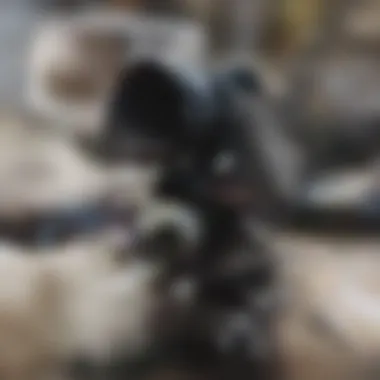
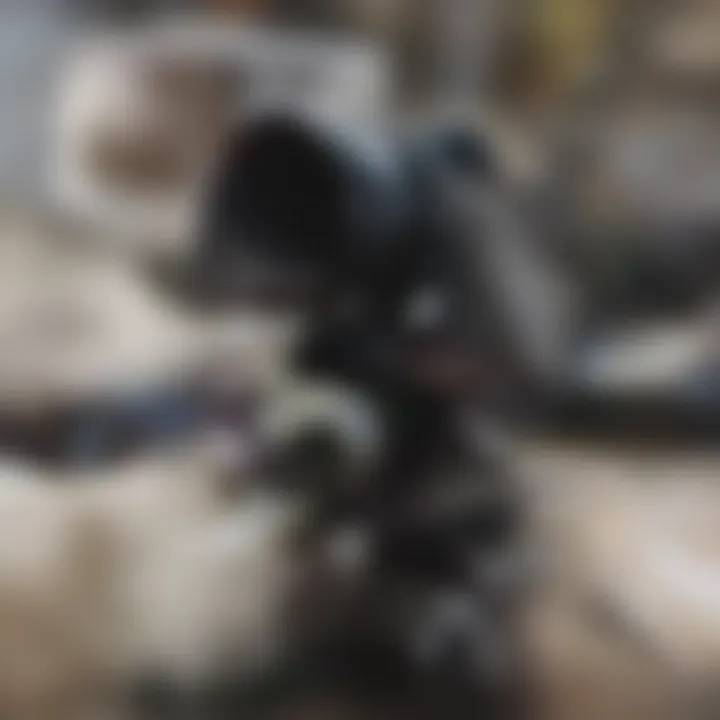
Fused Deposition Modeling (FDM)
Fused Deposition Modeling or FDM is one of the most prevalent additive manufacturing processes. This technique involves extruding melted thermoplastic materials through a heated nozzle. The material solidifies quickly upon cooling, allowing for the layer-by-layer construction of the desired object. FDM is particularly favorable due to its simplicity and relatively low cost.
In the context of carbon fiber additive manufacturing, FDM prepares composite filaments that blend carbon fibers with a thermoplastic matrix. These filaments enhance the overall mechanical properties of the produced parts. FDM allows engineers to design lighter structures without compromising strength, a crucial factor in industries like aerospace and automotive.
Key Benefits of FDM include:
- Accessibility: Easier adoption due to lower initial costs for machines.
- Material Versatility: Works with a variety of thermoplastics that can contain carbon fibers.
- Scalability: Suitable for both small-scale prototypes and larger production runs.
Selective Laser Sintering (SLS)
Selective Laser Sintering is a powerful additive manufacturing technique employing a high-powered laser to fuse powdered materials, like nylon or other polymers, together. SLS is notable for its ability to create complex geometries that traditional machining cannot achieve. While generally utilized with more conventional materials, advancements have introduced carbon fiber-reinforced powders into the SLS realm.
This method produces durable and heat-resistant parts with excellent dimensional accuracy. The introduction of carbon fiber into SLS not only improves mechanical properties but also provides lightweight solutions suitable for demanding applications. Its layerwise consolidation method makes last parts robust enough for many industrial uses, especially in aerospace and automotive sectors.
Advantages of SLS include:
- Design Freedom: Allows intricate designs absent in conventional manufacturing.
- Rapid Prototyping: Accelerates development cycles through quick iterations.
- No Supports Required: The unsintered powder supports the part during the process, eliminating additional support structures.
Continuous Filament Fabrication (CFF)
Continuous Filament Fabrication, or CFF, serves as a distinct additive manufacturing method. Unlike FDM, which works with short strands of filament, CFF utilizes continuous strands of carbon fiber embedded into thermoplastic matrices. The integration of continuous fibers results in parts exhibiting significantly enhanced mechanical properties, especially in tensile strength.
CFF's strength lies in its capacity to produce true composite parts directly without additional post-processing. This allows manufacturers to create highly optimized components for specific applications in various fields. With this method, the potential for lightweight and strong components becomes practical, aligning seamlessly with the needs of advanced industries.
Notable aspects of CFF include:
- Superior Strength-to-Weight Ratio: Ideal for applications requiring both durability and reduced mass.
- Process Efficiency: Streamlines manufacturing by combining infusion and deposition in one step.
- Adaptive Design Capability: Easily tailored to meet unique engineering requirements, fitting modern design challenges.
Continuous improvement in additive manufacturing technologies fuels the potential for carbon fiber applications across multiple industries, emphasizing efficiency, customization, and performance.
Continuous improvement in additive manufacturing technologies fuels the potential for carbon fiber applications across multiple industries, emphasizing efficiency, customization, and performance.
Applications of Carbon Fiber Additive Manufacturing
The applications of carbon fiber additive manufacturing serve as a testament to its capabilities and versatility. This technology has found its footing across multiple industries, demonstrating its potential to redefine production methodologies. With the integration of carbon fiber into additive processes, manufacturers achieve a balance between weight, strength, and design flexibility. Each application not only highlights the material's beneficial properties but also underscores specific considerations that must be addressed during implementation.
Aerospace Industry
In the aerospace sector, the demand for lightweight yet strong materials is paramount. Carbon fiber additive manufacturing allows for the creation of complex geometries and structures that would be impossible to achieve with traditional manufacturing methods. For instance, components such as brackets, enclosures, and even larger airframe parts can be produced with enhanced performance characteristics.
The benefits of using carbon fiber in aerospace are numerous. It contributes to weight reduction, which translates directly into fuel efficiency and increased payload capacity. Moreover, the design flexibility of additive manufacturing permits engineers to optimize performance by tailoring material distribution according to stress and loads, enhancing structural integrity. Notably, companies such as Boeing and Airbus have already begun incorporating these methods, realizing significant reductions in the cost and time needed for prototyping and production.
Automotive Applications
The automotive industry is also experiencing a paradigm shift thanks to carbon fiber additive manufacturing. With the ongoing push for electric and hybrid vehicles, reducing vehicle weight has become crucial for efficiency and performance. Carbon fiber composites are lighter than traditional materials, offering manufacturers a way to enhance fuel economy while ensuring durability.
Recent advancements allow for the production of customized parts tailored to specific vehicle models or user preferences. Parts such as dashboard components, brackets, and even entire body panels can be 3D printed with carbon fiber. This not only reduces excess material waste but also allows for rapid prototyping, enabling quicker time-to-market.
Many automotive manufacturers are now exploring this technology as a means to remain competitive. Brands like BMW and Ford have successfully developed lightweight components with carbon fiber that bring unique advantages in performance and sustainability.
Biomedical Innovations
In the biomedical field, carbon fiber additive manufacturing holds groundbreaking promise. The ability to customize medical devices, implants, and prosthetics to the patient's specific needs represents a leap forward in personalized medicine. Carbon fiber’s biocompatibility and strength-to-weight ratio make it ideal for creating implants that integrate seamlessly with the human body.
Devices such as orthopedic implants, dental applications, and surgical tools benefit significantly from this technology. For example, custom prosthetic limbs can be produced at a fraction of the cost and time compared to traditional methods. Additionally, the precise control over the manufacturing process allows for the fabrication of complex internal structures that can improve function.
"The intersection of carbon fiber with additive manufacturing creates new avenues for innovation across industries, reshaping traditional paradigms in production and design."
"The intersection of carbon fiber with additive manufacturing creates new avenues for innovation across industries, reshaping traditional paradigms in production and design."
For further reading on carbon fiber's impact, please visit Britannica and Wikipedia.
Advantages of Carbon Fiber Additive Manufacturing
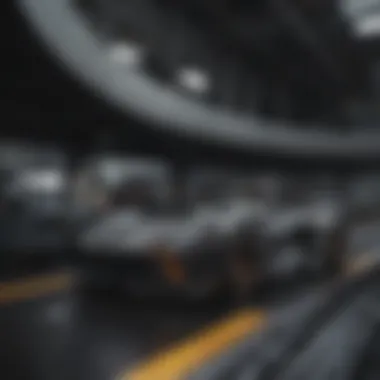
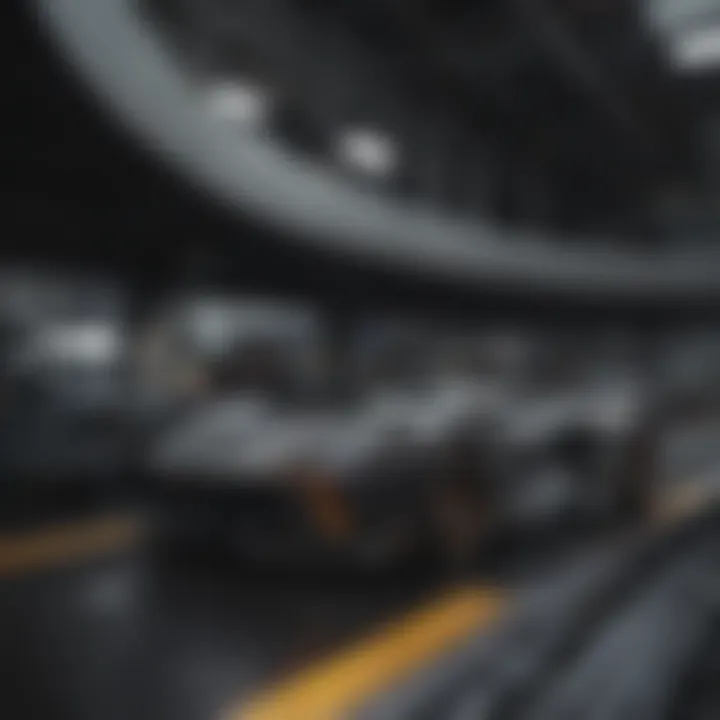
Exploring the advantages of carbon fiber additive manufacturing reveals why this technology is gaining traction across diverse industries. The benefits it provides include significant weight reduction, increased design flexibility, and enhanced cost-effectiveness. Understanding these elements is crucial for those considering its potential applications in various fields.
Weight Reduction
One of the standout advantages of carbon fiber additive manufacturing is its impact on weight reduction in products. Carbon fiber materials are known for their high strength-to-weight ratio. This characteristic allows manufacturers to develop components that are both lighter and strong. For industries like aerospace, where every gram counts, using lighter materials can lead to improved fuel efficiency and reduced operational costs. In automotive sectors, lighter cars can enhance performance and efficiency, further emphasizing the importance of this technology.
Research indicates that substituting traditional materials with carbon fiber can lead to reductions in weight by as much as 50%. This kind of reduction is significant in high-performance applications where weight efficiency translates to tangible benefits.
Design Flexibility
Carbon fiber additive manufacturing offers unparalleled design flexibility. Unlike conventional manufacturing methods, which may impose restrictions based on material form and tooling, 3D printing allows for intricate shapes and structures. This capability enables engineers and designers to push the boundaries of creativity without the typical constraints.
Customizations become much simpler with additive processes. Parts can be produced to exact specifications or modified directly from digital files. This is particularly beneficial in sectors like biomedical applications where tailored solutions are often necessary. The ability to iterate quickly reduces time to market and answers the demand for unique, custom parts, all while maintaining structural integrity and performance.
Cost-Effectiveness
While initial material costs for carbon fiber may be higher, the long-term economic advantages of carbon fiber additive manufacturing cannot be overlooked. The reduced need for machining and secondary processes can lower production costs significantly. Shorter production times contribute to overall savings by allowing for faster turnarounds.
Moreover, the minimal waste associated with additive manufacturing further enhances cost-effectiveness. Traditional manufacturing often results in excess material being cut away, whereas 3D printing creates components layer by layer, utilizing only what is required. These financial benefits position carbon fiber additive manufacturing as a competitive option despite the upfront investment in specialized materials and machinery.
"The weight efficiency and design freedom brought by carbon fiber additive manufacturing present a forward path for engineering innovation."
"The weight efficiency and design freedom brought by carbon fiber additive manufacturing present a forward path for engineering innovation."
Challenges in Carbon Fiber Additive Manufacturing
Carbon fiber additive manufacturing presents numerous opportunities, but it also faces significant challenges that must be understood and addressed. Recognizing these challenges is essential for professionals and researchers in the field as they navigate the complexities of this evolving technology. Focusing on specific elements such as technical limitations, regulatory hurdles, and material costs provides a clearer perspective on the obstacles currently hindering widespread adoption and optimization of carbon fiber in additive processes.
Technical Limitations
The production of components using carbon fiber in additive manufacturing is constrained by several technical limitations.
One primary issue is the complexity of the printing process itself. Carbon fiber composites often require specific printer settings and conditions, which may not be achievable with all machines. High precision machines, like those from Markforged, may be necessary to achieve optimal results.
Another limitation involves the materials used. Not all carbon fiber filaments manage to maintain their strength and integrity during the printing process. This leads to a potential compromise in the durability of the final product, which is particularly problematic in industries such as aerospace and automotive where performance is crucial.
Additionally, the layer adhesion in 3D printed components poses challenges. Achieving proper bond strength between printed layers is critical, as inadequate adhesion can result in weak points in the structure.
Regulatory Hurdles
Navigating the regulatory landscape is another daunting challenge in carbon fiber additive manufacturing. Industries like aerospace and biomedical are subject to strict regulations that ensure safety and reliability. The introduction of new materials and processes often requires extensive testing and certification.
For instance, the Federal Aviation Administration (FAA) has established guidelines that manufacturers must follow to ensure the safety and effectiveness of aircraft components. This can lead to delays in the adoption of new technology.
Regulatory compliance not only demands significant resources but can also slow down innovation. Moreover, as the technology evolves quickly, staying updated with current regulations requires ongoing effort and can struggle to keep pace with advancements in carbon fiber applications.
Material Costs
Material costs are a vital aspect to consider in carbon fiber additive manufacturing. The expense associated with high-quality carbon fiber filament is considerable, especially when compared to conventional materials like PLA or ABS. This economic factor can deter businesses from exploring carbon fiber options, particularly for low-volume applications where cost-efficiency is crucial.
Additionally, the sourcing of carbon fiber materials can be a challenge. Reliable suppliers that offer quality fibers at competitive prices are not always easy to find, creating bottlenecks in production.
Finally, it's essential to account for the long-term cost implications. While carbon fiber could lead to lightweight and robust components that offer performance benefits, the initial material investment may be seen as a barrier by some manufacturers.
"Understanding the full spectrum of challenges in carbon fiber additive manufacturing is essential for advancement in the industry."
"Understanding the full spectrum of challenges in carbon fiber additive manufacturing is essential for advancement in the industry."
Future Directions in Carbon Fiber Additive Manufacturing
The potential of carbon fiber additive manufacturing is vast and continues to evolve. As industries seek lighter yet stronger materials, advancements in this field are critical. Future directions in this technology not only promise innovation but also raise considerations for practical application and implementation. Companies and researchers are increasingly interested in how these advancements can impact production efficiency, material performance, and environmental sustainability.
Emerging Technologies
Emerging technologies in the realm of carbon fiber additive manufacturing hold great promise. Innovations such as digital light processing and multi-material additive manufacturing allow for more complex geometries and functionalities. These processes facilitate a higher precision in the layering of carbon fiber composites, which can lead to better mechanical properties and enhanced performance.
For instance, companies like Markforged and 3D Systems are pioneering methods to integrate carbon fiber into existing production techniques. This not only allows them to deliver customizable solutions but also enhances the integrity and durability of the final products. With the integration of artificial intelligence and machine learning, the optimization of the printing process can also be achieved.
Key emerging technologies include:
- Direct Energy Deposition (DED) - This method allows for rapid prototyping and complex shapes.
- Robotic Arm Printing - With this, the printing can take place in various orientations, leading to better design possibilities.
- Hybrid Systems - Mixing additive and subtractive manufacturing offers versatility in design and finishing.
The engagement of these emerging technologies is a vital step forward, as they not only improve the capacity for complex designs but may also reduce waste and resource consumption in the production process.
Research and Development Trends
Research and development play an integral role in shaping the future of carbon fiber additive manufacturing. Trends indicate a growing interest in optimizing materials for specific applications. Current research focuses on improving the quality and performance of carbon fiber composites used in various industries.

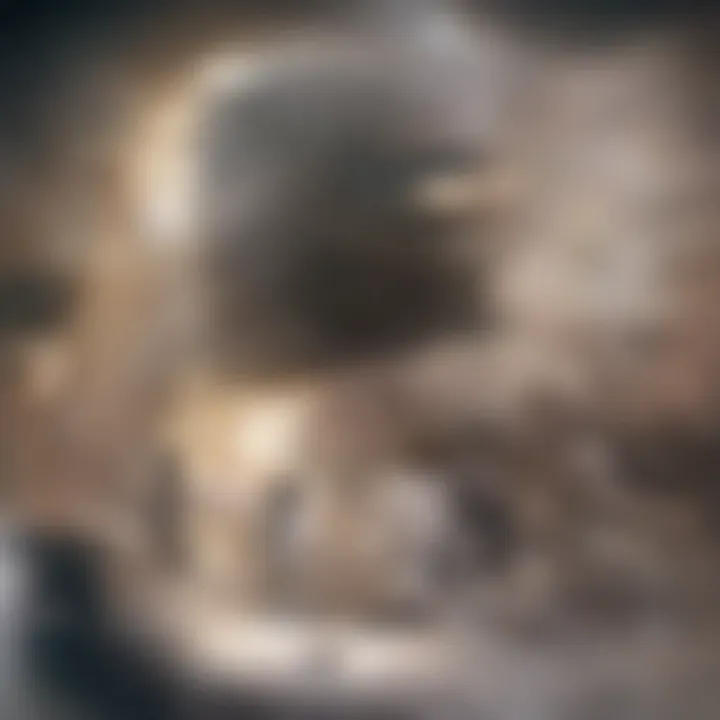
Studies emphasize on creating hybrid materials that blend carbon fiber with other polymers. This could lead to materials that possess both toughness and flexibility, ideal for a range of applications from aerospace to sports equipment. Additionally, the exploration of bio-based and recyclable materials is gaining traction. This reflects a broader trend towards sustainability in manufacturing practices.
Industry players are also focusing on:
- Scalability - Finding ways to up-scale additive processes to meet large-scale production demands.
- Cost reduction - Streamlining methods to bring down the costs associated with carbon fiber manufacturing.
- Standardization - Developing guidelines to ensure quality and reliability in products produced through additive methods.
The interplay of these trends will dictate how carbon fiber additive manufacturing adapts to future challenges and opportunities.
"Carbon fiber's potential in additive manufacturing can redefine performance benchmarks across industries"
"Carbon fiber's potential in additive manufacturing can redefine performance benchmarks across industries"
The exploration of these directions is crucial for a better understanding of how carbon fiber technologies can shape efficient manufacturing processes, reinforcing their place in innovative applications.
Case Studies in Carbon Fiber Additive Manufacturing
Case studies in carbon fiber additive manufacturing are essential as they provide tangible examples of how this technology is transforming industries. By examining real-world applications, one gains insight into the practical benefits and challenges of implementing carbon fiber 3D printing. These case studies serve as valuable resources for understanding best practices, potential pitfalls, and the overall impact on various sectors. The relevance of this topic extends to students, researchers, educators, and professionals who seek to grasp both the theoretical concepts and their practical ramifications in the market.
Successful Applications
The application of carbon fiber additive manufacturing has been most prominently observed in the aerospace and automotive industries. In the aviation sector, companies like Boeing have started utilizing carbon fiber components in their aircraft designs. The use of advanced materials reduces weight and increases fuel efficiency, essential for meeting contemporary aviation standards.
Similarly, within the automotive arena, brands such as BMW and Ford are experimenting with carbon fiber-reinforced parts. These can withstand high stress while maintaining a light profile, enabling performance improvements. Moreover, companies like Stratasys have produced successful prototypes using carbon fiber, which can lead to rapid production and testing cycles. Such applications demonstrate not just the ability to produce high-performance components but also the efficiency in moving through design and manufacturing phases.
Lessons Learned
Case studies also reveal important lessons regarding the integration of carbon fiber additive manufacturing into traditional processes. A common theme across many examples is the importance of thorough planning and understanding of material properties. Successful case studies highlight that an intimate knowledge of carbon fiber behavior during the additive manufacturing process is crucial for achieving structural integrity and performance requirements.
Additionally, engaging collaborative aspects among engineering, design, and production teams is critical. For instance, a project undertaken by General Electric in the energy sector showed that close collaboration facilitated innovation while overcoming technical challenges.
Moreover, one crucial lesson learned is the need for adaptability. As the industry continues to evolve, manufacturers must remain open to adopting new technologies and materials. In some cases, early adopters faced challenges due to limited knowledge and training regarding their equipment, which resulted in production delays. Addressing this situation involves ongoing education about best practices in carbon fiber additive manufacturing.
In summary, the examination of real-world case studies in carbon fiber additive manufacturing offers insights into its vast potential while also uncovering the considerations necessary for successful implementation across industries.
Impact on Industry Standards
The impact of carbon fiber additive manufacturing on industry standards cannot be overstated. As this technology evolves, it reshapes existing frameworks and establishes new benchmarks for quality and safety. The integration of carbon fiber materials into additive manufacturing processes presents unique challenges and opportunities that drive the need for robust industry standards. A clear set of guidelines is essential for ensuring product reliability and consistency across various applications, including aerospace and biomedical sectors.
Certification Processes
Certification processes play a crucial role in the adoption of carbon fiber additive manufacturing. They provide the necessary validation that products meet established quality and safety requirements. Typical certification includes assessment of materials, production processes, and end-user products. For instance, the Federal Aviation Administration (FAA) has specific guidelines relating to the use of composite materials in aerospace manufacturing. Compliance with standards like these assures stakeholders of material performance and regulatory adherence.
- ISO Certification: Organizations may seek ISO standards to demonstrate compliance with international best practices. Effective certification improves marketability and builds trust.
- Industry-Specific Criteria: Different sectors may require unique certification. For example, biomedical applications often necessitate additional testing to meet health and safety regulations.
The process of certification often requires thorough documentation and testing, which can be resource-intensive. However, this initial investment is vital for establishing credibility in the market.
Quality Assurance Measures
Quality assurance measures are essential in maintaining the integrity of carbon fiber additive manufacturing. These measures help monitor and control production processes to ensure consistent output quality. Key methods often include:
- Process Monitoring: Continuous monitoring of manufacturing parameters such as temperature and pressure can help detect anomalies early in the production process.
- Material Testing: Routine testing of raw materials and finished products ensures they meet specified strength and durability levels. Implementing standard tests such as tensile and compressive strength assessments is crucial.
- Feedback Mechanisms: Setting up systems for real-time feedback from post-production analysis can identify areas of improvement and help adapt processes to emerging needs or technology advancements.
Quality assurance is not merely a compliance requirement; it is a prerequisite for innovation and trusted performance in carbon fiber additive manufacturing.
Quality assurance is not merely a compliance requirement; it is a prerequisite for innovation and trusted performance in carbon fiber additive manufacturing.
Closure
The conclusion of this article serves to encapsulate the wealth of information regarding carbon fiber additive manufacturing. It is crucial as it not only summarizes the main findings but also reflects on the potential that these manufacturing methods hold for various industries. Understanding this topic helps in recognizing the transformative impact of carbon fiber composites on contemporary manufacturing processes.
Summary of Key Points
- Technological Foundations: The article highlights the diverse additive manufacturing technologies, including Fused Deposition Modeling, Selective Laser Sintering, and Continuous Filament Fabrication. Each technology offers unique benefits and challenges, making the selection process vital for specific applications.
- Material Properties: The properties that make carbon fiber attractive, such as strength-to-weight ratio and corrosion resistance, were discussed. Comparisons with traditional materials illustrate its advantages in various contexts.
- Applications Across Industries: Insights into the aerospace, automotive, and biomedical sectors showcase the versatility of carbon fiber in applications ranging from structural components to innovative medical devices.
- Advantages and Challenges: While there are significant advantages like weight reduction and design flexibility, challenges such as technical limitations and material costs were also examined.
- Future Directions: Emerging technologies and ongoing research trends indicate a promising future for carbon fiber additive manufacturing, suggesting increased adoption across multiple sectors.
This summary is essential for grasping the holistic view provided throughout the article. Each point not only highlights the significance of carbon fiber additive manufacturing but also encapsulates the critical elements for understanding its role in shaping the future of manufacturing.
The Road Ahead
Looking forward, the road ahead for carbon fiber additive manufacturing appears bright yet complex. Continuous research and development is key to tackling existing challenges. Innovations in materials science will further expand the possibilities of carbon fiber applications. Ongoing collaboration between academia and industry will foster advancements, pushing the boundaries of what can be achieved with additive manufacturing technologies.
The future also necessitates an emphasis on sustainability. Eco-friendly practices and materials will become more important as the industry seeks to minimize environmental impacts. Regulatory frameworks must adapt to facilitate safe and effective integration of new technologies into production processes.